-
- News
- Books
Featured Books
- smt007 Magazine
Latest Issues
Current IssueIntelligent Test and Inspection
Are you ready to explore the cutting-edge advancements shaping the electronics manufacturing industry? The May 2025 issue of SMT007 Magazine is packed with insights, innovations, and expert perspectives that you won’t want to miss.
Do You Have X-ray Vision?
Has X-ray’s time finally come in electronics manufacturing? Join us in this issue of SMT007 Magazine, where we answer this question and others to bring more efficiency to your bottom line.
IPC APEX EXPO 2025: A Preview
It’s that time again. If you’re going to Anaheim for IPC APEX EXPO 2025, we’ll see you there. In the meantime, consider this issue of SMT007 Magazine to be your golden ticket to planning the show.
- Articles
- Columns
Search Console
- Links
- Media kit
||| MENU - smt007 Magazine
What are the Most Important Principles of Lean Manufacturing?
April 6, 2017 | Neil Sharp, JJS ManufacturingEstimated reading time: 3 minutes
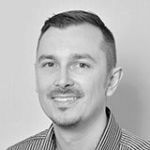
Lean manufacturing is nothing new, but it remains an important philosophy for manufacturers seeking to grow and effectively contend in a competitive, global environment. Essentially, it provides you with the tools to successfully identify and eliminate waste within your operation.
Waste comes in numerous forms, from physical waste (such as components and packaging), to metaphysical waste (such as time and effort expended). In whatever shape it occurs, waste has a detrimental impact on your output, efficiency and bottom line.
Through implementing lean manufacturing, you can focus only on what adds value to your operation, thereby enabling you to reach your business goals. In this post, we will outline the most important principles of lean manufacturing and explore how these can benefit your organization.
Lean Manufacturing and Toyota
Lean manufacturing is generally associated with the Toyota Production System (TPS), which is "steeped in the philosophy of 'the complete elimination of all waste' imbuing all aspects of production in pursuit of the most efficient methods".
TPS is based on two concepts: "The first is called 'jidoka' (which can be loosely translated as 'automation with a human touch'), which means that when a problem occurs, the equipment stops immediately, preventing defective products from being produced. The second is the concept of 'Just-in-Time', in which each process produces only what is needed by the next process in a continuous flow."
By applying these concepts, Toyota has been able to successfully manufacture high-quality vehicles on a consistent basis, and to their customers' requirements. In fact, Toyota is the world's largest car manufacturer – so it's hard to argue with their approach!
What Does Waste Look Like?
Toyota identifies seven different types of waste or "muda" ("futility", "uselessness" or "wastefulness" in Japanese). These were originally coined by Toyota's late chief engineer, Taiichi Ohno, and are (with examples):
- Transport – moving products unnecessarily
- Inventory – unwanted components etc.
- Motion – unnecessary movement of people or equipment
- Waiting – superfluous downtime
- Overproduction – manufacturing more product than is required
- Over processing – using complex tools where simpler ones would be sufficient
- Defects – spending time resolving preventable issues
By focusing your attention on each of these areas - all of which are non-value adding - and working out where improvements can be made, you can gradually decrease the amount of waste generated by your organisation. There are a number of tools that enable this – for example, Six Sigma, which focuses on reducing errors, and 5S, which is concerned with "continuous improvement".
The Role of Culture in Lean Manufacturing
While lean manufacturing derives from TPS, the term "lean" was actually coined by John Krafcik in his 1988 article, "Triumph of the Lean Production System", which remains relevant today.
Writing on his blog, "lean healthcare" consultant Mark Graban says, “I recommend [Krafcik's article] to lean practitioners and leaders today, not just as a historical artefact, but because its key points are still valid and relevant. What makes a ‘lean production system?’ It’s not the tools; it’s the management style and the culture. That was true in 1988 and it’s true today.
“[Krafcik] didn’t write about tools like 5S, kanban systems, or heijunka boxes. He wrote primarily about management, leadership, and culture.”
This is an incredibly important point to make. There is a host of resources out there, to help you become a “lean” organization – but, with the best will in the world, you won't succeed in your endeavor without engaging with this philosophy on a human level; without making sure that your entire team is on board and understands the importance of what you're doing.
That's why it's helpful to understand lean manufacturing as a philosophy – it’s a holistic way of thinking and working that should inform every element of your manufacturing process. It's crucial to adopt the right mindset before rolling out the practical changes required.
At its most basic level, lean manufacturing reduces waste within your manufacturing operation. As a consequence, you can increase your productivity, better serve the needs of your customers and grow your organization, ready to compete in today’s fast-changing and exciting environment.
This article originally appeared on the JJS Manufacturing blog, which can be found here.
Suggested Items
KYZEN’s Adam Klett to Present at 2025 SMTA Electronics in Harsh Environments Conference
05/05/2025 | KYZEN'KYZEN, the global leader in innovative environmentally responsible cleaning chemistries, announced today that Director of Science Adam Klett, PhD will present during the technical conference at the 2025 SMTA Electronics in Harsh Environments Conference.
Punching Out: Your Financial Preparation for a Sale
05/07/2025 | Tom Kastner -- Column: Punching Out!When preparing for a sale, it’s important to clean up the financials as much as possible. The fewer questions and the less that needs to be explained, the easier it is to get through due diligence without slowing things down or creating mistrust. Here are the main things that are relatively easy to clean up.
KYZEN to Spotlight Stencil Cleaning Solutions at SMTA Oregon
05/02/2025 | KYZEN'KYZEN, the global leader in innovative environmentally friendly cleaning chemistries, will exhibit at the SMTA Oregon Expo & Tech Forum, scheduled to take place on Tuesday, May 20 at the Wingspan Event and Conference Center in Hillsboro, OR. KYZEN’s cleaning expert Jeff Deering will be on-site at the expo providing information about stencil cleaning chemistries, including KYZEN E5631J.
KYZEN to Feature Stencil Cleaning and Aqueous Cleaners at SMTA Capital Expo and Tech Form
04/28/2025 | KYZEN'KYZEN, the global leader in innovative environmentally responsible cleaning chemistries, will exhibit at the SMTA Capital Expo and Tech Forum, scheduled to take place Thursday, May 8 at George Mason University – Mason Square in Arlington, VA.
KYZEN Focuses on Aqueous Cleaning and Stencil Cleaning at SMTA Wisconsin
04/24/2025 | KYZEN'KYZEN, the global leader in innovative environmentally responsible cleaning chemistries, will exhibit at the SMTA Wisconsin Expo and Tech Forum, scheduled to take place Tuesday, May 6 at the Crowne Plaza Milwaukee Airport. KYZEN will be on-site to provide attendees with information about aqueous cleaning chemistry AQUANOX A4618 and stencil cleaner KYZEN E5631J.