-
- News
- Books
Featured Books
- pcb007 Magazine
Latest Issues
Current IssueInventing the Future with SEL
Two years after launching its state-of-the-art PCB facility, SEL shares lessons in vision, execution, and innovation, plus insights from industry icons and technology leaders shaping the future of PCB fabrication.
Sales: From Pitch to PO
From the first cold call to finally receiving that first purchase order, the July PCB007 Magazine breaks down some critical parts of the sales stack. To up your sales game, read on!
The Hole Truth: Via Integrity in an HDI World
From the drilled hole to registration across multiple sequential lamination cycles, to the quality of your copper plating, via reliability in an HDI world is becoming an ever-greater challenge. This month we look at “The Hole Truth,” from creating the “perfect” via to how you can assure via quality and reliability, the first time, every time.
- Articles
- Columns
- Links
- Media kit
||| MENU - pcb007 Magazine
Factors Affecting the Adhesion of Thin Film Copper on Polyimide
September 6, 2016 | David Ciufo, Hsin-Yi Tsai and Michael J. Carmody, INTRINSIQ MATERIALSEstimated reading time: 2 minutes
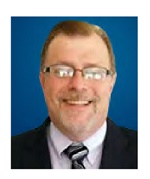
Abstract
The use of copper foils laminated to polyimide (PI) as flexible printed circuit board precursor is a standard practice in the PCB industry. We have previously described an approach to very thin copper laminates of coating uniform layers of nano copper inks and converting them into conductive foils via photonic sintering with a multi-bulb conveyor system, which is consistent with roll-to-roll manufacturing. The copper thickness of these foils can be augmented by electroplating. Very thin copper layers enable etching fine lines in the flexible circuit. These films must adhere tenaciously to the polyimide substrate. In this paper, we investigate the factors which improve and inhibit adhesion. It was found that the ink composition, photonic sintering conditions, substrate pretreatment, and the inclusion of layers (metal and organic) intermediate between the copper and the polyimide are important.
Ink factors include the intensity of photonic sintering. Better sintering leads to better cohesive strength of the nano copper layer. The ink solvent and the dispersant used to suspend the nanoparticles are significant both for adhesion and the colloidal stability of the dispersion. Pretreatment of the substrate by plasma roughening did not improve adhesion. We describe the effects of chromium and nickel interlayers which are typically used in standard foil laminates. Finally, we describe the types of peel strength testing used to assess adhesion.
Introduction
The goal of our ultra-thin film project is to create a thin (1−2 micron) film of uniform copper on flexible polyimide for application to flex circuits. Ultra-thin films allow very narrow copper lines on patterns created by photolithography, plating, and etching. Figure 1 depicts the invented process.
A very thin layer of nano copper ink is created on polyimide by coating techniques. A picture of a coating made in a roll-to-roll (R2R) manner on a slot die coating machine is shown at left in Figure 2. After drying the ink (done by air impingement here), a film of copper nanoparticles in dispersant/binder of about 0.5−1.0 microns thick is produced. This film can be turned into a continuous film of conductive copper metal by photonic sintering with a flash lamp system. There have been developed special R2R machines with moving conveyors, multiple flash bulbs, and algorithms to control and interleave flashes to give uniform sintering of the coating[2]. On the other hand, the lab scale coatings are made by using an automatic Mayer bar coater (Figure 2, right), dried in a vacuum oven, and sintered by a single flash lamp unit it the lab. The resulting copper films are less uniform than the ones generated by the R2R process, and banding where the flashes overlap is usually observed. Alternatively, a uniform conductive copper film can be generated by sintering by immersing in a formic acid/argon reducing atmosphere at 190°C for an hour (Figure 3).
Editor's Note: This article originally appeared in the August 2016 issue of The PCB Magazine.
Testimonial
"We’re proud to call I-Connect007 a trusted partner. Their innovative approach and industry insight made our podcast collaboration a success by connecting us with the right audience and delivering real results."
Julia McCaffrey - NCAB GroupSuggested Items
How Good Design Enables Sustainable PCBs
08/21/2025 | Gerry Partida, Summit InterconnectSustainability has become a key focus for PCB companies seeking to reduce waste, conserve energy, and optimize resources. While many discussions on sustainability center around materials or energy-efficient processes, PCB design is an often overlooked factor that lies at the heart of manufacturing. Good design practices, especially those based on established IPC standards, play a central role in enabling sustainable PCB production. By ensuring designs are manufacturable and reliable, engineers can significantly reduce the environmental impact of their products.
50% Copper Tariffs, 100% Chip Uncertainty, and a Truce
08/19/2025 | Andy Shaughnessy, I-Connect007If you’re like me, tariffs were not on your radar screen until a few months ago, but now political rhetoric has turned to presidential action. Tariffs are front-page news with major developments coming directly from the Oval Office. These are not typical times. President Donald Trump campaigned on tariff reform, and he’s now busy revamping America’s tariff policy.
Global PCB Connections: Understanding the General Fabrication Process—A Designer’s Hidden Advantage
08/14/2025 | Markus Voeltz -- Column: Global PCB ConnectionsDesigners don’t need to become fabricators, but understanding the basics of PCB fabrication can save you time, money, and frustration. The more you understand what’s happening on the shop floor, the better you’ll be able to prevent downstream issues. As you move into more advanced designs like HDI, flex circuits, stacked vias, and embedded components, this foundational knowledge becomes even more critical. Remember: the fabricator is your partner.
MKS’ Atotech to Participate in IPCA Electronics Expo 2025
08/11/2025 | AtotechMKS Inc., a global provider of enabling technologies that transform our world, announced that its strategic brands ESI® (laser systems) and Atotech® (process chemicals, equipment, software, and services) will showcase their latest range of leading manufacturing solutions for printed circuit board (PCB) and package substrate manufacturing at the upcoming 17th IPCA Show to be held at Pragati Maidan, New Delhi from August 21-23, 2025.
MKS Showcases Next-generation PCB Manufacturing Solutions at the Thailand Electronics Circuit Asia 2025
08/06/2025 | MKS Instruments, Inc.MKS Inc, a global provider of enabling technologies that transform our world, today announced its participation in Thailand Electronics Circuit Asia 2025 (THECA 2025), taking place August 20–22 at BITEC in Bangkok.