-
- News
- Books
Featured Books
- pcb007 Magazine
Latest Issues
Current IssueThe Hole Truth: Via Integrity in an HDI World
From the drilled hole to registration across multiple sequential lamination cycles, to the quality of your copper plating, via reliability in an HDI world is becoming an ever-greater challenge. This month we look at “The Hole Truth,” from creating the “perfect” via to how you can assure via quality and reliability, the first time, every time.
In Pursuit of Perfection: Defect Reduction
For bare PCB board fabrication, defect reduction is a critical aspect of a company's bottom line profitability. In this issue, we examine how imaging, etching, and plating processes can provide information and insight into reducing defects and increasing yields.
Voices of the Industry
We take the pulse of the PCB industry by sharing insights from leading fabricators and suppliers in this month's issue. We've gathered their thoughts on the new U.S. administration, spending, the war in Ukraine, and their most pressing needs. It’s an eye-opening and enlightening look behind the curtain.
- Articles
- Columns
- Links
- Media kit
||| MENU - pcb007 Magazine
Estimated reading time: 1 minute
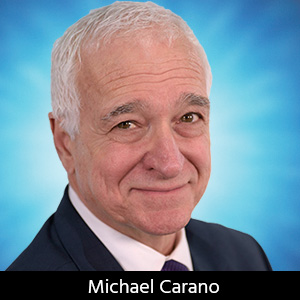
Contact Columnist Form
Trouble in Your Tank: Acid Copper Plating
Introduction
Electroplating a printed circuit board is by no means a trivial task. Higher layer counts, smaller-diameter vias (through-hole and blind) as well as higher-performance material sets contribute to the greater degree of difficulty with today’s technology. So, process engineers pay close attention to the “softer” issues such as cathode current density, solution chemistry (copper sulfate and sulfuric acid concentration) and addition agent control (well, sometime!).
The concern here is that acid copper pattern plating of a printed circuit board has many more critical aspects that must be diligently controlled for optimum performance. These include solution agitation and filtration, anode length and placement, current distribution effects, reducing electrical resistance in the plating cell, photoresist development and controlled organic contamination in the plating solutions. These are the subjects of this article.
Solution Agitation
For uniform surface plating distribution, a homogeneous mixing of the electrolyte is necessary to avoid overplating the surface while the through-hole or blind via is being plated from the bottom up. The engineer should adjust flow rates so as to not create an excessively turbulent solution movement.
Solution agitation of the copper plating electrolyte maybe accomplished with air agitation, eductors, solution impingement and/or cathode bar movement. The main purposes of agitation have been stated many times and include:
- Elimination of solution stagnation and dispersal of reaction products
- Increase of deposition rates by mass transfer enhancement
- Dissipation of heat at electrode/solution interfaces
To read the full version of this article which appeared in the January 2017 issue of the PCB Magazine, click here.
More Columns from Trouble in Your Tank
Trouble in Your Tank: Yield Improvement and ReliabilityTrouble in Your Tank: Causes of Plating Voids, Pre-electroless Copper
Trouble in Your Tank: Organic Addition Agents in Electrolytic Copper Plating
Trouble in Your Tank: Interconnect Defect—The Three Degrees of Separation
Trouble in Your Tank: Things You Can Do for Better Wet Process Control
Trouble in Your Tank: Processes to Support IC Substrates and Advanced Packaging, Part 5
Trouble in Your Tank: Materials for PWB Fabrication—Drillability and Metallization
Trouble in Your Tank: Supporting IC Substrates and Advanced Packaging, Part 5