-
- News
- Books
Featured Books
- smt007 Magazine
Latest Issues
Current IssueMoving Forward With Confidence
In this issue, we focus on sales and quoting, workforce training, new IPC leadership in the U.S. and Canada, the effects of tariffs, CFX standards, and much more—all designed to provide perspective as you move through the cloud bank of today's shifting economic market.
Intelligent Test and Inspection
Are you ready to explore the cutting-edge advancements shaping the electronics manufacturing industry? The May 2025 issue of SMT007 Magazine is packed with insights, innovations, and expert perspectives that you won’t want to miss.
Do You Have X-ray Vision?
Has X-ray’s time finally come in electronics manufacturing? Join us in this issue of SMT007 Magazine, where we answer this question and others to bring more efficiency to your bottom line.
- Articles
- Columns
Search Console
- Links
- Media kit
||| MENU - smt007 Magazine
Reducing Warpage on BGAs During Rework
January 9, 2017 | Bob Wettermann, BEST Inc.Estimated reading time: 3 minutes
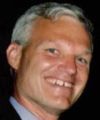
One of the challenges associated with BGA rework has to do with effects of device warpage, which can cause undue shorts or opens post rework. The impact of a lead-free rework process, the continuous "thinning" of the BGA package as well as continued turnaround time pressures of rework all have led to increased propensity of this phenomenon to occur. While most of the failures in the rework process can be captured via visual or x-ray inspection, or some escapes in test can occur. For example, head-in-pillow defects can be caused by the process of the ball being “pulled” out of the oriented paste during the reflow profile. Too much warpage can also create stress on the solder ball joints and lead to reliability failures of the packages (Figure 1).
Figure 1: Typical rework profile and the potential impact of warpage at differing points.
Outside of opens and shorts in the reflowed and reworked BGA, there is a widely accepted analytical technique for measuring the degree of warpage. These measurements are made by coating the part with reflective paint and placing a sheet of low expansion quartz glass etched with equally spaced parallel lines parallel to the sample. A beam of light is then directed onto the quartz glass and the lines create a shadow on the top of the BGA package. When the package becomes warped a Moiré pattern is produced by the geometric interference between the lines on the quartz and the shadow of the lines on the surface. These fringe patterns then can be calibrated and are displayed as 3-D topographical part "map". A typical Shadow Moiré warpage output, from a modern measuring instrument, can be seen below (Figure 2). This method tries to emulate the behavior of the package through a thermal cycle.
Figure 2: Shadow Moiré output showing device warpage. (Courtesy: Akrometrix)
The difference among the components in the BGA (silicon die, the molding compound, substrate, etc.) causes thermal stresses due to the thermal expansion mismatch between the various components. A major reason for warping in area array plastic package is this coefficient of thermal expansion (CTE) mismatch. Using low-CTE advanced thermal materials, it is possible to tailor CTE, reducing this problem. Sometimes underfill is used to provide mechanical support and protection for the dieto-package interconnects. This can minimize thermal stress on the die due to CTE mismatch with the substrate materials.
As a result of the higher lead free processing temperatures in rework, device packages, initially constructed for lead bearing solders are subjected to greater thermal stresses and exhibit a greater propensity to warp. Some research has demonstrated that the impact of a higher processing temperature, versus the molding temperature, of the package material is a direct causal link to the amount of device warpage. As the device packaging for lead free products have become more stable, this impact has been lessened through material changes in typical BGA packages.
The thinning of area array packages, due to the increasing demand to make end devices more portable, has brought the average moisture sensitivity of device packages up. This makes devices more susceptible to thermal damage based on a given heat exposure time. The purpose of the MSD standard is to identify the moisture sensitivity level at a fixed reflow temperature. The user can then properly store and handle the devices, avoiding subsequent thermal/mechanical damage, during the assembly reflow attachment and/or repair operations. The thinning of the device bodies has moved them to higher MSD levels and shorter floor life, thereby exacerbating the warpage problem.
JEDEC Standard Qualification Levels
Time-to-market pressure for repair depots, as well as leaner inventories, have caused additional turnaround stress on PCB rework departments. Many times, this time pressure on BGA rework means taking short cuts when using hot air rework systems. Matching nozzle size to the BGA is important in minimizing the part warping during rework. Using too small of a nozzle requires all the heat to pass thru the part and into the solder joint. This can cause large temperature differentials and result in BGA warping.
There are several process conditions which need to be controlled in order that warped device packages do not become a problem. The greatest areas to control include: profile development, MSD controls and solder paste volume adjustments made during printing.
Good reflow profile management, in terms of extending the heating/cooling profiles longer, will minimize the impact of device warpage. Although this will impact throughput. During the cool down process, if you go too slowly, it will create coarse-grained structures in the solder joint. Additionally, the proper control of temperature differential, across the part during reflow by using a multizone bottomside heater, will reduce the warpage impact.
To read this entire article, which appeared in the January 2017 issue of SMT Magazine, click here.
Suggested Items
SolderKing’s Successful Approach to Modern Soldering Needs
06/18/2025 | Nolan Johnson, I-Connect007Chris Ward, co-founder of the family-owned SolderKing, discusses his company's rapid growth and recent recognition with the King’s Award for Enterprise. Chris shares how SolderKing has achieved these award-winning levels of service in such a short timeframe. Their secret? Being flexible in a changing market, technical prowess, and strong customer support.
Preventing Surface Prep Defects and Ensuring Reliability
06/10/2025 | Marcy LaRont, PCB007 MagazineIn printed circuit board (PCB) fabrication, surface preparation is a critical process that ensures strong adhesion, reliable plating, and long-term product performance. Without proper surface treatment, manufacturers may encounter defects such as delamination, poor solder mask adhesion, and plating failures. This article examines key surface preparation techniques, common defects resulting from improper processes, and real-world case studies that illustrate best practices.
Breaking Silos with Intelligence: Connectivity of Component-level Data Across the SMT Line
06/09/2025 | Dr. Eyal Weiss, CybordAs the complexity and demands of electronics manufacturing continue to rise, the smart factory is no longer a distant vision; it has become a necessity. While machine connectivity and line-level data integration have gained traction in recent years, one of the most overlooked opportunities lies in the component itself. Specifically, in the data captured just milliseconds before a component is placed onto the PCB, which often goes unexamined and is permanently lost once reflow begins.
BEST Inc. Introduces StikNPeel Rework Stencil for Fast, Simple and Reliable Solder Paste Printing
06/02/2025 | BEST Inc.BEST Inc., a leader in electronic component rework services, training, and products is pleased to introduce StikNPeel™ rework stencils. This innovative product is designed for printing solder paste for placement of gull wing devices such as quad flat packs (QFPs) or bottom terminated components.
See TopLine’s Next Gen Braided Solder Column Technology at SPACE TECH EXPO 2025
05/28/2025 | TopLineAerospace and Defense applications in demanding environments have a solution now in TopLine’s Braided Solder Columns, which can withstand the rigors of deep space cold and cryogenic environments.