-
- News
- Books
Featured Books
- smt007 Magazine
Latest Issues
Current IssueSpotlight on India
We invite you on a virtual tour of India’s thriving ecosystem, guided by the Global Electronics Association’s India office staff, who share their insights into the region’s growth and opportunities.
Supply Chain Strategies
A successful brand is built on strong customer relationships—anchored by a well-orchestrated supply chain at its core. This month, we look at how managing your supply chain directly influences customer perception.
What's Your Sweet Spot?
Are you in a niche that’s growing or shrinking? Is it time to reassess and refocus? We spotlight companies thriving by redefining or reinforcing their niche. What are their insights?
- Articles
- Columns
- Links
- Media kit
||| MENU - smt007 Magazine
Estimated reading time: 4 minutes
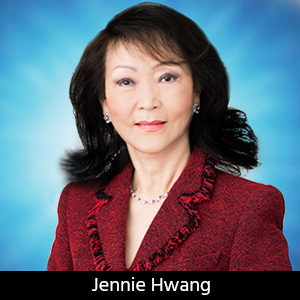
The Role of Bismuth (Bi) in Electronics: A Prelude
Bismuth (Bi) is a unique element on multiple fronts. For your eyes, bismuth can be grown into beautiful iridescent rainbow crystals. When it comes to considering applications in electronics and microelectronics industry, over last three decades, the industry has shied away from using Bi, at least not in standard practices in mass production. However, an interest has surfaced recently.
After receiving various questions and comments, this series on "The Role of Bismuth (Bi) in Electronics," is tailored to electronics and microelectronics industry, to provide an overview in its entirety in the areas of importance to industry applications going forward.
Backdrop
The Restriction of Hazardous Substances (RoHS) initiated by the European Commission indeed was impactful, similar to the Montreal Protocol—an international treaty agreed in 1987. Both RoHS and the Protocol have had profound impact on the electronics industry. The Protocol phased out the production of substances that are responsible for ozone depletion; and RoHS has driven the worldwide implementation of lead-free electronics.
On lead-free solder materials, our teams through the past two decades have conducted research far before the RoHS becoming effective. Our first patent (Patent Number: 5,520,752) in this area was filed in 1994 and issued in 1996. The patent, jointly owned by the U.S. Army of the Department of Defense and myself, disclosed Bi-containing lead-free alloys to replace SnPb solder including SnAgBi system, SnAgInBi system, and SnAgCuBi system and other non-Bi-containing lead-free systems. The patent embodies the concept and inventiveness of high-performance, lead-free alloys with the objective to serve military electronics.
The broad-based awareness of and the industry’s effort in lead-free alloys started after the RoHS Directive was published by the European Commission and when the lead-free electronics appeared to become a reality (RoHS 1 in 2002/2004, RoHS2 in 2011/2013). Variations of EU RoHS adopted by other countries were later deployed globally in the mid-2000s and thereafter.
It is cheerfully intriguing to observe that some esteemed engineers and scientists have always showed an interest in novel lead-free solder materials including Bi-bearing lead-free alloys. This is vividly demonstrated by the attendance at my lectures covering lead-free and the role of Bi, which were delivered in the Professional Development Courses offered by NEPCON West and NEPCON Japan in 1997–2003, IPC lead-free roadshows in 2003–2013, and at in-house programs at OEMs and NASA facilities over the last two decades, as well as recently (2017) by SMTA webtorial programs.
Fifteen years passed by; how is the lead-free electronics doing—its track record during this fifteen-year run and its outlook? And what is the role of Bi in the lead-free arena marching forward?
SAC system, specifically, SAC305 (Sn3.0Ag0.5Cu), has been widely known and used as a de facto “standard” alloy in the industry for the past 15 years. However, during this period, for a designed performance or other purposes, different alloys outside the SAC system have been successfully used by some OEMs at their discretion, albeit in special low-volume applications.
On the subject of Bi in the lead-free arena, one important point worth noting is to differentiate two separate Bi-containing lead-free alloy systems—Sn-based alloy system vs. Bi-based alloy system. The two systems bear separate metallurgical phenomena, thus physical properties and mechanical behavior, which in turn their respective intended applications and product service environments.
Bismuth can be introduced either through the supply chain (not by design) or by design. With the deliberation of all relevant parameters, theoretical and practical, Bi plays a potent role in electronic solder interconnections. The proper use of Bi can benefit the performance and reliability of electronic package and assembly including solder joint performance, tin whisker mitigation, among others.1,2
By the same token, its improper use could impart deleterious effects to solder joints, thus product reliability. An adequate understanding of the properties and performance parameters of Bi is critical to the product reliability. This series will discuss the relevant areas of Bi to help dispel misconceptions and to demonstrate performance criteria related to Bi. The goal is to help achieve the desired level of performance and product reliability.
Topics to be Covered
This series will highlight the following topics:
- Bi: Characteristics, resources, safety data
- Bi effects in 63Sn37Pb solder joint
- Physical properties
- Mechanical behavior
- Effects of Bi from component coating and PCB surface finish
- Dissolving into solder joint
- Estimation of concentration of Bi in solder joint
- Effect of compositional change
- Bi effects in SAC solder joint (SnAgCuBi)
- Compositional change
- Stress vs. strain
- Fatigue behavior
- Bi effects in other Pb-free alloys (SnCu, SnAg, SnAgIn)
- Stress vs. strain
- Fatigue performance
- Historically established Bi-containing electronic solder alloys
- Pb-containing
- Pb-free
- Bi-containing Pb-free solder alloys
- Melting temperature range
- Compositional control level
- Physical, mechanical properties
- BGA thermal fatigue performance
- PCB through-hole fillet-lifting vs. Bi
- Causes
- Solutions
- Low temperature BiPbSn phase
- Presence or absence
- Thermograms
- Detectable or non-detectable effects
- General guidelines
- Design limits in Pb-free solder joints vs. solder joint reliability
- Sn-based Bi-bearing solder vs. Bi-based solder
- Differentiation
- Physical properties
- Mechanical properties
- Service environments
References
1. Yves Palmieri, Bismuth Institute Information Center, Belgium.
2. Jennie S. Hwang, “Bismuth in Electronic Solders,” Bulletin of Bismuth Institute Information Center, Belgium, #78, 2001.
More Columns from SMT Perspectives and Prospects
SMT Perspectives and Prospects: Warren Buffett’s Perpetual Wisdom, Part 2SMT Perspectives and Prospects: Warren Buffett’s Perpetual Wisdom, Part 1
SMT Perspectives and Prospects: Artificial Intelligence, Part 5: Brain, Mind, Intelligence
SMT Perspectives and Prospects: Artificial Intelligence, Part 4—Prompt Engineering
SMT Perspectives and Prospects: The AI Era, Part 3: LLMs, SLMs, and Foundation Models
SMT Perspectives and Prospects: A Dose of Wisdom
SMT Prospects and Perspectives: AI Opportunities, Challenges, and Possibilities, Part 1
SMT Perspectives and Prospects: Critical Materials—A Compelling Case, Part 3