-
- News
- Books
Featured Books
- smt007 Magazine
Latest Issues
Current IssueIntelligent Test and Inspection
Are you ready to explore the cutting-edge advancements shaping the electronics manufacturing industry? The May 2025 issue of SMT007 Magazine is packed with insights, innovations, and expert perspectives that you won’t want to miss.
Do You Have X-ray Vision?
Has X-ray’s time finally come in electronics manufacturing? Join us in this issue of SMT007 Magazine, where we answer this question and others to bring more efficiency to your bottom line.
IPC APEX EXPO 2025: A Preview
It’s that time again. If you’re going to Anaheim for IPC APEX EXPO 2025, we’ll see you there. In the meantime, consider this issue of SMT007 Magazine to be your golden ticket to planning the show.
- Articles
- Columns
Search Console
- Links
- Media kit
||| MENU - smt007 Magazine
Navigating the Complex World of Flex Circuit Assembly
April 7, 2017 | Stephen Las Marias, I-Connect007Estimated reading time: 2 minutes
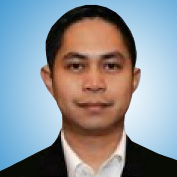
The expanding use of flexible printed circuits in markets such as military/aerospace electronics, automotive electronics, and medical electronics is fueling the demand growth for this PCB technology.
According to a report by Global Industry Analysts Inc. (GIA), the global market for flexible printed circuits is projected to reach $15.2 billion by 2020, driven by the growing focus of electronics manufacturers on performance and design flexibility.
Allied Market Research (AMR), another industry analysis group, is likewise bullish. It projects the worldwide flex printed circuit market to reach $27 billion by 2022, with a compound annual growth rate (CAGR) of 10.4% from 2016 to 2022.
From a regional perspective, Asia-Pacific—which is considered the global hub for electronics production—ranks as the fastest growing market for flex printed circuits, registering a CAGR of 6.7% over the 2013–2020 forecast period, according to GIA.
AMR, on the other hand, notes that Asia-Pacific dominated the global flex printed circuit market in terms of revenue, accounting for more than 46% in 2015, followed by North America.
We at I-Connect007 recently conducted a survey on flexible printed circuits to know more about the challenges that designers, fabricators, and assemblers face when dealing with flex circuits. They were asked about the steps in their processes that have the biggest effect on yields; the challenge when dealing with flex circuit materials; as well as the factors that have the greatest impact on the quality of their flex circuit design, fabrication and assembly.
Another question focused on market demands that are driving the increasing use of flexible printed circuits. Majority of the respondents highlighted the trend toward smaller form factors, which is leading to space-constrained designs. From a market applications perspective, the aerospace and defense segment, consumer electronics, and medical electronics were found to be the key industry sectors seeing increased use of flexible circuits, as per our survey.
Also, most respondents consider the design of the flex circuit, the handling, and soldering processes as among the key factors that have the biggest effect on yields.
Another issue is moisture control. In a short email interview, Brian Tracey, group vice president of business development at Interplex Industries Inc.—a provider of design and manufacturing services for custom flex circuit assembly—says the hydroscopic nature of the flex circuit makes it difficult to process, therefore drying the flex circuits prior to soldering can help improve yields. Directly related to this is the soldering process, which he considers as a key process step that has the biggest effect on yield as it can sometimes create solder voids, cold solder joints or incomplete circuits.
Meanwhile, Tracey notes that the limitations with the adhesives used between the insulation and copper layers offer a major challenge in flex circuit assembly as these adhesives are sensitive to water absorption as well as heat, which can break down the adhesive layers and cause the traces to fracture.
To read this entire article, which appeared in the March 2017 issue of SMT Magazine, click here.
Suggested Items
Indium’s Karthik Vijay to Present on Dual Alloy Solder Paste Systems at SMTA’s Electronics in Harsh Environments Conference
05/06/2025 | Indium CorporationIndium Corporation Technical Manager, Europe, Africa, and the Middle East Karthik Vijay will deliver a technical presentation on dual alloy solder paste systems at SMTA’s Electronics in Harsh Environments Conference, May 20-22 in Amsterdam, Netherlands.
SolderKing Achieves the Prestigious King’s Award for Enterprise in International Trade
05/06/2025 | SolderKingSolderKing Assembly Materials Ltd, a leading British manufacturer of high-performance soldering materials and consumables, has been honoured with a King’s Award for Enterprise, one of the UK’s most respected business honours.
Knocking Down the Bone Pile: Gold Mitigation for Class 2 Electronics
05/07/2025 | Nash Bell -- Column: Knocking Down the Bone PileIn electronic assemblies, the integrity of connections between components is paramount for ensuring reliability and performance. Gold embrittlement and dissolution are two critical phenomena that can compromise this integrity. Gold embrittlement occurs when gold diffuses into solder joints or alloys, resulting in mechanical brittleness and an increased susceptibility to cracking. Conversely, gold dissolution involves the melting away of gold into solder or metal matrices, potentially altering the electrical and mechanical properties of the joint.
'Chill Out' with TopLine’s President Martin Hart to Discuss Cold Electronics at SPWG 2025
05/02/2025 | TopLineBraided Solder Columns can withstand the rigors of deep space cold and cryogenic environments, and represent a robust new solution to challenges facing next generation large packages in electronics assembly.
BEST Inc. Reports Record Demand for EZReball BGA Reballing Process
05/01/2025 | BEST Inc.BEST Inc., a leader in electronic component services, is pleased to announce they are experiencing record demand for their EZReball™ BGA reballing process which greatly simplifies the reballing of ball grid array (BGA) and chip scale package (CSP) devices.