-
- News
- Books
Featured Books
- pcb007 Magazine
Latest Issues
Current IssueSales: From Pitch to PO
From the first cold call to finally receiving that first purchase order, the July PCB007 Magazine breaks down some critical parts of the sales stack. To up your sales game, read on!
The Hole Truth: Via Integrity in an HDI World
From the drilled hole to registration across multiple sequential lamination cycles, to the quality of your copper plating, via reliability in an HDI world is becoming an ever-greater challenge. This month we look at “The Hole Truth,” from creating the “perfect” via to how you can assure via quality and reliability, the first time, every time.
In Pursuit of Perfection: Defect Reduction
For bare PCB board fabrication, defect reduction is a critical aspect of a company's bottom line profitability. In this issue, we examine how imaging, etching, and plating processes can provide information and insight into reducing defects and increasing yields.
- Articles
- Columns
- Links
- Media kit
||| MENU - pcb007 Magazine
Estimated reading time: 1 minute
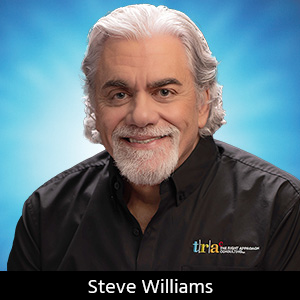
The Right Approach: Quick & Easy 6S to Reduce Handling Issues
Introduction
Handling is often the source of many pain points for PCB fabricators, resulting in rework, scrap and customer returns. Quick & Easy 6S is a fantastic tool to minimize handling risk by reducing product travel and improving shop cleanliness.
6S Methodology
6S (Figure 1) is literally five Japanese words beginning with the letter S, plus Safety, which together form a systematic process for organizing a workplace. While this may seem to be a minor tool in the war on waste, the benefits include quality and safety improvements, leadtime reduction, reducing hidden waste, and of course, increased profits. Below we will explore what the six Ss are and why they are important.
Sort (Seiri): Ensuring each item in a workplace is in its proper place or identified as unnecessary and then removed; it’s simply getting rid of unnecessary stuff.
Questions to ask:
Can this task be simplified?
Do we label items properly and dispose of waste frequently?
Set in Order (Seiton): Arrange materials and equipment so that they are easy to find and use. Prepare and label storage areas using paint, tape, outlines, or color-codes. Shadow boards are a great way to identify the type and location of tools (Figure 2).
Questions to ask:
How much time is spent looking for things and putting things away?
Can we improve the ergonomics of this task?
Shine (Seiso): Repair, clean and shine work area; in other words, “everyone is a janitor” (this is a concept that U.S. workers have a difficult time embracing!). Aside from any safety or health risks, employees honestly perform better in a neat and clean environment.
Editor's Note: This article originally appeared in the May 2016 issue of The PCB magazine.
More Columns from The Right Approach
The Right Approach: ‘Twas the Night Before Christmas (Harley-style)The Right Approach: I Hear the Train A Comin'
The Right Approach: Culture Change is Key to a QMS
The Right Approach: Leadership 101—Be a Heretic, Not a Sheep
The Right Approach: Leadership 101—The Law of Legacy
The Right Approach: Leadership 101: The Law of Explosive Growth
The Right Approach: Leadership 101—The Law of Timing
The Right Approach: The Law of Sacrifice