-
- News
- Books
Featured Books
- smt007 Magazine
Latest Issues
Current IssueSupply Chain Strategies
A successful brand is built on strong customer relationships—anchored by a well-orchestrated supply chain at its core. This month, we look at how managing your supply chain directly influences customer perception.
What's Your Sweet Spot?
Are you in a niche that’s growing or shrinking? Is it time to reassess and refocus? We spotlight companies thriving by redefining or reinforcing their niche. What are their insights?
Moving Forward With Confidence
In this issue, we focus on sales and quoting, workforce training, new IPC leadership in the U.S. and Canada, the effects of tariffs, CFX standards, and much more—all designed to provide perspective as you move through the cloud bank of today's shifting economic market.
- Articles
- Columns
- Links
- Media kit
||| MENU - smt007 Magazine
Achieving Repeatable, Consistent Control over the Selective Soldering Production Process
February 1, 2017 | Gerjan Diepstraten, Vitronics Soltec B.V.Estimated reading time: 5 minutes
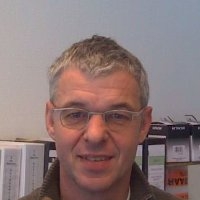
Abstract
Selective soldering is a process with more than 100 different parameters that may impact soldering performance. Some conditions change over time (e.g., machine temperature, humidity, contamination, wear of parts or settings after maintenance). Other factors in the process include the materials used, component wettability, solder mask surface energy, board material Tg and Td values, solder oxidation and composition.
During production, conditions may begin to drift. In order to avoid solder defects, statistical process control or SPC is the best method of identifying unexpected changes in the process. When using this statistical technique, however, it is important that the machine has the tools to measure these essential process parameters and if necessary control them to maintain a robust soldering process. Apart from machine parameters, the materials have a big impact. A robust selective soldering process should have a wide process window that is able to handle variations in material quality. In this paper, critical process parameters are discussed as well as methods that can be used to widen the process window. Additionally, process robustness is evaluated.
Introduction
Selective soldering machines are available in many different configurations, primarily because the assemblies are very different, not only in design, width and mass, but also in volume and in the number of solder joints.
Nevertheless, they all require the same three sub-processes of fluxing, preheating and soldering. These processes can have different methods, but in the end all main parameters are identical to create a solder connection: the amount of flux per area, preheat temperature, solder temperature, and contact time.
Machine and Process Capability
A machine capability analysis may be applied to a selective soldering machine to ascertain its suitability to flux, preheat and solder a circuit assembly. It is a short-term study with the sole aim of discovering the machine-specific effects on the soldering process.
Process capability is more of a long-term study. In addition to variations arising from the machine, all other external factors that influence the soldering process over a longer operating period must be taken into account.
Process capability can only be performed directly on the production line. Parameters tested may include topside board temperature and solder contact time. Parameters that influence the process and are related to the materials that are used include the printed circuit board itself.
Selective soldering is a method often used in the automotive industry. Machine capability is part of the quality program that ISO-certificated companies ascribe to. The ISO auditor may want to see how the company assures the assembly process. Quality tools including process FMEA, machine capability analysis, process capability and statistical process control are part of their daily business.
A machine capability analysis (MCA) is typically done before the acceptance of the machine, when the machine is installed in the production line and/or when the machine is moved to another place in the manufacturing facility to ensure that the performance of the machine is not affected. Some automotive customers require a MCA before a new production line starts up that is dedicated to a specific (new) product/model.
Fluxing Process
The majority of flux application systems in selective soldering are dropjet devices. In the flux process there are some very important parameters that may affect reliability. The most critical is when flux penetrates into a SMD or other area where it is not activated, due to lower process temperatures. Non-activated flux in combination with humidity can cause electro-migration when the product is used in the field. Therefore, the spreading of the flux is the most critical parameter in this process, although it may have no impact on the final soldering result. This is a problem because engineers focus on soldering results and not on flux residues that are very hard to identify. To avoid reliability risk, it is the best to choose a selective soldering flux that is inert even when it isn’t activated[2].
Today many engineers are struggling to control the applied flux amounts. For good soldering, more flux is sometimes needed. Applying more flux creates, however, the potential risk that flux may penetrate into SMD areas.
To avoid this, it is important to understand properties of flux and the printed circuit board.
The solder mask on the PCB is an important component that significantly impacts the spreading of the flux. The flux spread depends on several factors, including the following:
- Flux surface tension (flux type)
- Surface energy of the board (solder mask)
- Temperature of the flux
- Temperature of the board
- Flux amount
As one may notice, none of these are machine parameters expect for the flux amount that can be controlled by adjusting flux machine parameters.
The situation is even more complex. Flux spreading is critical for reliability, but the amount of dry solids of flux per square inch affects soldering quality. Thus, a trend in new fluxes for selective soldering is to increase flux solid content, which allows minor flux (less spreading) and yet retains a high concentration of solids in the soldering area.
A typical soldering process requires 500–2000 μg/in² solids.
Figure 1: Higher surface energy of solder mask makes flux flow.
Figure 1 shows the impact of the flux surface tension and the surface energy of the solder mask on flux spreading. Printed circuit boards made for the wave soldering process may fail in selective soldering due to the higher surface energy of the solder mask that makes the flux spread away from the soldering area.
All of these different parameters affecting the spreading (and thus also the amount of flux per square inch) makes it complicated to effect a process control on this critical process parameter. The surface tension of a flux (influenced by surfactants in flux) isn’t even defined in the datasheet. The surface energy of the solder mask can be measured using simple ink pencils with different inks.
Figure 2: Ink pencils to help define surface energy of a PCB.
The line of ink should remain unchanged for two seconds without turning into droplets; this indicates that the surface energy of the board is the same or higher than the surface tension of the ink. A typical value for selective soldering is 35 mN/m.
This parameter will not change from board to board, but requires verification when a different batch of bare boards are used.
To read this entire article, which appeared in the April 2016 issue of SMT Magazine, click here.
Testimonial
"We’re proud to call I-Connect007 a trusted partner. Their innovative approach and industry insight made our podcast collaboration a success by connecting us with the right audience and delivering real results."
Julia McCaffrey - NCAB GroupSuggested Items
Indium Corporation Promotes Two Leaders in EMEA (Europe, Middle East, and Africa) Markets
08/05/2025 | Indium CorporationWith its commitment to innovation and growth through employee development, Indium Corporation today announced the promotions of Andy Seager to Associate Director, Continental Sales (EMEA), and Karthik Vijay to Senior Technical Manager (EMEA). These advancements reflect their contributions to the company’s continued innovative efforts with customers across Europe, the Middle East, and Africa (EMEA).
MacDermid Alpha Electronics Solutions Unveils Unified Global Website to Deepen Customer, Talent, and Stakeholder Engagement
07/31/2025 | MacDermid Alpha Electronics SolutionsMacDermid Alpha Electronics Solutions, the electronics business of Elements Solutions Inc, today launched macdermidalpha.com - a unified global website built to deepen digital engagement. The launch marks a significant milestone in the business’ ongoing commitment to delivering more meaningful, interactive, and impactful experiences for its customers, talent, and stakeholders worldwide.
KOKI to Showcase Analytical Services and New HF1200 Solder Paste at SMTA Guadalajara 2025
07/31/2025 | KOKIKOKI, a global leader in advanced soldering materials and process optimization services, will exhibit at the SMTA Guadalajara Expo & Tech Forum, taking place September 17 & 18, 2025 at Expo Guadalajara, Salón Jalisco Halls D & E in Guadalajara, Mexico.
Weller Tools Supports Future Talent with Exclusive Donation to SMTA Michigan Student Soldering Competition
07/23/2025 | Weller ToolsWeller Tools, the industry leader in hand soldering solutions, is proud to announce its support of the upcoming SMTA Michigan Expo & Tech Forum by donating a limited-edition 80th Anniversary Black Soldering Set to the event’s student soldering competition.
Koh Young Appoints Tom Hattori as President of Koh Young Japan
07/21/2025 | Koh YoungKoh Young Technology, the global leader in True 3D measurement-based inspection solutions, announced the appointment of Tom Hattori as President of Koh Young Japan (JKY).