Achieving the Perfect Solder Joint: The Many Perspectives on Soldering
October 30, 2017 | Stephen Las Marias, I-Connect007Estimated reading time: 7 minutes
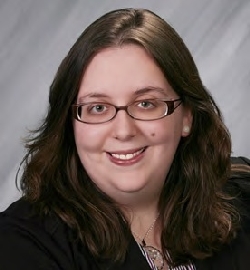
For this month's issue of SMT Magazine, I-Connect007’s editorial team brought several experts together for a teleconference call recently to discuss the many aspects of soldering, from solder paste, to automation, inspection, and the challenges in achieving the perfect solder joint.
In attendance were Indium Corporation’s Brook Sandy-Smith, technical support engineer; Metcal's Robert Roush, product support engineer; and from MC Assembly, Andrew Nunenkamp, director of engineering, and Vince Burns, quality engineer and an IPC Certified Trainer. We also talked about the strategies and parameters to consider to ensure reliable, good solder joints.
The Challenges
The first topic in the discussion is the challenge in achieving the perfect solder joint. When it comes to soldering and soldering materials, Sandy-Smith comments that the question she hears the most is regarding the type of flux that can be used to wet to unusual surfaces.
"Many times when people are soldering, they’re not just soldering to a PCB with a suitable surface finish. In these cases, we often get questions about soldering to unconventional surfaces. When people are doing regular SMT assembly, I frequently get questions about what to do if the components are oxidized or if the surface finish on the component is difficult to solder to."
Roush, on the other hand, says many of their customers are very concerned about process control and throughput, and the balance between the two. Customers want to make sure that they're getting as much product through at a reasonable rate, but that they also want to ensure that they’re minimizing scrap.
"They want to make sure that they're producing a quality product at the end. They're looking for guidance on training or advice on solder tip geometry selection and that type of thing. It really comes down to all the little process variables heading into forming that solder joint that we get the most questions for," says Roush. "There's just been such a trend in the industry for products to become denser, with more components in such a small amount of area that the boards and the thermal loads have just dramatically shifted over the years, and they’re looking for more performance to be able to give off thermal energy into the joint to form something strong and reliable in a reasonable time. We get many requests for trying to optimize the tip geometries or temperature selection or one of the other factors going into it to really improve that process. There’s only so much control they have over it. The tip geometry selection and solder, type of materials they’re soldering to, and then the training of the operator all goes into this big mix. In the end, they’re hoping that they’re getting a good solder joint. So that’s really what they’re looking for.
"Probably the second most asked about trend is traceability. There’s been a huge push in the last couple of years, especially among contract manufacturers (CM), to be able to provide traceability information to their customers for those solder joints. So, it’s really that next generation of how to collect this data and do something with it."
One of the soldering trends nowadays is the move towards automated hand soldering. So, is this a method for improving joints? Roush says with all the variables associated with just the idiosyncrasies of operators—variation on the skill and experience level—a robot levels that playing field.
"What you can’t replicate on a robot, at this point, is knowing when something is going wrong or there's an activity or a problem that crops up," he explains. "The robot is relatively dumb in that respect and it’s just going to do exactly what you program in it. If its conditions change, for example, there’s a bad batch of boards or there’s something wrong with a component that’s being put down, the robot won’t know any better and will just continue to execute the program. So, I don’t think they’re going to totally replace it, but I see it more of a complement and a way to increase throughput."
But on whether automated hand soldering provides a better solder joint, there are definitely tradeoffs, according to Roush.
"There's some fantastic operators out there that are like machines, and they do a fantastic job of soldering. But I think that the challenge with robotic soldering is that for 99% of what’s out there in the market, you have to program it on the safe side, and your tendency is to give it more time on the joints than may be necessary because you want to make sure that the joint is formed properly, because no one’s watching it. So, the time on joint may be four or five seconds and you only need it to be there three; that increases the amount of time it takes to produce the board, and you’re putting more thermal energy into the joint than you really need to, which can then impact IMC formation," says Roush.
One of the latest technologies from Metcal, the Connection Validation soldering station, provides operators with real-time, closed loop feedback to indicate intermetallic compound formation—the key to a good solder joint. With the CV, Roush says the power supplies are attached to a robot and have an application, and whether it’s a hand soldering or robotic soldering application, the feedback from the unit will basically indicate to the operator or to the robot to move on to the next joint as the IMC is formed. "So, there's no real danger there of staying on the joint too long or dwelling too long on a single joint," he says.
From a contract manufacturers' standpoint, MC Assembly's Nunenkamp says there are pros and cons for all product development using robotic soldering irons and hand soldering irons. "Lack of a one-size-fits-all solution is part of the challenge. What Robert was referencing is spot on from the idiosyncrasies of the impact of an operator to the robot," he explains. "I have certain scenarios that I cannot put on that robot because I don’t have the ability or the volume for it to be successful. I need to have trained solderers to successfully make those solder joints. We see volume-driven environments and Class 3 requirements are challenging robotics to be consistent, but then you have the visual validation factors as well or an automated system that can hopefully perform that inspection as well and meet IPC requirements. So, it’s all about the tooling, the fixturing and the alignment pieces that come with the robotics. We had a high-volume product that worked very well on the robot. Some of the variations that we run into though is if a no-clean solder is required, we have to change over requirements or needs for additional equipment then.
"So, in a contract manufacturer’s world, it really depends on the size of the customers' need and their design. We have other scenarios that we're looking at right now, for example, that require some very detailed soldering efforts that are very inconsistent when you put it on and depend on the people to do it. We could get some more consistency out of the robot once we get tooling in place and design of fixturing and supporting the components that you need in play. It is a significant investment to go that route. There are pros and cons in each direction and the application is really depending on that answer. So, if we’re building high-volume cellphones, you would have a different conversation, but if we’re building lower-mix, medium-mix or low-volume products to mid-volume products, then we have a little different approach to it."
From an assembler's point of view, the greatest challenge when it comes to solder joints is, according to Nunenkamp, is physically getting the IPC knowledge to the point of making the right judgment call on quality rather than personal preference. "The insufficient viewpoint, the non-wetting calls, the things that are considered defects in the world of IPC are getting that trained eye and knowledge instilled in the people that we need so that they can create the good solder joints and then can agree with the inspector’s eyes as well," Nunenkamp explains. "Obviously, driving inspections back to the operator that's making the joints is our preference so that we don’t double up our effort, but that’s really one of our largest challenges. Then, I think the other piece of the puzzle is getting them to use the tools that are made available and adequate for the job. The thermal energy that Robert talked about is one of those challenges that continues to be around, but you might use a pre-heater, you might use an alternate heating mechanism to get that thermal energy that you need in the actual product before you start soldering, or during the soldering operation as well. Their previous experiences can plague it a little bit right where they’ve never had to do this before or they’ve only done this in a leaded environment. We're now going to a lead-free environment with a couple other copper layers in the circuit board or a challenging thermal component, and really getting that innovation in the soldering development process versus the way they’ve always done it before is the challenge.
To read the full version of this article, which appeared in the October 2017 issue of SMT Magazine, click here.
Suggested Items
See TopLine’s Next Gen Braided Solder Column Technology at SPACE TECH EXPO 2025
05/28/2025 | TopLineAerospace and Defense applications in demanding environments have a solution now in TopLine’s Braided Solder Columns, which can withstand the rigors of deep space cold and cryogenic environments.
INEMI Interim Report: Interconnection Modeling and Simulation Results for Low-Temp Materials in First-Level Interconnect
05/30/2025 | iNEMIOne of the greatest challenges of integrating different types of silicon, memory, and other extended processing units (XPUs) in a single package is in attaching these various types of chips in a reliable way.
E-tronix Announces Upcoming Webinar with ELMOTEC: Optimizing Soldering Quality and Efficiency with Robotic Automation
05/30/2025 | E-tronixE-tronix, a Stromberg Company, is excited to host an informative webinar presented by Raphael Luchs, CEO of ELMOTEC, titled "Optimize Soldering Quality and Efficiency with Robotic Automation," taking place on Wednesday, June 4, 2025 at 12:00 PM CDT.
CE3S Launches EcoClaim Solutions to Simplify Recycling and Promote Sustainable Manufacturing
05/29/2025 | CE3SCumberland Electronics Strategic Supply Solutions (CE3S), your strategic sourcing, professional solutions and distribution partner, is proud to announce the official launch of EcoClaim™ Solutions, a comprehensive recycling program designed to make responsible disposal of materials easier, more efficient, and more accessible for manufacturers.
Indium to Feature Precision Gold-Based Die-Attach Preforms at IMS 2025
05/29/2025 | Indium CorporationIndium Corporation® will feature its high-reliability, gold-based precision die-attach preforms for critical laser and RF applications, as well as 5G communications, at the International Microwave Symposium, June 15-19, in San Francisco, CA.