-
- News
- Books
Featured Books
- pcb007 Magazine
Latest Issues
Current IssueInventing the Future with SEL
Two years after launching its state-of-the-art PCB facility, SEL shares lessons in vision, execution, and innovation, plus insights from industry icons and technology leaders shaping the future of PCB fabrication.
Sales: From Pitch to PO
From the first cold call to finally receiving that first purchase order, the July PCB007 Magazine breaks down some critical parts of the sales stack. To up your sales game, read on!
The Hole Truth: Via Integrity in an HDI World
From the drilled hole to registration across multiple sequential lamination cycles, to the quality of your copper plating, via reliability in an HDI world is becoming an ever-greater challenge. This month we look at “The Hole Truth,” from creating the “perfect” via to how you can assure via quality and reliability, the first time, every time.
- Articles
- Columns
- Links
- Media kit
||| MENU - pcb007 Magazine
Estimated reading time: 4 minutes
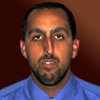
Welcome Your Product to the Real World!
The days, weeks, and (sometimes) years that go into a product’s development usually are incomprehensible to the lay person. Like laws and sausages, no one wants to really understand what has gone on behind the scenes to make your “thing” a reality. They just care that your widget makes their life easier and/or more enjoyable!
With that, design and development kick off the process which eventually takes your widget from a “light bulb” idea all the way to actual production, but ultimately the testing that has been performed along the way shapes your widget into something that is reliable and thus more attractive to your customer.
At the core of this reliability-based testing is exposure of your widget to various potentially harmful environments. These potentially devastating environments help designers and engineers identify weaknesses in the product and, hopefully, identify ways to make your widget better! Generally speaking, there are two main categories of reliability exposures—mechanical and climatic. This is not to say that there are not other types of harmful environments; like an exposure to hazardous vapors or subjecting your widget to electromagnetic interference, but mechanical and climatic are the more traditional types and we’ll explore those in a bit more detail in this column.
Mechanical Exposures
Generally speaking, mechanical test exposures involve hitting your widget with a large singular force or with a smaller repeated force at a high frequency. The large singular force exposure is traditionally referred to as a mechanical shock, whereas the repeated force at high frequency is traditionally referred to as vibration.
For mechanical shock, the widget is typically dropped from a specific height, onto a hard surface, with the widget checked for functionality pre- and post-exposure. Further, these types of shocks can be repeated or increased / decreased in magnitude, dependent on the application or ultimate end use. From a simulation standpoint, mechanical shock testing would be the equivalent of knocking your widget off your desk, or possibly dropping your widget down the stairs.
For vibration, the widget is mounted to a table that has the ability to move a relatively small distance laterally at a high frequency. This high-speed movement exposes the widget to a vibrational stress. In terms of simulation, this type of exposure is designed to determine how the widget might perform when bolted to something like a jet engine or a clothes dryer. The widget is typically operated during the exposure, so its performance can be monitored under the real world conditions.
Climatic Exposures
This category actually has some sub-categories, as a spectrum of exposures are possible when delving into this realm. Of typical interest in the world of climatic exposure would be the following categories: temperature, humidity, and weathering.
Temperature extreme testing is always of interest in respect to reliability. This testing can be done at a single extreme temperature (elevated or sub-ambient) or with both extremes, the latter of which being commonly referred to as thermal shock testing. For thermal shock, the testing exposes your widget to temperatures well above and well below normal atmospheric conditions in a cyclic process. The extremes in these temperatures can commonly vary from 150°C all the way down to -75°C with many other options in between and above and beyond. As for the exposure itself, the cyclic nature of the testing—physically transferring the widget from hot to cold—results in a thermal stress being applied to the device under test.
During the exposure, the widget can be monitored for functionality or it can be simply tested pre- and post-exposure. In respect to simulation, cyclic thermal excursions are common for many things in the real-world and could show how your widget survives a hike up a mountain, where the temperature at elevated altitude could be very different than on the ground where you started, or how it might survive in the engine compartment of an auto mobile, where the temperature will cycle from ambient conditions up to the temperature of the engine itself.
Humidity testing is usually performed in conjunction with elevated temperature testing and is thus commonly referred to as temperature / humidity testing. Humidity levels of 60% to 95% RH are common for this type of testing, along with temperature levels from 30°C to 85°C. The environment is very harsh—hot and wet!—and is commonly used to explore the reliability of electronic-based widgets, such as what might happen if you took your GPS deep into the jungles of Brazil! Common tests like surface insulation resistance (SIR) and electrochemical migration (ECM) are performed in an attempt to promote an electrical issue for the widget that will cause it to malfunction. In terms of evaluation, pre- and post-exposure testing and/ or monitoring while at conditions are common ways to check reliability.
Weathering type exposures are commonly centered around light effects. Commonly referred to as UV or Xenon Arc exposures, these types of tests expose your widget to a variety of light spectra…as if your widget had been left out in the sun too long! The main variables in this type of testing are the irradiance level (which can be thought of as the light intensity) and the test duration. Pre- and post-exposure testing is very common to determine what effect, if any, the light exposure has had on your widget. These tests could be related to visual characteristics, such as color and gloss, or mechanical properties, such as flexibility and tensile strength.
Ultimately, exposure of your widget to environmental stress testing is a key step in the development process of any product and the establishment of a reliability strategy to access the potential weaknesses, as a function of environment, for your widget is critical to its long-term success.
Editor's Note: This column originally appeared in the August 2016 issue of The PCB Magazine.
More Columns from Let's Talk Testing
Let’s Talk Testing: Professor Plum in the Library with the Candlestick…Right?Random Thoughts on Employment, from Both Sides of the Table…
Let's Talk Testing: You’re in for a (Thermal) Shock!
Let's Talk Testing: How Strong is Your Foundation?
Got Whiskers?
Let's Talk Testing: Are You Getting What You’ve Asked for?
Vias for Dummies
Don’t Reinvent the Wheel—Find an Expert!