Victory Giant Technology: The Qualified Forerunner of PCB Smart Factories
August 2, 2017 | Tulip Gu, I-Connect007Estimated reading time: 7 minutes
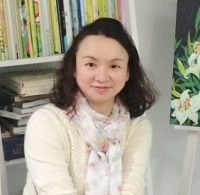
The topic of the July issue of PCB007’s China Online Magazine is “Automatic PCB Factories,” focusing on the pressures of cost, delivery time and process, and the irreversible trend toward automated PCB factories. Centering on this theme, we interviewed Andy Zhou, COO of Victory Giant Technology (HuiZhou) Co. Ltd., the first domestic PCB manufacturer who carries out large-scale implementation of intellectualization throughout the factory. As there are various opinions about how to build a smart PCB factory, we invited him to give us some ideas.
For quite a long time, Victory Giant Technology (HuiZhou) Co., Ltd. acted as the world’s largest PCB provider of high-density multilayer VGA (video card). The company’s layout also covers high value-added application areas like new energy automobile circuit board, server, industrial control, etc.
Benefiting from the smart manufacturing shop, which came into use in 2015, and gradually reaching target output, it brought huge growth in capacity and saved more labour cost. Most obvious, the price increase of copper-clad laminate and copper foils started from last year, instead, completely reflected the advantage of the supply chain.
Figure 1: Automated horizontal plating line at Victory Giant Technology.
Tulip Gu: As a forerunner of PCB smart factories, what kind of actions on the smart factory project is Victory Giant Technology taking, and what are the results?
Andy Zhou: Globalization is putting more and more pressure on market competition, and the life cycle of electronic products is becoming shorter and shorter. The market is requiring more and more from the PCB manufacturers. To conform to the times, Victory Giant Technology now has invested 1.12 billion yuan to build a smart factory based on Industry 4.0, thus we can fully realize “Production automation, unmanned logistics, intelligent scheduling, and digital management.” By making comprehensive innovation and intelligent reconstruction in the production process, we need only 350 people to fulfill 10 billion output value, and we have shortened the delivery time from 57 days to only 36 hours.
Gu: Do you agree that high-starting-point automation leads to high-production benefits? As we know, talking about “using machinery to replace people,” Victory Giant Technology is the leading player in the industry. You have mentioned that you need just 350 people to fulfill 10 billion output value, so do you think per-capita output value is good criteria to measure the success of automation? Or do you think there are other factors which are more important? (e.g., the perfect combination of people, machinery, information exchange is the very essence of automation.)
Figure 2: The LDI room at Victory Giant.
Zhou: High-starting-point automation does not always lead to high production benefit. High production benefit comes from system engineering. We started from the whole planning of IE, and used automation and informatization to achieve overall lowest cost, highest productivity and best quality. Per-capita output value is one of the key criteria to measure the success of automation, yet we regard return on investment as the most important one. If investing in automation could bring “lower cost, shorter delivery time, and better quality,” that means the project has succeeded.
Gu: Some experts think that the overall level of automation in China lags, but we should not improperly belittle ourselves, for we have the best manufacturing ecosystem in the world. What is your opinion? Along the way Victory Giant Technology pushing smart factory forward, what kind of problem you have encountered and how do you solve them? Could you please give us some real cases?
Zhou: China does have the best manufacturing ecosystem in the world. In the construction of the whole Victory Giant Technology smart factory, we can find 80% of equipment vendors that we need for our project within Pearl River Delta, a two-hour economic circle. And they are very willing to innovate and upgrade the equipment together with us. This is the important foundation which can ensure the success of our project. Along the way as we were pushing smart factory forward, the biggest problem we met is the standardization. In the past, when we talked about automation, we only focused on partial automation, but now we focus on whole automation. If we cannot realize the standardization of loading before and after the procedure, we cannot realize the logistics of automation. If we cannot realize the standardization of communication protocol between equipment from different vendors, we cannot realize perfect informatization. So standardization is always the stumbling block on the way of pushing smart factory forward. Based on “Collaborative Innovation,” we discuss with our vendors and we together work on standards. For example, we have solved the problem of feeding and unloading vehicles during different procedures, and we have also solved the problem of communication protocol between equipment from different vendors. Working together, collaboration innovation, and interconnection must be the inevitable choice of future intelligent manufacturing.
Figure 3: Robot in the exposure area.
Page 1 of 2
Testimonial
"Advertising in PCB007 Magazine has been a great way to showcase our bare board testers to the right audience. The I-Connect007 team makes the process smooth and professional. We’re proud to be featured in such a trusted publication."
Klaus Koziol - atgSuggested Items
Indium Promotes Huang to Senior Manager, Marketing Communications
08/28/2025 | Indium CorporationWith its commitment to innovation and growth through employee development, Indium Corporation announces the promotion of Jingya Huang to Senior Manager, Marketing Communications, to continue to lead the company’s branding and promotional efforts.
Rehm Academy Expands Its Training Program
08/28/2025 | Rehm Thermal SystemsThe demands on modern industrial companies and employees continue to rise, and therefore, the topic of further education is becoming increasingly important today.
MacDermid Alpha Awarded for Innovation: Driving Process Optimization and Efficiency with Major Indian EMS Provider
08/28/2025 | MacDermid Alpha Electronics SolutionsMacDermid Alpha Electronics Solutions, a leading global supplier of integrated materials for the electronics industry, is recognized by one of India’s top EMS providers, Syrma SGS, with an award for innovation that advanced process optimization, enhanced operational efficiency, and yield gains.
Integrated Solutions for Board-level Reliability: A Smarter Path Forward
08/27/2025 | Alan Gardner, MacDermid Alpha Electronics SolutionsIn today’s electronics manufacturing landscape, reliability is no longer just a benchmark but a business imperative. As industries such as automotive, aerospace, and high-performance computing (HPC) push the boundaries of innovation, the demand for dependable board-level performance under extreme conditions has never been greater.
ZESTRON Expands Capabilities with Addition of the EPS by i-Tech AG 75 Pallet Cleaning System
08/26/2025 | ZESTRONZESTRON, the global leader in high-precision cleaning solutions and services, is excited to announce the addition of a new capability in its Technical Center in Manassas, VA: