-
- News
- Books
Featured Books
- pcb007 Magazine
Latest Issues
Current IssueInventing the Future with SEL
Two years after launching its state-of-the-art PCB facility, SEL shares lessons in vision, execution, and innovation, plus insights from industry icons and technology leaders shaping the future of PCB fabrication.
Sales: From Pitch to PO
From the first cold call to finally receiving that first purchase order, the July PCB007 Magazine breaks down some critical parts of the sales stack. To up your sales game, read on!
The Hole Truth: Via Integrity in an HDI World
From the drilled hole to registration across multiple sequential lamination cycles, to the quality of your copper plating, via reliability in an HDI world is becoming an ever-greater challenge. This month we look at “The Hole Truth,” from creating the “perfect” via to how you can assure via quality and reliability, the first time, every time.
- Articles
- Columns
- Links
- Media kit
||| MENU - pcb007 Magazine
Estimated reading time: 4 minutes
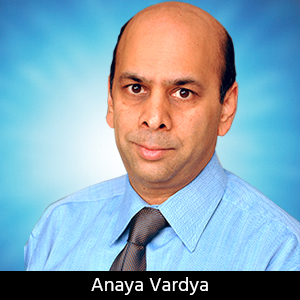
Standard of Excellence: RF Microwave Technology—The Future is Now
Although RF/microwave technology has been around for a considerable amount of time, many people are still not sure exactly what it is. This month, I am going to dedicate my column to explaining exactly what it is, why it is used, and in what products is it used. I’ll also discuss who needs it.
In terms of PCB fabrication, RF/microwave technology is the assemblage of PCB features (traces), dielectrics and spaces designed to function precisely at very short wavelengths/high frequency. In short, extremely tightly controlled conductor widths, thicknesses, copper roughness and dielectric thickness, dielectric constant at a suitably low loss tangent to allow controlled performance at elevated frequency.
Microwave typically refers to operation between 300MHz to 300GHz. But in general, it is an operation in the analog realm at frequencies affecting and or capable of reacting with common dielectric materials. In application, it can be used for anything, but is often utilized for transmission of signals across a space.
As new products are being developed, the need for RF/microwave is taking off due to the advent of wireless communication and data transmission. What has changed in the world to make this a growing technology? The freedom of connectivity and interconnectivity without wires. Wireless is in. Look around you. The new iPhones, for example, don’t even have a plug-in socket for ear buds—they’ve gone wireless. Been to a rock concert lately? Did you wonder where the wires have gone? That’s gone wireless. Pairing your phone to your car radio…wireless. Your printer is now wireless, as are so many other devices. All of them are wireless due to RF/microwave technology. That Bluetooth thing? That’s just another word for wireless. Get the idea? That’s why this technology is in such demand. And we’re just getting started.
And so, you ask, “If we’re just getting started, where are we going with this? How about the future of this technology? Where is it going tomorrow?” I’m far from an industry expert on forecasting future trends, but in general, we can be assured that the future will have an even greater level of connectivity—either peer-to-peer or systems-integrated. This will require the technology and/or infrastructure to support this. I have had discussions with groups interested in expanding the use of RF/MW into intelligent heating and process solutions. Taking what is now a relatively simple technology operating a fixed frequency or band of frequencies and intelligently altering either the frequency or phase to make it act upon materials. It is a very interesting concept.
It should also be noted that there are two somewhat similar, yet divergent technologies developing: the RF and microwave frequency applications, and high-speed data transmission operating almost exclusively in the digital realm. With the advent of the extremely high data rates, as opposed to frequencies, there are becoming many similar requirements between the analog and digital realm when it comes to dielectric loss, consistency and conductor shape and impedance. Then the two diverge when it comes to other aspects. Becoming expert at one can aid in the ability to manufacture products for the other with slightly different critical attributes.
When it comes to designing and fabricating RF/microwave boards there are several things to take into consideration. I feel like a broken record since I say this so often, but involvement of your fabricator’s application engineering resource is key. The earlier the better. Ask as many questions as possible. Try to learn what gives him trouble or more to the point, what represents increased risk. Sometimes this can be a combination of certain technologies within the same design. There may be many things that contribute to this, but they all add to decreased yield and/or performance and ultimately increased cost.
Then when fabricating RF/microwave boards, you first need to understand the application thoroughly. Therefore, direct communication with the design engineers at the conceptual stage is so important. Continuing this work with the board level designers to completely understand all the critical aspects which could have a significant impact on various performance criteria important to the function of the product. In short, understanding exactly what we can do to ensure that the functional design parameters are met. This can be quite complex when factoring in all the various aspects affecting circuit performance: line width, height, position and co-positional relationships, circuit roughness, surface finish, finish thickness, via size, via plating thickness, surface planarity of mixed plating’s or surface finishes. There are also significant differences between normal laminates and those used to produce RF/MW PCBs, the biggest one being the stability or the lack of reaction at higher frequency. If a material reacts at a higher frequency it will tend to absorb or distort the signals in close proximity.
I’ll end by saying one more time that the relationship, or shall we say partnership, between the vendor and the customers—especially that relationship between the designer and the fabricator—cannot be stressed enough. To build a great RF/MW product the fabricator must have a complete and thorough understanding of how this product is going to be used. This is critical.
John Bushie is ASC's application engineering manager and a process engineering specialist.
More Columns from Standard of Excellence
Standard of Excellence: Training Your Team to Excel in Customer ServiceStandard of Excellence: Delivering Excellence—A Daily Goal
Standard of Excellence: The Role of Technology in Enhancing the Customer Experience
Standard of Excellence: Turning Negative Customer Feedback Into Positive Outcomes
Standard of Excellence: Anticipating Customer Needs Early and Often
Standard of Excellence: The Power of Personalization in Customer Care
Standard of Excellence: Building Trust with Customers—The Foundation of Excellent Service
Standard of Excellence: Finding and Developing Future Leaders in Manufacturing