-
- News
- Books
Featured Books
- smt007 Magazine
Latest Issues
Current IssueWhat's Your Sweet Spot?
Are you in a niche that’s growing or shrinking? Is it time to reassess and refocus? We spotlight companies thriving by redefining or reinforcing their niche. What are their insights?
Moving Forward With Confidence
In this issue, we focus on sales and quoting, workforce training, new IPC leadership in the U.S. and Canada, the effects of tariffs, CFX standards, and much more—all designed to provide perspective as you move through the cloud bank of today's shifting economic market.
Intelligent Test and Inspection
Are you ready to explore the cutting-edge advancements shaping the electronics manufacturing industry? The May 2025 issue of SMT007 Magazine is packed with insights, innovations, and expert perspectives that you won’t want to miss.
- Articles
- Columns
- Links
- Media kit
||| MENU - smt007 Magazine
Implementing a Capacity Planning Tool
September 22, 2017 | David Prunier, MC AssemblyEstimated reading time: 4 minutes
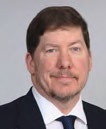
So, you have a wedding coming up. Among the struggles of deciding what colors the bridesmaids are going to be wearing and who gets to sit next to eccentric old Uncle Russ, you may have had to stop and ask yourself how many people can fit into the church? Then how many people can fit into each pew, (comfortably) and especially, who can endure Uncle Russ for an hour. This little exercise of determining how many relatives, friends and strangers can fit in the church is in its simplest form and example of capacity planning. For the benefit of our readers, this discussion will focus on the use of capacity planning (CP) in the context related to contract manufacturing. Uncle Russ symbolizes the unknown constraints that may influence your ability to meet customer’s demand, which a good CP tool should take into consideration.
In our first example of determining how many people would fit in the church, we were doing a rough-cut capacity plan. Finite capacity planning (FCP) was determining how many people could fit into each pew, seat or bench. Unfortunately, not all CP is that simple.
For those who grew up in manufacturing during the 1980s, you probably remember the term MRP II. Manufacturing Resource Planning or MRP II is not to be confused with Material Requirements Planning (MRP). One is the software used to manage the inventory, materials purchasing activities and production plans to meet the customer delivery dates (MRP) versus the methods used for efficiently managing the manufacturing resources of the company (MRP II). We are not going to bore you with the details behind each terminology but rather we want to focus in one of the important elements of MRP II where we see most EMS companies struggling. We will focus our discussion in the Capacity Planning process under the MRP II method. If you would like to learn more about MRP II, we suggest you read the book "The Oliver Wight Class A Standard for Business Excellence."
One of the more common challenges we see in the EMS world is that through the outsourcing of their manufacturing, many OEMs have forgotten the fundamentals of supply chain management and expect quick turnaround on orders without taking into consideration the whole supply chain constraints or the impact of not providing accurate forecasts to the EMS partner. Old Uncle Russ can, too easily, disrupt a great capacity plan if we ignore the possibility of his visit! In this paper, we will talk about some of the fundamentals but also about possible solutions in the reality of a not so perfect world.
CP is important to us in the contract manufacturing or EMS world for several reasons. It helps in level loading our factory, it helps us balance demand with available capacity, it helps to identify bottlenecks-those obstacles that might otherwise impede the flow of product and most importantly it helps us to improve our on-time delivery performance; something both near and dear to our customers and ourselves in the EMS world. If you’ve read anything regarding the “Theory of Constraints,” you know how important it is to identify all potential and existing bottlenecks associated with the flow of product. This may also include all the process steps concerned with external operations within your supply chain as well.
CP can concern itself with labor, design and machine capacity. There are several key assumptions that must be made for CP to work properly. These serve as an excellent starting place for those interested in developing a good CP model. These are the following core assumptions:
1. All material is available when needed.
2. All machines are up and running effectively.
3. All labor standards have been reviewed and validated.
4. All part numbers/model numbers are accurate.
5. There are sufficient available resources to operate equipment, run planning tools, complete tasks.
6. All appropriate work centers have been identified.
7. All available resources are identified in each work center.
8. Queue times are identified. All wait periods, set-up, transfer times, transaction times and transport.
9. Management support for implementing the tool is given and there is a champion for the project.
You may find that you have your own site-specific gates to making sure that the plan can work effectively, and this should be included in your overall assessment and timeline when undertaking this project. The nine assumptions listed above should get you most, if not all the way there.
How many of us in the EMS and OEM worlds have found ourselves wrestling with a master scheduler or planner to have their product put in the queue only to have it bumped or find out that something else prevented it from being run in the time slot allotted? Uncle Russ always shows up at the most inopportune time! This problem is a very common one, almost as common as finding out that most EMS providers using an MRP system also have a CP module available to them but chose to either selectively use its outputs or to ignore its existence completely.
This article was originally published in the September 2017 issue of SMT Magazine.
Suggested Items
Zollner Completes Full Acquisition of Bluechips Microhouse
07/01/2025 | Zollner Elektronik AGZollner Elektronik AG has successfully finalized its com- plete takeover of Bluechips Microhouse Co., Ltd., in Thailand. In the future the company will operate as part of the Zollner Group of companies under the leadership of Thomas Kiefl – strategically networked, technologically focused and internationally oriented.
Inission Acquires the Lithuanian Company Selteka
07/01/2025 | InissionInission AB has signed an agreement to acquire 100% of UAB Selteka. Selteka is a well-respected EMS (electronics manufacturing services) company with operations located in Kaunas, Lithuania.
Kitron Strengthens Order Backlog with EUR 11 Million Contract for Defense Communication
07/01/2025 | KitronKitron has received an order valued at EUR 11 million to produce advanced military communication products destined for the European market.
TRI Unveils New Multi-Camera AOI, TR7500 SIII Ultra
07/01/2025 | TRITest Research, Inc. (TRI), the leading test and inspection systems provider for the electronics manufacturing industry, proudly introduces the new TR7500 SIII Ultra.
IMI Wins Gold Award for Best Managed Technology Company at FinanceAsia’s 29th Asia’s Best Companies Awards
07/01/2025 | IMIIntegrated Micro-Electronics Inc. (IMI) has been awarded the prestigious Gold Award for Best Managed Technology Company at the 29th edition of the Asia’s Best Companies Awards, hosted by FinanceAsia.