-
- News
- Books
Featured Books
- smt007 Magazine
Latest Issues
Current IssueSupply Chain Strategies
A successful brand is built on strong customer relationships—anchored by a well-orchestrated supply chain at its core. This month, we look at how managing your supply chain directly influences customer perception.
What's Your Sweet Spot?
Are you in a niche that’s growing or shrinking? Is it time to reassess and refocus? We spotlight companies thriving by redefining or reinforcing their niche. What are their insights?
Moving Forward With Confidence
In this issue, we focus on sales and quoting, workforce training, new IPC leadership in the U.S. and Canada, the effects of tariffs, CFX standards, and much more—all designed to provide perspective as you move through the cloud bank of today's shifting economic market.
- Articles
- Columns
- Links
- Media kit
||| MENU - smt007 Magazine
Rework and Repair on Flex Circuits
April 14, 2017 | Bob Wettermann, BEST Inc.Estimated reading time: 4 minutes
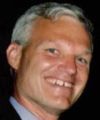
Flex circuits are used in a variety of applications for the interconnection of conductors which need to be bent or exercised continuously. This interconnection technology has historically been used as a wire interconnection. There are a variety of versions of this type of circuit. One of them is the dual access flex circuit which is a single-sided flex circuit that is manufactured so that the conductive material can be accessed from both sides of the flex. A double-sided flex circuit is a circuit having two conductive layers, one on each side of the base layer within the circuit. Trace patterns, specific to your needs, can be created on both sides of the substrate film. They can be interconnected where desired with copper plated through-holes. A multilayer flex circuit combines several single-sided or double-sided circuits with complex interconnections, shielding and/or surface mounted technologies in a multilayer design. Rigid flex circuits combine the best of both rigid printed circuit boards and flexible circuits integrated. Circuits are typically interconnected between the rigid and flex circuits through plated through-holes.
There are a variety of benefits to the flex circuits. One of the major benefits of a flex assembly is the nearly error-free implementation of wiring in lieu of labor intensive hand wiring. They are also able to configured, unlike their rigid counterparts, as complex 3-dimensional configurations as they can be contorted in to a variety of shapes. As the name implies, the materials used in flex circuits can be bent back and forth numerous times meaning they can be used in in highly repetitive applications such as on print heads. When weight is an issue, flex circuits are a good alternative to rigid boards and wires as both the dielectric material and conductor runs are very thin.
Over the last several years the flex industry has seen a growth in demand. It is now a 10 billion WWD industry with growth rates in the 7–10% year range.
Figure 1: Rigid-flex circuit board assembly.
With this surge in usage of flex, the standards for rework (replacing devices while still meeting the initial specification and functionality) and repair (repairing the physical damage on a flex circuit) of these type of electronic interconnection circuits has not kept pace.
There are some rework challenges that come from the very nature of flex circuits. First of all, it is difficult to hold the flex circuit flat. The flexible nature of the Kapton or other base flex material, which makes it so attractive in the application, makes it challenging from a rework perspective. In order to retain the flatness of the assembly, it needs to be taped to be held down. In some cases, a vacuum fixture, a relatively pricey endeavor, is fabricated for flex circuit rework. When placing fine pitch components, the vacuum structure of such fixtures has a significant influence. If the vacuum is directly under some of the leads of a fine pitch component, there is a likelihood any vacuum will “pull” the flex into the hole, preventing the component from contacting the flex circuit lead, thereby resulting in an electrical “open.” For rework paste printing, co-planarity is a challenge when the stencil and surface to be printed are not coplanar. Therefore, paste print deposition using a syringe is often used instead. Sometimes, conductive epoxies are used in interconnecting devices to the flex material. While the curing temperature of these joining materials is much lower than the reflow temperature of more standard solder, it can make a mess. Even when the rework process is engineered properly, many times the limitation on rework is that the marginal cost of the assembly is far less than the burdened rework cost, making the scrap pile a more attractive economic alternative.
Figure 2: Rigid flex ripped circuit.
There are some advantages to reworking flex circuits from a process standpoint. The lower thermal mass compared to a rigid PCB shortens the duration time to reach liquidus when soldering to a flex board. This speeds up the rework process for replacement. In addition, many times this lowers the air temperature required from the hot air system thereby resulting in less potential component damage. The high temperature withstand properties of flex materials such as Kapton, Peek and high-temperature polyimide all give the flex rework process a larger process window.
In terms of industry standards for PCB repair, the IPC 7711/21 Repair and Modification of Printed Boards and Electronic Assemblies covers the rework and repair processes for flex circuits. Each of the processes in the standard are listed in terms of their applicability to flex rework or repair with an “F” in the upper right-hand part of the process documents under the “Board Type” section heading. There is even a flex-specific standard of conductor repair. Conductor repairs on flex is covered in procedure 7.1.1.
Figure 3: Repaired base Kapton material along with conductors.
By way of an example of a conductor repair, Figure 2 illustrates a torn flex circuit as part of a rigid-flex board. The standard process found in IPC 7721 3.5.1 was used to repair the material. The conductor runs had a copper foil jumper installed to replace the damaged conductors and then they were soldered together for further rigidity. The outcome of this repair can be found in Figure 3.
Rework and repair of flex circuit assemblies is evolving and remains a challenge as the industry continues to adopt best practices from the rigid assembly world.
This article was originally published in the March 2017 issue of SMT Magazine.
Testimonial
"The I-Connect007 team is outstanding—kind, responsive, and a true marketing partner. Their design team created fresh, eye-catching ads, and their editorial support polished our content to let our brand shine. Thank you all! "
Sweeney Ng - CEE PCBSuggested Items
MacDermid Alpha Electronics Solutions Unveils Unified Global Website to Deepen Customer, Talent, and Stakeholder Engagement
07/31/2025 | MacDermid Alpha Electronics SolutionsMacDermid Alpha Electronics Solutions, the electronics business of Elements Solutions Inc, today launched macdermidalpha.com - a unified global website built to deepen digital engagement. The launch marks a significant milestone in the business’ ongoing commitment to delivering more meaningful, interactive, and impactful experiences for its customers, talent, and stakeholders worldwide.
KOKI to Showcase Analytical Services and New HF1200 Solder Paste at SMTA Guadalajara 2025
07/31/2025 | KOKIKOKI, a global leader in advanced soldering materials and process optimization services, will exhibit at the SMTA Guadalajara Expo & Tech Forum, taking place September 17 & 18, 2025 at Expo Guadalajara, Salón Jalisco Halls D & E in Guadalajara, Mexico.
Weller Tools Supports Future Talent with Exclusive Donation to SMTA Michigan Student Soldering Competition
07/23/2025 | Weller ToolsWeller Tools, the industry leader in hand soldering solutions, is proud to announce its support of the upcoming SMTA Michigan Expo & Tech Forum by donating a limited-edition 80th Anniversary Black Soldering Set to the event’s student soldering competition.
Koh Young Appoints Tom Hattori as President of Koh Young Japan
07/21/2025 | Koh YoungKoh Young Technology, the global leader in True 3D measurement-based inspection solutions, announced the appointment of Tom Hattori as President of Koh Young Japan (JKY).
Silicon Mountain Contract Services Enhances SMT Capabilities with New HELLER Reflow Oven
07/17/2025 | Silicon Mountain Contract ServicesSilicon Mountain Contract Services, a leading provider of custom electronics manufacturing solutions, is proud to announce a significant upgrade to its SMT production capability with the addition of a HELLER 2043 MK5 10‑zone reflow oven to its Nampa facility.