-
- News
- Books
Featured Books
- pcb007 Magazine
Latest Issues
Current IssueInventing the Future with SEL
Two years after launching its state-of-the-art PCB facility, SEL shares lessons in vision, execution, and innovation, plus insights from industry icons and technology leaders shaping the future of PCB fabrication.
Sales: From Pitch to PO
From the first cold call to finally receiving that first purchase order, the July PCB007 Magazine breaks down some critical parts of the sales stack. To up your sales game, read on!
The Hole Truth: Via Integrity in an HDI World
From the drilled hole to registration across multiple sequential lamination cycles, to the quality of your copper plating, via reliability in an HDI world is becoming an ever-greater challenge. This month we look at “The Hole Truth,” from creating the “perfect” via to how you can assure via quality and reliability, the first time, every time.
- Articles
- Columns
- Links
- Media kit
||| MENU - pcb007 Magazine
IPC Status Update: Training, Standards, and More!
October 10, 2017 | Patty Goldman, I-Connect007Estimated reading time: 8 minutes
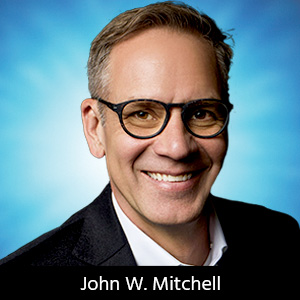
At the recent IPC Fall committee meetings that are co-located with the SMTA International conference and show, IPC’s president and CEO, John Mitchell, sat down for a chat with me for an update on what’s happening at IPC.
Patty Goldman: Good to see you again, John, so what's new?
John Mitchell: All kinds of good stuff. Obviously, the IPC Fall Committee Meeting is going on with great attendance, and there are a lot of exciting things happening. We just finished the awards luncheon where we recognized more than one hundred standards committee volunteers for their good work.
We’re able to announce that the J-STD-001/A610, revision G, is coming out around the end of October. These are major documents and that's exciting. We are updating some nice red-line training materials on the revision so people can very quickly assess what the differences are.
Next, the IPC board meeting is happening in the first week of October. Typically, at the fourth quarter board meeting, we get the approval for a budget for the following year, and that's a big deal; this is where / when we set our initiatives and other things that we're looking to do in the following year.
As a global organization, we're looking at trying to increase our exposure as such. Even with 40+% of our membership based outside of the U.S., many are not aware that we're a global industry association, and that the standards are globally generated. Some people still think, "Oh, it's a U.S. based standard.”
Goldman: Well, I suppose that’s because so much of IPC is based in the U.S.
Mitchell: Perhaps. But that's like saying your Big Mac is made in the U.S. and shipped to Europe when you buy it there. It's not. Similarly, IPC standards are built by local experts from around the world. Right now, you can open a standard and you see the list of all the committee members and their companies and where they're located—they're all over the planet. We're looking to put a new symbol on the standards, like a globe with a number, that will represent how many countries were involved in that particular standard development.
Goldman: That sounds like a good idea, very simple, but effective.
Mitchell: Yes, it would be a simple thing. You get it. With whatever standard it is you can say, "Look, 17 countries participated in this so that's not just the U.S." The U.S. is but one country represented. So that's one thing that you might see coming out, as we go forward.
We're also looking at revamping some committees along the same globalization lines, to make sure we have global representation on the board. Our GR committee is recommending, also for approval at the board meeting, that they change their structure so that we're better represented in Europe and Asia as well as North America,. And I'm going to be presenting the same type of thing to the committee chairmen at the TAEC. This will help ensure that the standards and the leadership are represented more globally as well.
Other initiatives, not in any order, deal with some of the recent developments, like with the IPC-6012 automotive addendum. We're looking more at the transportation sector. We've been looking at it for a couple of decades but haven't gotten a lot of interest. Well, there seems to be a lot of interest now with the increased content of electronics in vehicles, etc.
We are in the process of finishing the A610 automotive addendum, and now we have an initiative in the transportation sector—the IPC-6012 automotive addendum. We are trying to make sure that the automotive industry’s needs are being met and are more broadly represented through standards participation. This more or less mirrors other industries like aerospace and defense, where we already have good participation and standards.
Goldman: I would say the automotive OEMs are waking up to how much they need electronics specifications.
Mitchell: You may be right. So, we want to be talking directly with the OEMs and Tier 1 companines primarily, and getting them more involved in our standards committees. In China, GM has asked for specific training from IPC around the 6012−automotive addendum. That has now been developed. Initially, you would get your 6012−standard training as the prerequisite for the 6012 automotive addendum.
Goldman: I can remember when the automotive guys said that the space stuff wasn't really good enough for them and everyone said, "What? Why?" But now we understand that “under the hood” is a pretty harsh environment.
Mitchell: This transportation initiative is one we're putting forward to the board to fund and drive. In addition to everything we're currently doing, we're trying to bring some expertise in to better handle that.
Another initiative is education, which also very important to us. You'll see us working much more with universities and collaborating with other groups to provide education and training. The last initiative is infrastructure and efficiency changes, so we can help our membership work with us in a more efficient manner.
Goldman: How is IPC EDGE coming along?
Mitchell: IPC EDGE is coming along well. We hired a new senior director of learning and professional development who is focused on growing IPC EDGE and will work to expand IPC’s online educational offerings to help address the skills gap in the electronics industry and reach the next generation of employees .
Goldman: You know me. I just checked the other day and I didn't find anything for PCB manufacturers in there.
Mitchell: Let me tell you about that. When we ask the PCB members what training they would find useful, we don’t get much input. But we are interested in trying to fulfill their needs. We've launched a global needs assessment for which we hired an outside organization to survey our members on their professional development needs —and they're looking across all the different segments of the value chain as well as all the different regions. They started with some specific interviews, face-to-face discussions, and then they've gone to surveys as well. We're hoping to have that information soon, in fact, there's a draft meeting of it happening right now in New York. So that's why you don't have all our folks here, because some of them are out there.
Again, we don't have all the resources in the world. Trying to serve a $2+ trillion electronics industry, we have to focus where we can make the biggest impact for the industry and we're looking at that as well. And that will drive content and we'll build a strategy roadmap based on that information. Then we’ll see where our path is over the next couple of years.
But we are doing things for the PCB guys. As part of our strategic discussions we look at each of our immediate areas. Our standards, our education, our advocacy, and our solutions group. And we want to make sure: Who are we helping? How are we helping? What are we doing? What should we be doing that we're not doing? Then we try to prioritize and align resources.
On the advocacy side, as I look back over the last five years I've been here...What are the big wins that we've had in advocacy? In the ITAR category XI (military electronics), we got PCBs actually enumerated in there as a protective group. Under TSCA, we got some actual wording inserted in the TSCA reform bill. Then we helped drive the passage of the RAMI bill, which provided funding for advanced manufacturing centers of excellence, which provided funds to NextFlex group, as well as DMDII (Digital Manufacturing and Design Innovation Institute) projects. IPC is participating in both. And then the gold cyanide issue in China. These are key wins and they've all been for the PCB industry. On the advocacy front, only a small part has been for the assembly side, which I thought was interesting.
Goldman: I was very impressed with IMPACT−Washington D.C. this year. The IPC team in Washington put together an outstanding group of senators, representatives and government department reps. Everybody who attended was totally impressed. Everybody that I spoke with was just blown away by that. Heck, there was a meeting with Scott Pruitt, the head of EPA—and it was very positive.
Mitchell: Oh, thank you. Good to hear. On the education front, we're trying to align some of our activities where some government funding is as well, so we can move some things a little faster. We are trying to do things like that. A lot of our PCB companies, as you would categorize it for governmental funding, are the small-to-medium-size groups. You don't have many $100 million companies. There's a couple, but there aren’t that many. They have lower margins, so it's a tough business to be in.
But for all those size companies, one of the things that they need is training of all different kinds. We're looking to find ways to get funding so that we can provide some of it for free, some of it for very low-cost. I remember when I was working at a couple of different companies, you'd promote somebody to manager, put them in a new role, and they'd say, "Okay, where's my training?" And they’d hear in response, "Ask me if you have any questions, I'd be happy to tell you." That's about the extent of the training, and that's even at some decent-sized companies. Well, if we can help plug that gap, what a boon to all the small- and medium-sized companies that don't have large budgets to go figure this stuff out. So that's an area where we're looking to focus as well.
Goldman: Excellent, this is all good news. John, thank you so much for your time.
Mitchell: Thanks, Patty.
Testimonial
"We’re proud to call I-Connect007 a trusted partner. Their innovative approach and industry insight made our podcast collaboration a success by connecting us with the right audience and delivering real results."
Julia McCaffrey - NCAB GroupSuggested Items
Meet the Author Podcast: Martyn Gaudion Unpacks the Secrets of High-Speed PCB Design
07/16/2025 | I-Connect007In this special Meet the Author episode of the On the Line with… podcast, Nolan Johnson sits down with Martyn Gaudion, signal integrity expert, managing director of Polar Instruments, and three-time author in I-Connect007’s popular The Printed Circuit Designer’s Guide to... series.
Intervala Hosts Employee Car and Motorcycle Show, Benefit Nonprofits
08/27/2024 | IntervalaIntervala hosted an employee car and motorcycle show, aptly named the Vala-Cruise and it was a roaring success! Employees had the chance to show off their prized wheels, and it was incredible to see the variety and passion on display.
KIC Honored with IPC Recognition for 25 Years of Membership and Contributions to Electronics Manufacturing Industry
06/24/2024 | KICKIC, a renowned pioneer in thermal process and temperature measurement solutions for electronics manufacturing, is proud to announce that it has been recognized by IPC for 25 years of membership and significant contributions to electronics manufacturing.
Boeing Starliner Spacecraft Completes Successful Crewed Docking with International Space Station
06/07/2024 | BoeingNASA astronauts Barry "Butch" Wilmore and Sunita "Suni" Williams successfully docked Boeing's Starliner spacecraft to the International Space Station (ISS), about 26 hours after launching from Cape Canaveral Space Force Station.
KIC’s Miles Moreau to Present Profiling Basics and Best Practices at SMTA Wisconsin Chapter PCBA Profile Workshop
01/25/2024 | KICKIC, a renowned pioneer in thermal process and temperature measurement solutions for electronics manufacturing, announces that Miles Moreau, General Manager, will be a featured speaker at the SMTA Wisconsin Chapter In-Person PCBA Profile Workshop.