Food Additive Key to Environmentally Friendly, Efficient, Plastic Solar Cells
September 30, 2016 | North Carolina State UniversityEstimated reading time: 1 minute
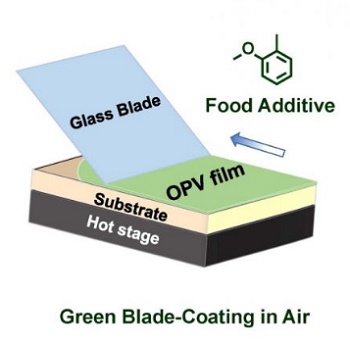
Researchers from North Carolina State University and the Chinese Academy of Sciences have created an efficient, semi-printed plastic solar cell without the use of environmentally hazardous halogen solvents. These solar cells can be manufactured at room temperature, which has implications for large-scale commercial production.
Plastic solar cells, or organic photovoltaics, are popular because they are lightweight, flexible, transparent and inexpensive to manufacture, making them useful in multiple applications. Unfortunately, the halogen-containing solvents used in their manufacture are an obstacle to large-scale commercialization. These solvents are key to making sure that the solar cell’s morphology, or structure, maximizes its energy efficiency; however, they are environmentally hazardous. Additionally, the use of these harsh chemicals requires a controlled environment, which adds to production costs.
Long Ye, a postdoctoral research scholar in physics at NC State and lead author of a paper describing the work, wanted to find out if nontoxic solvents could provide equally efficient morphology in the manufacturing process. Ye and his colleagues developed a proof of concept semi-printed plastic solar cell that utilized o-methylanisole (o-MA) as the solvent. O-MA is a commonly used flavoring agent in foods, and is nontoxic to humans.
Schematic illustration and chemical structure of semi-printed plastic solar cells in air, using food additive o-MA as solvent.
Image credit: Long Ye, NC State
The researchers used soft X-ray techniques to study the morphology of their solar cell. They found that the o-MA based solar cell had similar morphology, crystalline features and device performance to those produced by halogenated solvents. The solar cell’s overall efficiency rating was around 8.4 percent. Furthermore, their cell could be produced via blade coating at ambient, or room temperature. Blade coating is a process that uses a glass blade to spread a thin layer of the photovoltaic film onto either a rigid or flexible substrate, and the process is compatible with large-scale commercial manufacturing.
“Two of the key requirements for mass producing these solar cells are that the cells can be produced in the open air environment and that the process doesn’t pose health or environmental hazards,” Ye says. “Hopefully this work can help pave the way for printing solar cells in ambient air.”
Suggested Items
KYZEN to Spotlight Stencil Cleaning Solutions at SMTA Oregon
05/02/2025 | KYZEN'KYZEN, the global leader in innovative environmentally friendly cleaning chemistries, will exhibit at the SMTA Oregon Expo & Tech Forum, scheduled to take place on Tuesday, May 20 at the Wingspan Event and Conference Center in Hillsboro, OR. KYZEN’s cleaning expert Jeff Deering will be on-site at the expo providing information about stencil cleaning chemistries, including KYZEN E5631J.
LG Innotek to Build FC-BGA into 700 Million USD Business with State-of-the-art Dream Factory
05/01/2025 | PR NewswireLG unveiled the Dream Factory, a hub for the production of FC-BGAs (Flip Chip Ball Grid Arrays), the company's next-generation growth engine, to the media for the first time and announced it on the 30th April.
Siemens, Intel Foundry Advance Collaboration
04/30/2025 | Siemens Digital Industries SoftwareSiemens Digital Industries Software announced that its continued collaboration with Intel Foundry has resulted in multiple product certifications, updated foundry reference flows, and additional technology enablement leveraging the foundry’s leading-edge technologies for next-generation integrated circuits (IC) and advanced packaging.
The Knowledge Base: Unlocking the Invisible—The Critical Role of X-ray Technology
04/29/2025 | Mike Konrad -- Column: The Knowledge BaseFrom detecting voids under BGAs to solder defects in high-reliability applications, X-ray inspection has become an indispensable tool in modern manufacturing. But how is the technology evolving? What challenges do experts face in deploying X-ray inspection effectively and what does the future hold for this critical quality assurance method?
KOKI Expands U.S. Sales Coverage with Multiple New Representatives
04/29/2025 | KOKIKOKI, a global leader in advanced soldering materials and process optimization services, is pleased to announce the expansion of its U.S. sales network with the addition of three new manufacturers’ representative firms: Assembled Product Specialists, Diversitech Reps Inc., and Eagle Electronics.