-
- News
- Books
Featured Books
- smt007 Magazine
Latest Issues
Current IssueWhat's Your Sweet Spot?
Are you in a niche that’s growing or shrinking? Is it time to reassess and refocus? We spotlight companies thriving by redefining or reinforcing their niche. What are their insights?
Moving Forward With Confidence
In this issue, we focus on sales and quoting, workforce training, new IPC leadership in the U.S. and Canada, the effects of tariffs, CFX standards, and much more—all designed to provide perspective as you move through the cloud bank of today's shifting economic market.
Intelligent Test and Inspection
Are you ready to explore the cutting-edge advancements shaping the electronics manufacturing industry? The May 2025 issue of SMT007 Magazine is packed with insights, innovations, and expert perspectives that you won’t want to miss.
- Articles
- Columns
- Links
- Media kit
||| MENU - smt007 Magazine
Mentor Graphics: Connecting the Manufacturing Environment
May 18, 2017 | Stephen Las Marias, I-Connect007Estimated reading time: 6 minutes
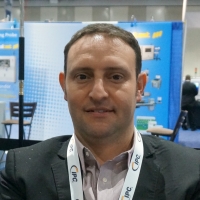
Oren Manor serves as the director of business development for Mentor Graphics Valor Division. His responsibilities include business ownership of Valor’s engineering and pre-production tools as well as partnerships and OEM engagements. In this interview with SMT Magazine, Manor discusses the latest updates in their Open Manufacturing Language (OML) community, their case study regarding Phoenix Contact’s implementation of their IoT solution in its facilities, and what’s new in ODB++.
Stephen Las Marias: Oren, please tell us briefly about Mentor Graphics and your role in the company.
Oren Manor: Mentor Graphics is a rather large company, doing everything from IC design to PCB layout, and cabling system design into manufacturing, which is the Valor division. I'm responsible for all our partnerships in the Valor Division, managing business development with our OEM partners, the machine vendors, and all other partnerships, whether it's for programming or for data connectivity.
I've been involved with OML because it requires cooperation from the machine vendors. I've been involved heavily in trying to evangelize and convince some of the machine vendors here that OML is the future and for the last 18 months, I’ve been promoting OML as a standard for the industry.
Las Marias: What challenges are you seeing at IPC APEX EXPO?
Manor: Getting the data is a challenge. Everybody has it. There are a lot of proprietary interfaces here. If you walk through this floor, you will see hundreds of different proprietary interfaces where the protocols are different—one machine communicates to you via TCP/IP, one communicates over some kind of file-based protocol, or one has a database—and the data is different. I count in seconds, you count in minutes; I don't give you this data, you give that the data—it's a mess.
Then OML tries to consolidate the data to say, "Here are the events coming from a machine." This is all the data that the machine needs to provide and there’s an SDK that explains how to do the communication over the network, which is reliable, secure, and efficient. OML makes some sense out of this mess of proprietary interfaces to promote a single language.
OML will greatly benefit all our competitors, so it will benefit every company out there that has some kind of traceability or MES solution—whether it is Aegis, iTac, Cogiscan, even SAP and the ERP vendors. They will all benefit since the ERP system cannot really access real-time data from the shop floor because it's all proprietary, and SAP doesn’t develop drivers for all of these machines. OML acquires the data in real-time and is applied to real-world manufacturing shop-floor processes – it’s straightforward.
We’ve been getting a lot of traction with OML. We have more than 400 people in our OML community now and we have about 50 development partners. We see a lot of good momentum. I'm not sure that the industry can generate its own standard. This industry is known for de facto standards, and a good example is ODB++, which is a de facto standard. It's the best way to send data from design to manufacturing. The copyright is owned by Mentor, but the ODB++ specification is completely free. Anybody can get it and anybody can develop an ODB++ reader. That’s why most of the machines here know how to read ODB++ data. Just because the OML is pioneered and driven by Mentor, it doesn’t mean it cannot be absorbed by the industry.
Las Marias: OML is open for everyone.
Manor: Open for everybody. Anybody can go to the OML community website and get the OML specification. All we’re retaining is the copyright ownership, so we have the right to make changes, but anybody can use it free of charge, royalty-free, no licensing, and they don't need to use any Mentor tool. In many cases, users have a flow that is completely comprised of non-Mentor applications. You don’t need to use any Mentor tool or Mentor software with it; you can use it in any kind of environment and I think that's why the big EMS companies like OML so much. It allows them to get the data and use it in their home-grown systems. Because they’ve developed a lot of applications over the years, you can't just strip them away now. OML allows them to use the data with their existing MES applications developed in-house and grown over the years.
Las Marias: How has the OML community grown over this past year?
Manor: Tremendously. We only started it about a year ago. It’s grown rapidly. We get very good, positive reactions from both the machine vendors as well as EMS vendors. Also now, with the fact that the CFX (Connected Factory Exchange), the standard developed by IPC, is in limbo at the moment, I think it’s hard to get consensus from the machine vendors, the EMS, and the OEMs about how to do this. Everybody has their own approach. It’s going to be challenging for IPC to get everybody here to agree.
Now, of course, we fully support and are part of IPC, but I’m not sure it’s straightforward to promote the CFX as an industry consortium. It might be better if we just try to promote the OML as a given. OML is already on the table and available to everyone. You can adopt it now rather than wait three years for all these guys to agree on something—who knows if the end compromise is worthwhile?
We’re engaged, we’re working with some leading companies to enhance where we have limitations or where we need some additional information. We’re getting good traction and good feedback from a lot of industry players.
Las Marias: The Industry 4.0 and IoT are among the major discussions last year. Do you think everyone really knows what that is about?
Manor: Probably not. At the end of the day, a lot of people want to buy an Industry 4.0 application or smart factory solution. It’s challenging for companies to understand what to really do from a practical perspective and how to make it efficient. On the other hand, smart manufacturing does have some concepts and talks about Lean solutions; it talks about having very good data, and making real-time decisions.
The Industry 4.0 discussion provides two topics which are good to talk about: data and connectivity. How do I get data? How do I really read and collect real-time information? And the whole idea about big data analytics…once you collect the data, you have a significant amount of data—even if you’re a small, two-, three-line EMS. If you collect all of the traceability and quality data from all of your machines, you need a big data solution. A traditional SQL database is not going to be able to hold that data, so you immediately fall into this big data segment and you need a solution for big data.
You will now understand that you need to solve your data collection problem. You need real-time data, but you can’t trust the data fed by operators or collected manually. If you really want to know what’s happening on the shop floor, you need to collect the data from the machine and you need a solution for the data captured if you want to do some analytics. People now are looking for these two applications because they understand that this is going to get them into this smart manufacturing domain.
To read the full version of this article which appeared in the May 2017 issue of SMT Magazine, click here.
Suggested Items
Delta SEA Partner Event 2025 Unites Regional Partners to Embrace a “Future Ready” Vision
07/03/2025 | Delta ElectronicsDelta Electronics (Thailand) Public Company Limited, successfully hosted its Delta SEA Partner Event 2025: Future Ready at Delta Chungli Plant 5, Taiwan on June 10 – 11 , 2025.
Murray Percival Company Welcomes CeTaQ to Its Line Card, Optimizing SMT Processes for PCB Manufacturers
07/03/2025 | Murray Percival CompanyThe Murray Percival Company, a trusted supplier to the Midwest's electronics industry, is pleased to announce that it has added CeTaQ to its line card, a global expert in Surface Mount Technology (SMT) measurement systems.
RBB’s Jeff Schartiger Appointed to SMTA Ohio Board as Technical Advisor
07/03/2025 | RBBRBB, a trusted leader in electronics manufacturing since 1973, is proud to announce that Jeff Schartiger, Operations Manager at RBB, has been appointed to the SMTA Ohio Chapter Board as a Technical Advisor.
Kitron Receives EUR 4 Million Contract for Defense Airborne Radar Application
07/02/2025 | KitronKitron has received an order valued at EUR 4 million to produce electronics modules for airborne radar application, destined for the US market.
Zollner Completes Full Acquisition of Bluechips Microhouse
07/01/2025 | Zollner Elektronik AGZollner Elektronik AG has successfully finalized its complete takeover of Bluechips Microhouse Co., Ltd., in Thailand. In the future the company will operate as part of the Zollner Group of companies under the leadership of Thomas Kiefl—strategically networked, technologically focused and internationally oriented.