Mr. Laminate Tells All: The Certification of IPC-4101D Polyimide Base Materials: Buyer Beware
November 22, 2016 | Doug Sober, Essex Technologies GroupEstimated reading time: 4 minutes
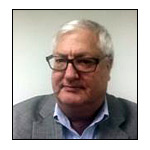
At the most recent IPC meeting held in Rosemont, Illinois, one of the hot topics of discussion at the Laminate and Prepreg Subcommittee was the three polyimide specification sheets. The header portion for the three polyimide-based copper-clad laminates and prepregs are shown in Figure 1, for easy comparison of polyimide grades.
Here is a quick summary of the composition and glass transition temperature:
When IPC-4101 was originally conceived, the idea was to have materials with similar chemistry, similar performance and similar processing covered by a single specification sheet. This was by design to make materials covered by one specification sheet to be interchangeable by the board shop. However, it is hard to imagine that an epoxy modified polyimide with a Tg of 200°C minimum would have the same performance and processing through the printed wiring board process as a pure polyimide with a Tg of 240°C minimum.
It has been brought to the attention of the IPC Technical Activities Executive Committee (TAEC) that some confusion exists in the industry about the header requirements in IPC-4101D WAM1. More specifically that some base material suppliers are certifying specification Sheet 42, comprised of a blend of polyimide and epoxy resins, for specification sheets numbered 40 and 41 which are supposed to be pure polyimides. The reverse is also being practiced for certification purposes. It seems that some suppliers feel any polymide-based material can be certified to any of the three specification sheets if the Tg and peel strength requirements are met.
An argument supporting the practice was that when the epoxy and the polyimide react with the curing agent, there is only one big molecule with the largest portion being the polyimide functionality. So it is a pure polyimide at that point. That argument does not hold any water with UL which uses a formulated constituent list provided by the base material supplier to determine the listing program needed. Nor is this logic used by the Greenpeace organization when discussing reacted-in tetrabromo-bisphenol A with epoxy. The sum of the parts is important but that is not the way the industry looks at chemical compositions of base materials for the electronics industry.
Other suppliers using their own rules for substitutions just say, “You (IPC) cannot stop us.” I guess the buyer must be beware of the substitution practices of their suppliers. If anyone would like to discuss this further with me, please contact me through the address provided below.
Figure 1: IPC-4101D Polymide specification sheets.
This is not to say that some substitutions are not needed, especially for the epoxy specification sheets. During the last IPC meeting held in Rosemont (IPC Fall Committee Meetings, 2016, Rosemont, Illinois), the 3-11 Laminate/Prepreg Materials Subcommittee finalized a substitution table found in Figure 2. This table shows which specification sheets can be substituted for others. For example, specification sheet 26 can be certified with base materials that can be certified with 126 or 129. Any substitutions being made outside of this substitution table are not considered valid by IPC.
Figure 2: Permissible material substitutions.
Other interesting developments from the IPC meeting in Rosemont was the new IPC-4101E proposal. This document would be essentially the current IPC-4101D with Amendment 1 and Amendment 2 already included. The most important element of IPC-4101E is the inclusion of an Appendix A which describes more strict requirements for contamination in copper-clad laminates. These requirements have been pushed by the European Space Agency (ESA).
There was great resistance to putting these requirements into the body of IPC-4101 as another Quality Class. Customers tend to ask for the most stringent class possible regardless of whether they need it or not. So the Laminate/ Prepreg Subcommittee put it in as an Appendix A. Appendix A must be called out on the purchase order for the higher level of cleanliness to be in effect for the material. The group also decided to move this requirement into a new document in the future called IPC-4101 SPACE. Once the IPC-4101 SPACE is published, Appendix A will be dropped and a new document published under the name IPC-4101F.
The 3-11 Laminate/Prepreg Materials Subcommittee is always making sure that there are specifications developed which match the publication plan and the needs of the industry. For example, a new specification sheet was proposed for a halogen-free, low Dk and Df material with a Tg of 170°C minimum. This document would be similar to the halogenated specification sheets 72 and 73 in the current IPC-4101D in terms of the performance requirements. So a gap exists in the current IPC-4101D list of specification sheets. The group felt that the requirements as presented were too high or developed around a specific material of just one company. So the group reduced some of the requirements and changed resin 3 from “PPO” to “non-epoxy” to make it more generic and allow more materials to be certified to the proposed specification sheet. The header for this new specification sheet is shown in Figure 3.
Figure 3: IPC-4101D proposed specification sheet.
This new specification sheet again will provide a halogen-free alternative to the brominated specification sheets 72 and 73. We hope to have it included as part of the IPC-4101Revision F document.
The next IPC 3-11 Laminate/Prepreg Materials Subcommittee meeting will be held in San Diego, California, in February 2017.
Doug Sober is the president of Essex Technologies Group and may be reached by clicking here.
Testimonial
"We’re proud to call I-Connect007 a trusted partner. Their innovative approach and industry insight made our podcast collaboration a success by connecting us with the right audience and delivering real results."
Julia McCaffrey - NCAB GroupSuggested Items
How Good Design Enables Sustainable PCBs
08/21/2025 | Gerry Partida, Summit InterconnectSustainability has become a key focus for PCB companies seeking to reduce waste, conserve energy, and optimize resources. While many discussions on sustainability center around materials or energy-efficient processes, PCB design is an often overlooked factor that lies at the heart of manufacturing. Good design practices, especially those based on established IPC standards, play a central role in enabling sustainable PCB production. By ensuring designs are manufacturable and reliable, engineers can significantly reduce the environmental impact of their products.
50% Copper Tariffs, 100% Chip Uncertainty, and a Truce
08/19/2025 | Andy Shaughnessy, I-Connect007If you’re like me, tariffs were not on your radar screen until a few months ago, but now political rhetoric has turned to presidential action. Tariffs are front-page news with major developments coming directly from the Oval Office. These are not typical times. President Donald Trump campaigned on tariff reform, and he’s now busy revamping America’s tariff policy.
Global PCB Connections: Understanding the General Fabrication Process—A Designer’s Hidden Advantage
08/14/2025 | Markus Voeltz -- Column: Global PCB ConnectionsDesigners don’t need to become fabricators, but understanding the basics of PCB fabrication can save you time, money, and frustration. The more you understand what’s happening on the shop floor, the better you’ll be able to prevent downstream issues. As you move into more advanced designs like HDI, flex circuits, stacked vias, and embedded components, this foundational knowledge becomes even more critical. Remember: the fabricator is your partner.
MKS’ Atotech to Participate in IPCA Electronics Expo 2025
08/11/2025 | AtotechMKS Inc., a global provider of enabling technologies that transform our world, announced that its strategic brands ESI® (laser systems) and Atotech® (process chemicals, equipment, software, and services) will showcase their latest range of leading manufacturing solutions for printed circuit board (PCB) and package substrate manufacturing at the upcoming 17th IPCA Show to be held at Pragati Maidan, New Delhi from August 21-23, 2025.
MKS Showcases Next-generation PCB Manufacturing Solutions at the Thailand Electronics Circuit Asia 2025
08/06/2025 | MKS Instruments, Inc.MKS Inc, a global provider of enabling technologies that transform our world, today announced its participation in Thailand Electronics Circuit Asia 2025 (THECA 2025), taking place August 20–22 at BITEC in Bangkok.