-
- News
- Books
Featured Books
- smt007 Magazine
Latest Issues
Current IssueWhat's Your Sweet Spot?
Are you in a niche that’s growing or shrinking? Is it time to reassess and refocus? We spotlight companies thriving by redefining or reinforcing their niche. What are their insights?
Moving Forward With Confidence
In this issue, we focus on sales and quoting, workforce training, new IPC leadership in the U.S. and Canada, the effects of tariffs, CFX standards, and much more—all designed to provide perspective as you move through the cloud bank of today's shifting economic market.
Intelligent Test and Inspection
Are you ready to explore the cutting-edge advancements shaping the electronics manufacturing industry? The May 2025 issue of SMT007 Magazine is packed with insights, innovations, and expert perspectives that you won’t want to miss.
- Articles
- Columns
- Links
- Media kit
||| MENU - smt007 Magazine
Test Solutions Your EMS Partner Should Offer
October 20, 2017 | Neil Sharp, JJS ManufacturingEstimated reading time: 4 minutes
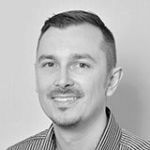
Testing is an integral part of the manufacturing process. It safeguards against defects and faults, so when a customer takes the product out of the box, it works perfectly.
When looking to outsource your manufacturing, you need to know that your chosen electronics manufacturing services (EMS) partner has good test solutions in place so that they can produce consistent, high-quality products to your customers’ requirements.
In this article, we will highlight the importance of test, and outline the different types of test your EMS partner should offer.
Test Versus Inspection
Test should not be confused with inspection. During production, products are usually inspected through manufacturing defects analysis (MDA). The purpose is to check that the right components are correctly soldered in the right places. A process of repeatable inspection is essential as it allows for any faults to be found early in the process, reducing re-work.
Inspection can confirm that the parts have been fitted in the right place—that is, the manufacturing process is sound—but can’t tell you that the finished product works. Implementing a test strategy is really the only way to confirm if a product works. And if it doesn’t work as expected, I’m sure you’d rather it was your EMS partner that found this out, and not your customer.
In-Circuit and Flying Probe
In-circuit test (ICT) and flying probe are arguably the two most popular types of Automated Test Equipment (ATE) used to test printed circuit board assemblies (PCBAs).
At a basic level, they are types of MDA. They cover the majority of the most common process faults that occur, such as open circuits (e.g. something not soldered), short circuits, passive component measurements (resistors and capacitors) and diode and transistor orientation.
But they also measure the value of components. ICT can provide limited analogue and digital measurements, a ‘vectorless’ test to check the soldering of pins to the PCB through a non-contact probe or plate, and even offers some basic functional testing. And flying probe offers limited optical inspection, which can add coverage for those components that can’t be accessed electrically.
For both flying probe and ICT you will need to provide a Bill of Materials (BOM) and Computer Aided Design (CAD) data, as well as populated and unpopulated sample PCBs.
Typically, you wouldn’t need to use both of these methods. A good EMS partner will help guide you on which will be the best solution for your product.
Boundary Scan
Boundary scan testing is used for checking the correct connection between large digital devices on a PCB. It uses test logic that has already been built into the digital integrated circuits (ICs) on the board, thereby removing the need for physical test probes and equipping manufacturers to debug and program complex digital circuits.
Boundary scan can be used in tandem with ICT or flying probe, but on a board with multiple ICs, it is more likely to be used as a standalone test method. Implementing this solution does require a tailored software program and the cost of the license needed to write the program is usually around £3,000 but this can increase upwards of £10,000 in some instances.
Cost aside, boundary scan is a reliable and quick test that takes just a few seconds and delivers in-circuit levels of test coverage and diagnostics for digital circuits.
Electrical Safety Testing
On electrical assemblies, electrical safety testing is essential as it helps ensure the integrity of the assembly. It’s essential for any product that uses electricity, and should be carried out as a matter of course.
The simplest form is portable appliance testing (PAT). A product is connected to PAT equipment, which checks whether it’s safe to use and that the relevant electrical components are insulated. For higher voltage products, a flash test should be implemented to check whether the insulators have enough strength for the voltage. A higher than usual voltage is applied and, to pass, it should be able to withstand this stress.
Functional Testing
Unlike the test methods above, this one is focused on the design rather than the manufacturing quality. It’s testing to see if the product works as it should.
This should be the final test before the product reaches the hands of the customer. While it adds little to the value to the production process, it does provide that extra comfort—you can sleep easy at night knowing your customers will receive products that do indeed work!
But functional test should never be relied on alone. Not least because if it doesn’t work at this point, there’s not much you can do except start from scratch. And a product can still pass a functional test even if something is wrong at a component level, for example missing and wrong value components can go undetected. This is why we always recommend implementing a robust test strategy, designed to verify each stage of the build process and sub assembly of the finished product.
Test should not be an afterthought. If treated as such there is a real possibility all the hard work and effort put into outsourcing your manufacturing will have been wasted. Selecting an outsourcing approach that incorporates a solid test strategy will help reduce costs, and maximize product reliability. The test options outlined here are not mutually exclusive; they cover different elements of the manufacturing process and, depending on your product, a combination should be implemented. Your EMS partner should work with you to devise the best test strategy for your needs.
Suggested Items
Zollner Completes Full Acquisition of Bluechips Microhouse
07/01/2025 | Zollner Elektronik AGZollner Elektronik AG has successfully finalized its com- plete takeover of Bluechips Microhouse Co., Ltd., in Thailand. In the future the company will operate as part of the Zollner Group of companies under the leadership of Thomas Kiefl – strategically networked, technologically focused and internationally oriented.
Inission Acquires the Lithuanian Company Selteka
07/01/2025 | InissionInission AB has signed an agreement to acquire 100% of UAB Selteka. Selteka is a well-respected EMS (electronics manufacturing services) company with operations located in Kaunas, Lithuania.
Kitron Strengthens Order Backlog with EUR 11 Million Contract for Defense Communication
07/01/2025 | KitronKitron has received an order valued at EUR 11 million to produce advanced military communication products destined for the European market.
TRI Unveils New Multi-Camera AOI, TR7500 SIII Ultra
07/01/2025 | TRITest Research, Inc. (TRI), the leading test and inspection systems provider for the electronics manufacturing industry, proudly introduces the new TR7500 SIII Ultra.
IMI Wins Gold Award for Best Managed Technology Company at FinanceAsia’s 29th Asia’s Best Companies Awards
07/01/2025 | IMIIntegrated Micro-Electronics Inc. (IMI) has been awarded the prestigious Gold Award for Best Managed Technology Company at the 29th edition of the Asia’s Best Companies Awards, hosted by FinanceAsia.