All About Flex: Lead-Free Soldering Flexible Circuits
September 22, 2016 | Dave Becker, All FlexEstimated reading time: 3 minutes
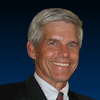
Ever since the European community adopted the RoHS directive in 2006, the U.S. electronics industry has been steadily increasing its use of lead-free solder. Medical was the first U.S. industry to go totally lead-free. Today, a significant percentage of electronics soldering is done with lead-free solder. After several years of refinement and withstanding some mischaracterizations, lead-free soldering is proving to be cost effective and reliable.
While lead-free solder is reliable, there are differences in materials and processing that need to be understood to ensure a robust electronics design.
Material Composition: The most widely used lead-free solder paste is a tin/silver/copper alloy (Sn/Ag/Cu). These are available in slightly different combinations; the following are the more common ones:
- Sn96.5/Ag3.0/Cu0.5
- Sn95.5/Ag3.8/Cu0.7
- Sn95.5/Ag4.0/Cu0.5
There are alloys other than tin/silver/copper that can be used for lead-free soldering; most of these are for non-electronic applications. The optimal choice of alloy depends on the type of surface to solder and the application for the flexible circuit.
Cosmetic Appearance: The classic tin-lead solder joints were shiny and smooth. In fact, a defective solder joint often had a dull, rough appearance. This is not the case for lead-free solder joints, which have a less shiny appearance. Those who are not familiar with lead-free solder will immediately flag the dull appearance as defective joints. The dull appearance in solder joints is not indicative of the quality of the solder joint, but simply due to the inherent properties of the alloy. See Figure 1 for a side-by-side comparison.
Figure 1: Lead-free vs. tin-lead. (Source: CEDOS Electronics)
Process Temperature: Lead-free solder starts to reflow around 218°C, whereas tin-lead solder will reflow around 188°C. The higher temperature can have an adverse impact on the fixtures, equipment and materials used on a flexible circuit. When introducing a new part number requiring lead-free solder, an engineering review should occur to insure all materials have proper temperature compatibility.
Mechanical Strength: Lead-free solder does not have the mechanical strength of the traditional tin-lead solder. This is one of the reasons that the lead-free is not used in military or aerospace applications. The RoHS directive exempts military and some aerospace products. While tin-lead solder has better mechanical properties, there are ways to address mechanical strength issues with lead-free solder. Adding epoxy or conformal coating to reinforce the bond areas are ways to add robustness to designs requiring a high level of mechanical strength.
Flux: As with tin-lead soldering, there are two basic types of fluxes used with lead-free soldering: water washable flux and no-clean flux. The water washable flux must be completely removed after soldering. Water wash generally works well if there is adequate room under the components to rinse away residue. If the component density and profile do not allow thorough rinsing, then no-clean flux should be used. No-clean flux leaves a visible residue, which some may find objectionable. There may be a temptation to require residue removal with a cleaning process. But experts advise against removing the residue of a no-clean flux. No-clean flux residue is designed to encapsulate any contaminants that could potentially cause electrical problems in the field. By cleaning the no-clean flux, there is risk some of the contaminants will remain and create potential reliability problems.
Testing: Reliability and electrical testing are the same for both lead-free and tin-lead soldering processes. There are a couple of tests to determine if a given component has lead. One is to apply a chemical that simply changes color if there is lead in the solder. One could also use an atomic absorption spectrophotometer that will provide the exact content of the metal. These tests are mainly applicable to ensure an incoming product is lead-free, or to prove that a product meets RoHS requirements. During circuit fabrication, in-process material control should insure solder paste is lead-free.
An electronic packaging designer who is unfamiliar with lead-free processes will need to be educated on the various design, material, process, component and inspection nuances that lead-free soldering presents. Many circuit suppliers are able to provide a significant amount of design support for applications requiring lead-free solder.
Dave Becker is vice president of sales and marketing at All Flex Flexible Circuits LLC.
Testimonial
"Our marketing partnership with I-Connect007 is already delivering. Just a day after our press release went live, we received a direct inquiry about our updated products!"
Rachael Temple - AlltematedSuggested Items
Indium Corporation Promotes Two Leaders in EMEA (Europe, Middle East, and Africa) Markets
08/05/2025 | Indium CorporationWith its commitment to innovation and growth through employee development, Indium Corporation today announced the promotions of Andy Seager to Associate Director, Continental Sales (EMEA), and Karthik Vijay to Senior Technical Manager (EMEA). These advancements reflect their contributions to the company’s continued innovative efforts with customers across Europe, the Middle East, and Africa (EMEA).
MacDermid Alpha Electronics Solutions Unveils Unified Global Website to Deepen Customer, Talent, and Stakeholder Engagement
07/31/2025 | MacDermid Alpha Electronics SolutionsMacDermid Alpha Electronics Solutions, the electronics business of Elements Solutions Inc, today launched macdermidalpha.com - a unified global website built to deepen digital engagement. The launch marks a significant milestone in the business’ ongoing commitment to delivering more meaningful, interactive, and impactful experiences for its customers, talent, and stakeholders worldwide.
KOKI to Showcase Analytical Services and New HF1200 Solder Paste at SMTA Guadalajara 2025
07/31/2025 | KOKIKOKI, a global leader in advanced soldering materials and process optimization services, will exhibit at the SMTA Guadalajara Expo & Tech Forum, taking place September 17 & 18, 2025 at Expo Guadalajara, Salón Jalisco Halls D & E in Guadalajara, Mexico.
Weller Tools Supports Future Talent with Exclusive Donation to SMTA Michigan Student Soldering Competition
07/23/2025 | Weller ToolsWeller Tools, the industry leader in hand soldering solutions, is proud to announce its support of the upcoming SMTA Michigan Expo & Tech Forum by donating a limited-edition 80th Anniversary Black Soldering Set to the event’s student soldering competition.
Koh Young Appoints Tom Hattori as President of Koh Young Japan
07/21/2025 | Koh YoungKoh Young Technology, the global leader in True 3D measurement-based inspection solutions, announced the appointment of Tom Hattori as President of Koh Young Japan (JKY).