-
- News
- Books
Featured Books
- smt007 Magazine
Latest Issues
Current IssueWhat's Your Sweet Spot?
Are you in a niche that’s growing or shrinking? Is it time to reassess and refocus? We spotlight companies thriving by redefining or reinforcing their niche. What are their insights?
Moving Forward With Confidence
In this issue, we focus on sales and quoting, workforce training, new IPC leadership in the U.S. and Canada, the effects of tariffs, CFX standards, and much more—all designed to provide perspective as you move through the cloud bank of today's shifting economic market.
Intelligent Test and Inspection
Are you ready to explore the cutting-edge advancements shaping the electronics manufacturing industry? The May 2025 issue of SMT007 Magazine is packed with insights, innovations, and expert perspectives that you won’t want to miss.
- Articles
- Columns
- Links
- Media kit
||| MENU - smt007 Magazine
The Benefits of Postponement Manufacturing When Outsourcing
May 25, 2017 | Neil Sharp, JJS ManufacturingEstimated reading time: 5 minutes
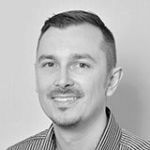
Accurately trying to predict the configuration options your customer will order over a 12-month period is tough. In fact, some sales staff will tell you it's impossible.
Despite having historical sales data and the latest market intelligence, it's a process many original equipment manufacturers (OEMs) struggle with each year. Too much stock of the wrong variant at the wrong time – sound familiar?
As customer service expectations for consumer products increase when it comes to delivery and personalization, so do those for complex industrial electronic products and systems. With the world changing at an incredible pace, OEMs agile enough to respond rapidly to customer demand stand a greater chance of survival compared to those that are not.
Let's take a look in more detail at this late stage configuration technique and some of the benefits an OEM can expect to gain when outsourcing to an electronics manufacturing services (EMS) provider that offers this service.
What is postponement manufacturing?
In simple terms, the EMS provider builds a generic version of the product (often referred to as an "embryo" unit) and then places it into stock. On receipt of a firm order from the customer, the embryo is then taken out of stock, configured, tested, packaged and shipped to the customer.
Dell have long been seen as early adopters of this strategy and arguably transformed the PC market we know today from a "make-to-stock" to a "make-to-order" model. Writing for IndustryWeek, Dave Blanchard comments, "Back in the 1990s, computer maker Dell Inc. became the poster child for supply chain efficiency largely thanks to its 'direct model', which shifted a make-to-stock philosophy to make-to-order. That transition helped Dell reduce its cycle times to levels that had been unthinkable for the high-tech industry, allowing the company to carry inventory for just a few days rather than for three to four weeks. And other industries, particularly the consumer-packaged-goods field, were quick to notice Dell's success and began shifting their own supply chains toward the direct model."
While postponement manufacturing is a relatively simple theory, in practice it involves a high degree of collaboration between the OEM and EMS provider and visibility throughout the supply chain.
For instance, in order to produce enough embryo units to meet demand, the EMS provider needs:
- An indication of the total number of finished products or systems required per annum, along with typical monthly run rates.
- A robust supporting supply chain.
Ideally, these details would be captured within a service level agreement (SLA) so that both parties are clear in terms of delivery expectations and stock liabilities. While the OEM cannot be expected to predict the exact variations their customers will order, they should be able to estimate the total number of units they plan to sell during the year. Armed with this information (plus typical monthly run rates), the EMS provider can begin looking at what stock levels they would need to pipeline in order to meet potential demand.
Regular business reviews between the OEM and the EMS provider are critical when it comes to postponement manufacturing. The meetings allow finished goods levels and stock liabilities to be discussed, while providing the OEM with an opportunity to update the EMS provider with any updated forecasting information they may have.
In addition, they are a particularly useful forum when discussing new products added to the range or when the OEM is planning to withdraw an older version from the market. Both scenarios are likely to require the EMS provider to make changes to the existing supply chain, to ensure the OEM has stock in place for the new version and is not left with excess raw materials associated with the legacy product. Postponement manufacturing is an investment, for both parties, and in order to be successful it requires a close, collaborative, long-term partnership.
The benefits of postponement manufacturing for OEMs
So now we have covered some of the basics, what are the advantages to an OEM in working with their EMS provider and implementing a postponement manufacturing strategy?
- Reduction in inventory - one of the key benefits that you can realise through postponement manufacturing is a reduction in finished goods stock. Finished units would be configured, tested, packaged and shipped out only when firm demand has been confirmed - i.e. an order has been placed. This means any "just in case" stock that has built up over the years trying to second guess what customers might order should finally be a thing of the past.
- Reduction in lead-time to the end user - it could easily take several months to build, test, package and ship your complex industrial electronics device from scratch. However, adopting a postponement manufacturing strategy can significantly reduce this time as the build is effectively split out into two stages. The embryos are scheduled and built in advance by the EMS provider, which takes the majority of time, leaving the lead-time associated with final configuration, packaging and shipment left to complete when an order is placed - which, in many cases, can take just a few days.
- Ability to react quicker to customer demand - linked to the above, with delivery lead-times slashed to a handful of days, your sales team have the ability to react and fulfil fluctuations in customer demand much more effectively. And more importantly, before the competition get a chance.
- Ability to build in greater levels of customization - what do your customers really want? What elements of the hardware, software, packaging or accessories could be personalized on the products you design and sell? What are your competitors offering? How will the market change in the next three to five years? Although you may not have answers to all of these questions right now, they are worth bearing in mind as mass customization continues to shape the manufacturing industry.
So, if you currently design and sell a highly configurable or personalized product, with fluctuating demands (at an "option" or "variant" level), a postponement manufacturing strategy could be the answer you are looking for. And I guess if you don't currently offer your customers any degree of product personalization, should you?
This strategy doesn't tend to work well for OEMs that only plan to outsource small parts of their product or supply chain, or those looking for the cheapest supplier with a tendency to change each year. However, for those that have researched the benefits of a complete outsourced manufacturing solution, and are now actively looking to focus on the core activities that really matter to their business (design, sales, marketing, customer service,) it can totally transform their business.
This article originally appeared on the JJS Manufacturing blog, which can be found here.
Suggested Items
Delta SEA Partner Event 2025 Unites Regional Partners to Embrace a “Future Ready” Vision
07/03/2025 | Delta ElectronicsDelta Electronics (Thailand) Public Company Limited, successfully hosted its Delta SEA Partner Event 2025: Future Ready at Delta Chungli Plant 5, Taiwan on June 10 – 11 , 2025.
Murray Percival Company Welcomes CeTaQ to Its Line Card, Optimizing SMT Processes for PCB Manufacturers
07/03/2025 | Murray Percival CompanyThe Murray Percival Company, a trusted supplier to the Midwest's electronics industry, is pleased to announce that it has added CeTaQ to its line card, a global expert in Surface Mount Technology (SMT) measurement systems.
RBB’s Jeff Schartiger Appointed to SMTA Ohio Board as Technical Advisor
07/03/2025 | RBBRBB, a trusted leader in electronics manufacturing since 1973, is proud to announce that Jeff Schartiger, Operations Manager at RBB, has been appointed to the SMTA Ohio Chapter Board as a Technical Advisor.
Kitron Receives EUR 4 Million Contract for Defense Airborne Radar Application
07/02/2025 | KitronKitron has received an order valued at EUR 4 million to produce electronics modules for airborne radar application, destined for the US market.
Zollner Completes Full Acquisition of Bluechips Microhouse
07/01/2025 | Zollner Elektronik AGZollner Elektronik AG has successfully finalized its complete takeover of Bluechips Microhouse Co., Ltd., in Thailand. In the future the company will operate as part of the Zollner Group of companies under the leadership of Thomas Kiefl—strategically networked, technologically focused and internationally oriented.