-
- News
- Books
Featured Books
- smt007 Magazine
Latest Issues
Current IssueWhat's Your Sweet Spot?
Are you in a niche that’s growing or shrinking? Is it time to reassess and refocus? We spotlight companies thriving by redefining or reinforcing their niche. What are their insights?
Moving Forward With Confidence
In this issue, we focus on sales and quoting, workforce training, new IPC leadership in the U.S. and Canada, the effects of tariffs, CFX standards, and much more—all designed to provide perspective as you move through the cloud bank of today's shifting economic market.
Intelligent Test and Inspection
Are you ready to explore the cutting-edge advancements shaping the electronics manufacturing industry? The May 2025 issue of SMT007 Magazine is packed with insights, innovations, and expert perspectives that you won’t want to miss.
- Articles
- Columns
- Links
- Media kit
||| MENU - smt007 Magazine
Counterfeit: A Quality Conundrum
October 18, 2017 | Michael Ford, Aegis Software Corp.Estimated reading time: 8 minutes
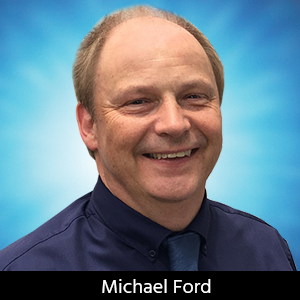
There is an imminent, critical challenge facing every manufacturer in the industry. The rise in the ingress of counterfeit materials into the supply chain has made them prolific, though yet, the extent is understated. What needs to be faced now is the need for incoming inspection, but at what cost to industry, and does anyone remember how to do it?
Going back 20 years, the incoming inspection of materials was common throughout the electronics assembly industry. At that time, component material and production technologies were relatively new, with sizes beginning to diminish, led by design pressure, which gave rise to what we would now regard as frequent failures. Having to repair or replace circuit boards after assembly, or later once assembled on the main production lines, was a very expensive challenge. I saw numerous cases of production lines where epidemic rates of material-related quality issues had been detected, and it was decided to simply remove the defective products from the line so that the line could continue while the products were being re-worked. Unfortunately, the re-work rate was often longer than the rate at which defects were discovered, resulting in significant stock-piles. Once, to compound the problem, visitors were due to be touring the plant the next day. Local companies selling very large black sheets saw their sales sky-rocket, as defective products in the factory were hidden in every place conceivable.
The situation was not a one-off. This was daily life at so many manufacturing sites back in the “wild West” days. To be fair, faulty materials were not the only contributor to defect rates that were so bad, a quality manager today wouldn’t allow the factory to produce a single thing. Assembly processes, especially SMT itself a relatively new technology, were also quite variable in those days. Materials, however, were the one thing that could not be controlled or addressed by industrial engineering practice. The solution, as we would say today, was to “left-shift” the problem into the material receiving operation. There, materials could be measured and inspected as they were booked into the factory, so as to engender confidence that they would be fit for production and not contribute to assembly line failures.
In fact, a great deal of testing also ended up being introduced at many stages in the production flow, as the final assembly line became the one thing in the factory that must not stop, as it would cause delivery issues to customers. Increased forms of in-line testing and inspection, including automated methods such as ICT, AOI, etc., became commonplace and continue to be regarded as essential. Segmentation of production areas, each with associated buffer stock, also became common. The increased cost to manufacturing was quite severe and contributed in no small way to manufacturing moving overseas to areas where the labor needed to perform all of these enhanced tasks was cheaper.
In the wild West, however, action still needed to be taken to reduce the costs of test and inspection as much as possible to keep what little remained competitive. As far as incoming inspection was concerned, manufacturers started to extend relationships with material suppliers to provide guidance on expected quality levels and provide help and training in sampling and testing so that suppliers could take ownership of the quality of their materials. Once a degree of control was established, contracts were put into place with responsibility for material defects to be placed with the supplier, relieving manufacturing progressively of incoming inspection tasks. The impact on the business of manufacturing was significant, which went beyond the labor saving.
With reliable material quality and supply, buffer stocks could be reduced and handling decreased. The age of efficient, Kanban and just in time (JIT) material delivery was enabled. Traceability was positioned as the police force of the supply-chain, as it could in theory assign responsibility for material defects found in manufacturing and beyond, back to the material supplier. In some cases, this happened successfully for those who took traceability seriously, utilizing the specialist software tools needed for complex production processes from multiple vendors with huge bills of materials. With relationships and trust in place between material suppliers and manufacturers, incoming material inspection has become almost redundant, providing significant cost reduction, which has already helped to tip the balance for the on-shore business case for manufacturing.
That is, until now.
It is discretely known by many key companies in the industry that the incidence of finding counterfeit materials in products is rapidly on the rise. They can be re-marked integrated circuits or passive components, even laminates within PCBs. Today’s counterfeiters are smart, buying used machinery on the open market for the cleaning, marking and re-packaging of discarded, obsolete, life-tested or inferior materials. Some of the tampering can be visible to a trained eye; odds are, however, that some cannot. The growth of this issue, it is said, could potentially destabilize trust within the industry. The use of effective traceability throughout the manufacturing process is a key weapon against counterfeit supply, as any instance where a counterfeit material is discovered during internal testing, inspection, or even in a failed product in the market, can be traced back, without doubt, to the source. Though this insurance is in place, the disruptive effect of counterfeit materials and the loss of confidence in quality has not been addressed, leading to the re-visit of the question of “left-shift,” that is the reinstatement or increase in the level of incoming inspection.
There are two problems associated with this. Firstly, there is the cost of labor. Adding indirect costs to manufacturing, after having enjoyed a good period of time without them, is going to be hard to accept. Then, there is the requirement of the skill and experience levels of those people who specify, manage and perform the tests. Even if we could find experienced people today, the cost of hiring engineers with degrees who know about the various statistic dependent sampling rules and test result interpretation is going to be significant. In-house experience is likely near to zero. It will be an uphill battle. To do nothing, however, would be like a ticking time-bomb. To raise the issue openly and vocally would invite a loss of confidence from customers. To put into place an active solution within manufacturing is a compelling alternative, so long as there is a positive cost justification. In other words, the ROI is not just based on what disaster may or may not someday happen.
We are, after all, in 2017, so we should be looking for a smarter, modern solution to this problem. Rather than looking at each individual element of the problem separately, it is better to create an overall specification for a material logistics system that will satisfy all of the key needs of the business. On the shopping list needs to be incoming inspection support, material logistics management and traceability. Especially in the electronics assembly industry, the solution needs to include support and understanding of complex processes, achieved by connection to automated processes, such as SMT machines, robots and associated inspection and test equipment. The combined singular solution then yields a net benefit for manufacturing, rather than representing an additional cost. Justification of the complete solution is then so much easier than trying to get disparate solutions working together in an attempt to address the business-critical need for quality.
Page 1 of 2
Suggested Items
Zollner Completes Full Acquisition of Bluechips Microhouse
07/01/2025 | Zollner Elektronik AGZollner Elektronik AG has successfully finalized its com- plete takeover of Bluechips Microhouse Co., Ltd., in Thailand. In the future the company will operate as part of the Zollner Group of companies under the leadership of Thomas Kiefl – strategically networked, technologically focused and internationally oriented.
Inission Acquires the Lithuanian Company Selteka
07/01/2025 | InissionInission AB has signed an agreement to acquire 100% of UAB Selteka. Selteka is a well-respected EMS (electronics manufacturing services) company with operations located in Kaunas, Lithuania.
Kitron Strengthens Order Backlog with EUR 11 Million Contract for Defense Communication
07/01/2025 | KitronKitron has received an order valued at EUR 11 million to produce advanced military communication products destined for the European market.
TRI Unveils New Multi-Camera AOI, TR7500 SIII Ultra
07/01/2025 | TRITest Research, Inc. (TRI), the leading test and inspection systems provider for the electronics manufacturing industry, proudly introduces the new TR7500 SIII Ultra.
IMI Wins Gold Award for Best Managed Technology Company at FinanceAsia’s 29th Asia’s Best Companies Awards
07/01/2025 | IMIIntegrated Micro-Electronics Inc. (IMI) has been awarded the prestigious Gold Award for Best Managed Technology Company at the 29th edition of the Asia’s Best Companies Awards, hosted by FinanceAsia.