-
- News
- Books
Featured Books
- smt007 Magazine
Latest Issues
Current IssueMoving Forward With Confidence
In this issue, we focus on sales and quoting, workforce training, new IPC leadership in the U.S. and Canada, the effects of tariffs, CFX standards, and much more—all designed to provide perspective as you move through the cloud bank of today's shifting economic market.
Intelligent Test and Inspection
Are you ready to explore the cutting-edge advancements shaping the electronics manufacturing industry? The May 2025 issue of SMT007 Magazine is packed with insights, innovations, and expert perspectives that you won’t want to miss.
Do You Have X-ray Vision?
Has X-ray’s time finally come in electronics manufacturing? Join us in this issue of SMT007 Magazine, where we answer this question and others to bring more efficiency to your bottom line.
- Articles
- Columns
- Links
- Media kit
||| MENU - smt007 Magazine
Condensation Testing—A New Approach
August 2, 2016 | Chris Hunt and Ling Zou, National Physical Laboratory, and Phil Kinner, Electrolube LtdEstimated reading time: 20 minutes
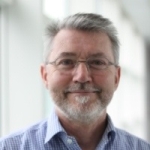
Conformal coatings are applied to protect electronic assemblies from adventitious environmental factors, which include, corrosive gases and fluids and high humidity. Whenever there is a significant level of humidity, there is always the opportunity for parts of the assembly to drop beneath the dew point, thus resulting in the formation of condensed water on the surface of the assembly, which can significantly reduce the insulation resistance of the boards surface, resulting in malfunctioning electronics.
While the characterization of coating performance under high humidity conditions is detailed, in well accepted IPC and IEC standards, the performance and testing under condensing conditions is not so well developed.
This situation largely reflects the hardware challenge. Most humidity chambers are designed to achieve stable, well controlled humidity and temperature conditions, but none of these offer condensing options. Therefore, the user has to improvise. A common approach to attempt to achieve condensing conditions is to ramp at a fast enough rate to cause condensation, a feature the humidity chamber designers have by and large, successfully managed to remove. Alternatively chambers run very close to 100% relative humidity and hence at this condition condensation will occur in various parts of the chamber. An immediate drawback of these approaches is that chambers of different designs will perform differently, and will be sensitive to small drops in cooling performance.
There are many alternative approaches to achieving condensation, and these are described in ISO, IEC, ASTM and others, and commonly attempt to drive a chamber into producing condensation, against the anticipated use condition, and hence sensors in the chamber detect the additional moisture and will work to reduce the humidity level to the required set-point. Thus, the level of experimental control will be very dependent on the chamber performance, and variability across chamber manufacturers can be expected.
A new approach has been developed where the test board is mounted on a substrate whose temperature can be independently controlled without changing the ambient condition. Thus, the temperature of the test board can be depressed below ambient to any desired point and hence, produce condensation at different levels. It is then, therefore, straightforward to cycle between condensing and non-condensing conditions on the test board in a constant ambient environment. The technique has been demonstrated to be repeatable and controllable, with the user able to select a temperature differential that matches their worst in-use conditions, or to understand the performance of their system under a range of condensing conditions.
The data for a range of conformal coatings are presented, and correlated back to the conformal coating material type, and coverage and thickness by cross-sectioning.
Introduction
Condensation is the change of physical state of matter from the gas phase to the liquid phase. It is most often caused when gaseous matter is in contact with a substrate that is at a lower temperature. The temperature at which condensation will form is known as the dew point. The dew point is the temperature at which the water vapor in a sample of air at constant barometric pressure condenses into liquid water at the same rate at which it evaporates. At temperatures below the dew point, water will leave the air. The condensed water is commonly called dew when it forms on a solid surface.
All things being equal, as the temperature falls, the relative humidity rises, reaching 100% at the dew point, at least at substrate level. The dew point temperature is never greater than the ambient temperature, since the relative humidity cannot exceed 100%.
The dew point then, is the saturation temperature for water in air, and the dew point will be dependent on the relative humidity. A high relative humidity implies that the dew point is closer to the current air temperature. Relative humidity of 100% indicates the dew point is equal to the current temperature and that the air is maximally saturated with water. When the moisture content remains constant and temperature increases, relative humidity decreases.
Conformal coatings are thin, polymeric coatings, intended to preserve the condition of a printed circuit board (PCB) under a wide range of operating environments, including high humidity, corrosive gases, dust and other contaminants.
Conformal coatings are often evaluated in high humidity environments, typically 40°C/93% RH, 65°C/ 95% RH or 85°C and 85% RH. Until recently, little attention has been paid to the characteristics of conformal coatings under condensing environments. Table 1 shows the dew point at several conditions, including those of the common evaluation test methods.
The results in Figure 12 show that the two polyurethane coatings behave in a very similar mode as shown in Figure 10. The nano coating results are not shown here as they also performed similarly to before. However, now the two acrylic results are different, with the single coated acrylic showing a large drop in SIR, indicating that the corners of the tracks are not covered. Supporting this conclusion, the image in Figure 13 shows corrosion at the track edge, and with corrosion products forming across the top of the coating between the anode and cathode. The acrylic-1 results show the SIR dropping to 106Ω from the first condensation event, with the behavior remaining broadly consistent through the following condensation cycles. With the double coated acrylic, the SIR results are not as bad, but SIR values are dropping below 108Ω, and with a trend of decreasing SIR with each condensation cycle. The 1oz copper SIR pattern boards the results in Figure 9 do not show any difference between the single and double coated boards, but with the 3oz copper SIR pattern boards the results do show a clear difference, and furthermore the acrylic coating can be seen to failing in either single or double coated condition. Hence the geometry challenge of the 3oz copper tracks for the acrylic-1 coating has been shown by it failing the condensation test. From above this coating passed the humidity test at 40°C/93%RH, and the same coating with the 1oz copper tracks also passed. Thus the incremental geometry challenge and the fine control of the condensing condition in this experimental arrangement allows detailed and robust characterization of coating performance.
As can be seen, the dewpoint is within a few degrees of the ambient conditions at all of these conditions. At 30°C and 90% RH, a common enough condition in South East Asia, and North East America for example, the dewpoint is only 28°C (i.e., if the substrate is just 2°C cooler than the ambient air, condensation can begin to form).
As condensation proceeds from the formation of droplets and then coalescence to the formation of a continuous water layer, with the surface then saturated, it is essentially the same as if it were submerged in water, although there will not be the same dilution effect of ionic contamination. Conformal coatings are known to protect poorly in such immersion conditions.
Page 1 of 6
Suggested Items
Electrolube Showcases Unrivalled Electronics Protection Solutions for EV, EM at productronica India
09/07/2022 | ElectrolubeElectrolube will be showcasing new solutions from their extensive encapsulation resin, thermal management and conformal coating portfolios in Hall 14 stand PB55 at productronica India, held on September 21-23 at the India Expo Mart in Greater Noida.
Electrolube’s Polyurethane Resin A Success for Tier 1 Automotive Supplier
07/07/2022 | ElectrolubeMacDermid Alpha Electronics Solutions is pleased to announce a successful collaboration between its electro-chemicals brand, Electrolube, and a tier 1 automotive supplier.
Electrolube’s UL94V-0 Approved Alternative to 3M Novec 2702 Electronic Grade Coating
05/23/2022 | ElectrolubeElectrolube, a brand of MacDermid Alpha Electronics Solutions has formulated a Conformal Coating (FPC) specifically to resolve a number of issues experienced by a specific user of surface modifier materials.
MacDermid Alpha Appoints New Global Product Managers For Electrolube Brand Resins and Coatings
04/01/2022 | MacDermid Alpha Electronics SolutionsMacDermid Alpha Electronics Solutions, a global supplier of integrated solutions from our Circuitry, Assembly and Semiconductor divisions that provides unmatched capabilities in electronics design and manufacturing, has announced the appointments of Saskia Hogan and Beth Massey as new Global Product Managers for the Electrolube brand.
MacDermid Alpha’s Electrolube Awarded NextGen Best Paper
02/03/2022 | MacDermid Alpha Electronics SolutionsMacDermid Alpha Electronics Solutions, a global supplier of integrated solutions from our Circuitry, Assembly and Semiconductor divisions that provides unmatched capabilities in electronics design and manufacturing, is pleased to announce that Electrolube’s Senior Technical Manager, Beth Turner, has been awarded NextGen Best Paper.