-
- News
- Books
Featured Books
- pcb007 Magazine
Latest Issues
Current IssueInventing the Future with SEL
Two years after launching its state-of-the-art PCB facility, SEL shares lessons in vision, execution, and innovation, plus insights from industry icons and technology leaders shaping the future of PCB fabrication.
Sales: From Pitch to PO
From the first cold call to finally receiving that first purchase order, the July PCB007 Magazine breaks down some critical parts of the sales stack. To up your sales game, read on!
The Hole Truth: Via Integrity in an HDI World
From the drilled hole to registration across multiple sequential lamination cycles, to the quality of your copper plating, via reliability in an HDI world is becoming an ever-greater challenge. This month we look at “The Hole Truth,” from creating the “perfect” via to how you can assure via quality and reliability, the first time, every time.
- Articles
- Columns
- Links
- Media kit
||| MENU - pcb007 Magazine
Estimated reading time: 3 minutes
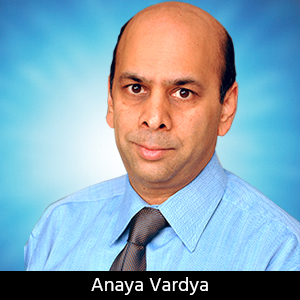
LED and Metal-Backed Technology—Today and in the Future
Probably one of the hottest, or should I say coolest, technologies today is LED. I would also venture to say it is one of the fastest growing as well. All you have to do is look around you can see evidence of this everywhere from holiday lights in your home and Jumbotrons at sports arenas, to highway and business signage. The lighting industry is now dominated by LED technology.
Our understanding of, and status as experts in LED technology did not come easy. As a matter of fact, it took a number of years before we were able to learn and process all of the basic facets of this technology. In this column, I’d like to share some of the things we have learned.
First, it is critical to work closely with your LED customers. You must have a complete understanding of the parameters of their end product in order to advise them on the best way to design the circuit board for maximum efficiency and heat dissipation. This means that you have to know exactly how much heat the end product is going to be exposed to, including how much the product itself will be producing. By knowing this you the fabricator can determine not only which material to use to fabricate the printed circuits, but also advise the designer on the basic construction of the PCB. I have seen a number of instances, for example, where by choosing the right thermal laminates we were able to avoid having a metal-backed heat dissipation shield completely.
Secondly, we learned that we have to work with our vendors—particularly our laminate vendors—to not only make sure that they have the right thermal products on the shelf today, but also to help them in the development of future new products. Right now, for example, my company has just UL-approved six different new thermal control laminates to be used on our LED, metal back, RF and heavy copper products. It is not only important to let our vendors know what our needs are and will be, it is as critically important to listen to them as well. After all they are the experts of their own products.
Speaking of vendors, we also worked very closely with our solder mask suppliers, seeking their expertise on the best black, and more importantly, white inks to use. This was not easy challenge since these products are seeing a lot of heat, which tends to affect the color of inks. We worked with our vendor on the challenges we had with white solder mask, which tends to turn yellow with heat. But I am glad to say that by working together this problem was solved to the point where we are now getting excellent results using white solder mask on our thermal products.
We are now at a point in our company where we are building literally thousands of LED PCBs every single day, most on them on a quick turn basis, which makes us one of the industry leaders in this technology. But like everything else worth doing we had to meet a lot of challenges to get there.
The key to our success in LED technology comes from working very closely with our customers to get a good understanding of what their end products will look like, and how they will have to perform once out in the field. By keeping an ongoing discourse with vendors, both parties can learn from one other and together, forge a true technology partnership to build the best PCBs possible.
Dave Lackey is vice president of business development at American Standard Circuits.
More Columns from Standard of Excellence
Standard of Excellence: Training Your Team to Excel in Customer ServiceStandard of Excellence: Delivering Excellence—A Daily Goal
Standard of Excellence: The Role of Technology in Enhancing the Customer Experience
Standard of Excellence: Turning Negative Customer Feedback Into Positive Outcomes
Standard of Excellence: Anticipating Customer Needs Early and Often
Standard of Excellence: The Power of Personalization in Customer Care
Standard of Excellence: Building Trust with Customers—The Foundation of Excellent Service
Standard of Excellence: Finding and Developing Future Leaders in Manufacturing