Panasonic Commercializes High Heat Resistance Circuit Board Material for Automotive Use
January 11, 2017 | Panasonic CorporationEstimated reading time: 3 minutes
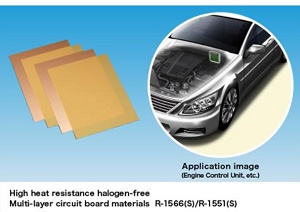
Panasonic Corporation announced today that it has commercialized its High Heat Resistance Halogen-free Multi-layer Circuit Board Material for automotive electronic control unit (ECU) circuit boards. The company will start mass production in April 2017. The product's high heat resistance and excellent tracking resistance[1] will improve the reliability of ECU circuit boards in high-temperature environments.
The number of ECUs mounted per vehicle has been on the rise with advances in the electrification of automobiles. ECUs are often mounted in engine compartments to preserve passenger compartment space, and therefore require resistance to high temperatures. The heat generated by high-performance ECU components themselves also needs to be addressed. Furthermore, circuit board materials need to be increasingly resistant to high temperatures to cope with the larger currents and higher voltages carried by HEV and EV ECU circuits. In the past, improving heat and tracking resistances usually resulted in lower processability of circuit boards due to materials properties. To resolve this issue, Panasonic has commercialized its High Heat Resistance Halogen-free Multi-layer Circuit Board Material, which features high heat and tracking resistances as well as excellent circuit board processability by adopting its unique resin design and compounding technologies based on the quality developed for automotive products.
Panasonic's new multi-layer circuit board material has the following features:
1. Improving the reliability of ECU circuit boards in high-temperature environments by achieving high heat resistance
The glass transition temperature (Tg)[2]: 175°C (DSC(1))
Panasonic's conventional material(2): 148°C
2. Excellent tracking resistance; compatible with large currents and high voltages
Achieved tracking resistance: CTI ≥ 600 V
Panasonic's conventional material*2: 600 V > CTI ≥ 400 V
3. Achieving excellent processability while also improving high heat and tracking resistances
Suitable applications:
Automotive ECUs, automotive modules, HEV/EV power control unit, DC/AC converter substrates
Panasonic Technology
1. Improving the reliability of ECU circuit boards in high-temperature environments by achieving high heat resistance
ECUs mounted in engine compartments, plus the heat generated by high-performance ECU components themselves, have created new requirements for high heat resistance. In some cases, these requirements cannot be met by conventional ECU circuit board materials that have glass transition temperatures of approximately 140 to 150°C. By adopting its unique resin design and compounding technologies, Panasonic has achieved a glass transition temperature of 175°C. This improves the reliability of ECU circuit boards in high-temperature environments and also meets new requirements for high heat resistance such as when these circuit boards are directly mounted on engines.
2. Excellent tracking resistance; compatible with large currents and high voltages
Increases in HEVs and EVs have raised concerns that large currents and high voltages flowing through ECU circuits may increase the risk of tracking, which lead short-circuit and cause failures. There is a growing market demand for circuit boards with high tracking resistance that eliminates short circuits even under high current and voltage conditions. The new product has achieved a CTI (Comparative Tracking Index) of 600 V or higher based on Panasonic's unique resin design and compounding technologies, giving it high insulation resistance to large currents and high voltages, and thus improving the insulation reliability of ECU circuitry.
3. Achieving excellent processability while also providing enhanced heat and tracking resistance
Improved heat and tracking resistances tend to result in hardened circuit board materials, leading to lower drill processability. The new material has achieved excellent processability while also improving high heat and tracking resistances by adopting Panasonic's unique resin compounding technologies. This will contribute to reducing processing costs by extending the service life of drill bits.
Notes:
(1) Differential scanning calorimetry (DSC) based on a circuit board test method (IPC TM650)
(2) Panasonic halogen-free multilayer circuit board material (Product No. R-1566)
About Panasonic
Panasonic Corporation is a worldwide leader in the development of diverse electronics technologies and solutions for customers in the consumer electronics, housing, automotive, enterprise solutions and device industries. Since its founding in 1918, the company has expanded globally and now operates 474 subsidiaries and 94 associated companies worldwide, recording consolidated net sales of 7.553 trillion yen for the year ended March 31, 2016. Committed to pursuing new value through innovation across divisional lines, the company uses its technologies to create a better life and a better world for its customers. To learn more about Panasonic, click here.
Suggested Items
Top Tech in Taiwan: IPC's Blueprint to Advance Smart Manufacturing
06/04/2025 | Sydney Xiao, IPCRenowned as a global hub of innovation and a cornerstone of the electronics industry, Taiwan is leading advancements in technology and manufacturing. A decade ago, IPC established an office in Taiwan, embedding itself deeply in this innovative ecosystem. Now with nearly 200 member companies in the region, IPC remains dedicated to driving standardization, education, and technological progress in Taiwan’s electronics manufacturing sector.
IPC Releases Latest Standards and Revisions Updates
06/05/2025 | IPCEach quarter, IPC releases a list of standards that are new or have been updated. To view a complete list of newly published standards and standards revisions, translations, proposed standards for ballot, final drafts for industry review, working drafts, and project approvals, visit ipc.org/status. These are the latest releases for Q1 2025.
IPC Launches New Wire Harness Design Course Led by Defense Industry Expert
06/03/2025 | I-Connect007 Editorial TeamIPC is expanding its educational offerings with a new online course designed to provide foundational knowledge in wire harness and cable design. The course, Introduction to Wire Harness Design I, is led by a seasoned mechanical engineer and subject matter expert in military cable systems working at FNSS Defense Systems in Turkey.
Nolan’s Notes: Moving Forward With Confidence
06/03/2025 | Nolan Johnson -- Column: Nolan's NotesWe’re currently enjoying a revitalized and dynamic EMS provider market with significant growth potential. Since December 2024, the book-to-bill has been extremely strong and growing. Starting with a ratio of 1.24 in December, book-to-bill has continued to accelerate to a 1.41 in April. Yet, there is a global economic restructuring taking place. To say that the back-and-forth with tariffs and trade deals makes for an uncertain market is an understatement. While we may be in a 90-day tariff pause among leading economic nations, the deadline is quickly approaching and that leaves many of you feeling unsettled about what to expect.
IPC Issues Call for Participation for IPC APEX EXPO 2026
06/02/2025 | IPCIPC is now accepting abstracts for technical papers with presentations, posters, and professional development courses at IPC APEX EXPO 2026.
Copyright © 2025 I-Connect007 | IPC Publishing Group Inc. All rights reserved.
Log in