-
- News
- Books
Featured Books
- pcb007 Magazine
Latest Issues
Current IssueInventing the Future with SEL
Two years after launching its state-of-the-art PCB facility, SEL shares lessons in vision, execution, and innovation, plus insights from industry icons and technology leaders shaping the future of PCB fabrication.
Sales: From Pitch to PO
From the first cold call to finally receiving that first purchase order, the July PCB007 Magazine breaks down some critical parts of the sales stack. To up your sales game, read on!
The Hole Truth: Via Integrity in an HDI World
From the drilled hole to registration across multiple sequential lamination cycles, to the quality of your copper plating, via reliability in an HDI world is becoming an ever-greater challenge. This month we look at “The Hole Truth,” from creating the “perfect” via to how you can assure via quality and reliability, the first time, every time.
- Articles
- Columns
- Links
- Media kit
||| MENU - pcb007 Magazine
Estimated reading time: 5 minutes
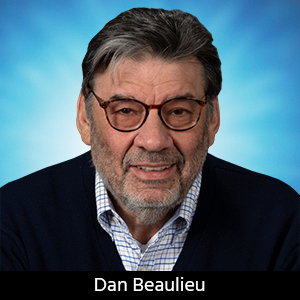
It’s Only Common Sense: Building Leaders—The Time is Now
The hottest topic on the PCB circuit these days is the lack of young people in our industry. As the rest of us get older, it is finally occurring to us that there is no one following in our footsteps, and there is no one there to fill our shoes, when we decide enough is enough.
Thinking about this the other day, I remember what it was like when I started in this industry so many years ago. It was with a company called Maine Electronics, a wholly owned subsidiary of Rockwell International. Originally, I was supposed to be an English teacher, but after about an hour of student teaching, I decided that, honorable career that it was, teaching was not for me. So, then I had to decide what it was I was going to do to make a living if teaching was out.
Through a series of circumstances and coincidences and a long story best left for another day, I found myself hired at Maine Electronics as what was then called a program coordinator, which was a fancy name for an expeditor. My job was to track and report the status of every single PCB in the programs I was handling. In those pre-computer days, taking status and tracking boards was all done manually, by myself and seven other program coordinators. It was an interesting group. All of us were young, all of us were men of course; it was only much later that management realized that women could track and expedite boards as well as men could—better actually. We were all under 24. And we all had some amount of college under our belt; some of us had degrees but most did not yet. We all had the same demographics politically and socially, which meant long hair and liberal politics, and that was ironic when you think that we were working on Minuteman missiles and F-11 bombers.
You can just imagine the fun we had chasing our boards all over the shop and competing with one another to see who could get supervisors to work on their boards first. It was a time when our technology was respected enough that our customers were used to late dates and catch-back schedules. We lived under a great deal of pressure, but as always, when looking back at hard times, today when we get together, we consider those the good old days.
I was fortunate to begin my career in a company what was one of the leading PCB producers in the world. The shop was run by very experienced PCB experts from either Rockwell Autonetics in Anaheim or left-overs from the previous company, Maine Research, which had been designed and built as the most advanced PCB facility in the world. Just to give you an example, we were building controlled impedance boards before people even knew there was such a thing.
But the point I want to make is that we young people were trained every day of the week. Everything we did was a lesson for our future. Once we had been there a year or so they started grooming us for the next step in our career development. Some of us were destined to become process engineers, others were to become supervisors or quality managers and a few of us where trained as sales people. In other words, from the very first day we were hired we were considered long-time members of the Rockwell family, and training us was considered an investment in the future of the company. Our managers were tasked with starting all of us on the career path of our choice…within the company.
They were always working on the future of the company, with great intention. There was nothing haphazard about it.
And now, as we look back on the past 20 years, how many of us have done that same thing? Not many of us, which is why we are in the dilemma we are in today. I daresay part of it is due to the arrogance of the boomer generation. We’ve always thought that we were the coolest generation with no regard or much respect, for that matter, for the generations that followed us. We thought we would live forever, so why bother looking back? We could not imagine a world without us and so we concentrated on the present with little interest in the future, especially a future we would not be part of.
Thus, here we are, a bunch of old gray men and a few better-looking women, wondering how we are going to sustain our industry going forward, wondering who is going to carry the torch into the future.
But here is a reality check for you: It’s not really that we have had a shortage of young people in our shops because our companies actually do have some young people working in them. Take a walk through your shop, and look around. Notice anything? Young people are there. They have been there all along, working in the plating department or the drill room or in shipping; but we have not taken the time to notice them. We have not taken the time to talk to them, to get to know them, to find out what they are like, and what they like to do when they’re not working. We need to sit down and talk to them and find out what their career aspirations are. We need to work with them, develop them just like those professionals at Rockwell did with me and my fellow program coordinators so many years ago. And then we must sit by their side and start working out their career path. Showing them that a career in the PCB business can be a good career. Demonstrating to them just how important our work is. Explaining to them what these little green cards go into and how they are changing the world.
We should make them believe that this is a good industry, an industry to be proud of, and an industry that can provide a bright future for the person who is willing to work and to learn. And we should be willing to teach that person and help him or her to become a viable, contributing member of our PCB community both for today and the future.
It’s only common sense.
More Columns from It's Only Common Sense
It’s Only Common Sense: Why Failure Is an Opportunity for GrowthIt’s Only Common Sense: Stop Chasing New Customers and Start Keeping the Ones You Have
It’s Only Common Sense: Sales as a Team Sport
It’s Only Common Sense: How to Win Back Lost Customers
It’s Only Common Sense: Knowing When to Walk Away
It’s Only Common Sense: Customer Service Is Sales in Disguise
It’s Only Common Sense: Your Guide to Better Time Management
It’s Only Common Sense: Selling to Today's Generation of Buyers