3D Printed Electronics for Printed Circuit Structures
October 4, 2017 | Samuel LeBlanc, Paul Deffenbaugh, Jacob Denkins, and Kenneth Church nSCRYPT INC.Estimated reading time: 1 minute
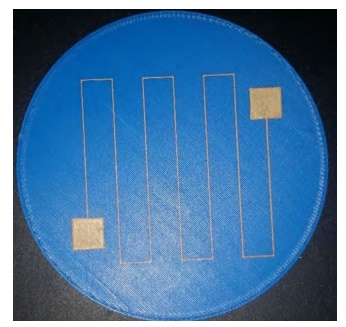
Abstract
Printed electronics is a familiar term that is taking on more meaning as the technology matures. Flexible electronics is sometimes referred to as a subset of this and the printing approach is one of the enabling factors for roll-to-roll processes. Printed electronics is improving in performance and has many applications that compete directly with printed circuit boards. The advantage of roll-to-roll is the speed of manufacturing, the large areas possible, and a reduction in costs.
As this technology continues to mature, it is also merging with the high-profile 3D printing. 3D printing is becoming more than just a rapid prototyping tool and more than just printing small plastic toys. Companies are embracing 3D printing as a manufacturing approach to fabricate complex parts that cannot be done using traditional manufacturing techniques. The combination of 3D printing and printed electronics has the potential to make novel products and, more specifically, to make objects electrically functional. Electrically functional objects have the advantage of competing with printed circuit boards.
Printed circuit structures will be a new approach to electronic packaging. It is the desire of many companies to reduce assembly processes, decrease the size of the electronics, and do this at a reduced cost. This is challenging, but the potential of printing the structure and the electronics as a single monolithic unit has many advantages. This will reduce the human touch in assembly, as the electronics and the object are printed. This will increase the ruggedness of the product, as it is a monolithic device.
This will eliminate wires, solder, and connectors, making the device smaller. This has the potential to be the future of printed circuit boards and microelectronic packaging. This article will show working demonstrations of printed circuit structures, the obstacles, and the potential future of 3D printed electronics.
To read the full version of this article which appeared in the September 2017 issue of The PCB Magazine, click here.
Testimonial
"The I-Connect007 team is outstanding—kind, responsive, and a true marketing partner. Their design team created fresh, eye-catching ads, and their editorial support polished our content to let our brand shine. Thank you all! "
Sweeney Ng - CEE PCBSuggested Items
Indium Corporation Promotes Two Leaders in EMEA (Europe, Middle East, and Africa) Markets
08/05/2025 | Indium CorporationWith its commitment to innovation and growth through employee development, Indium Corporation today announced the promotions of Andy Seager to Associate Director, Continental Sales (EMEA), and Karthik Vijay to Senior Technical Manager (EMEA). These advancements reflect their contributions to the company’s continued innovative efforts with customers across Europe, the Middle East, and Africa (EMEA).
MacDermid Alpha Electronics Solutions Unveils Unified Global Website to Deepen Customer, Talent, and Stakeholder Engagement
07/31/2025 | MacDermid Alpha Electronics SolutionsMacDermid Alpha Electronics Solutions, the electronics business of Elements Solutions Inc, today launched macdermidalpha.com - a unified global website built to deepen digital engagement. The launch marks a significant milestone in the business’ ongoing commitment to delivering more meaningful, interactive, and impactful experiences for its customers, talent, and stakeholders worldwide.
KOKI to Showcase Analytical Services and New HF1200 Solder Paste at SMTA Guadalajara 2025
07/31/2025 | KOKIKOKI, a global leader in advanced soldering materials and process optimization services, will exhibit at the SMTA Guadalajara Expo & Tech Forum, taking place September 17 & 18, 2025 at Expo Guadalajara, Salón Jalisco Halls D & E in Guadalajara, Mexico.
Weller Tools Supports Future Talent with Exclusive Donation to SMTA Michigan Student Soldering Competition
07/23/2025 | Weller ToolsWeller Tools, the industry leader in hand soldering solutions, is proud to announce its support of the upcoming SMTA Michigan Expo & Tech Forum by donating a limited-edition 80th Anniversary Black Soldering Set to the event’s student soldering competition.
Koh Young Appoints Tom Hattori as President of Koh Young Japan
07/21/2025 | Koh YoungKoh Young Technology, the global leader in True 3D measurement-based inspection solutions, announced the appointment of Tom Hattori as President of Koh Young Japan (JKY).