-
- News
- Books
Featured Books
- pcb007 Magazine
Latest Issues
Current IssueThe Hole Truth: Via Integrity in an HDI World
From the drilled hole to registration across multiple sequential lamination cycles, to the quality of your copper plating, via reliability in an HDI world is becoming an ever-greater challenge. This month we look at “The Hole Truth,” from creating the “perfect” via to how you can assure via quality and reliability, the first time, every time.
In Pursuit of Perfection: Defect Reduction
For bare PCB board fabrication, defect reduction is a critical aspect of a company's bottom line profitability. In this issue, we examine how imaging, etching, and plating processes can provide information and insight into reducing defects and increasing yields.
Voices of the Industry
We take the pulse of the PCB industry by sharing insights from leading fabricators and suppliers in this month's issue. We've gathered their thoughts on the new U.S. administration, spending, the war in Ukraine, and their most pressing needs. It’s an eye-opening and enlightening look behind the curtain.
- Articles
- Columns
- Links
- Media kit
||| MENU - pcb007 Magazine
Planning a PCB: Signal Integrity and Controlled Impedance Considerations
November 3, 2017 | John (Josse) Steinar Johnsen, ELMATICAEstimated reading time: 2 minutes
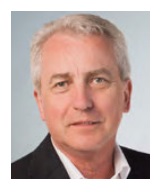
Editor’s note: We are pleased to introduce our newest column, which will be contributed each month by a team member from Elmatica.
Knowledge and experience are the two key elements when planning a PCB. Today’s PCB designers must have far more knowledge and understanding of the PCB production process than in the past. This is especially important when they plan and how they plan the stackup, via span, routing and power distribution.
This article will focus on multilayer boards since these are the types of PCBs where we truly see the importance of planning in the day-today PCB life. On a double-sided board, you can of course use one layer as a ground plane, but critical traces are not easy to handle.
As a designer, you know your needs when it comes to signal integrity, electromagnetic interference (EMI) design and impedance requirements. The factors involved are:
- Number of layers
- Number of power and ground planes used
- Sequence of layers
- Space between the layers
To continue, we can say that:
- Signal layers carrying critical signals, should always be adjacent to a plane
- Power and ground planes should be as close as possible for best capacitance
- Power and ground planes can use other material with a higher Dk, for best possible capacitance
- High-speed signals should be routed on innerlayers located between planes for best possible shielding
Multiple groundings will lower the reference plane’s impedance, and reduce the common mode radiation from the high-speed signals. The lowest layer-count you need to achieve all of this is probably an 8-layer board (Figure 1).
However, these points can be very challenging. There might be a maximum thickness of the PCB that cannot be ignored; many plane layers will limit the number of signal layers. It can be difficult to get the wanted signal impedances, regarding distance between layers, track widths and gaps between tracks.
Signal integrity addresses the degradation of signal quality to the point where an error occurs. EMI focuses on the corresponding specifications, test requirements and interference between nearby equipment. For signal integrity, the key factor is to keep noise levels significantly below signal levels. Our noise margins are typical in the millivolt range for digital circuits, but for EMI, emission levels must be kept in the microvolt and microamp range.
Ground impedance is at the root of virtually all signal integrity and EMI problems. To keep a low ground impedance is mandatory for both EMI and signal integrity. This is achieved with a solid ground plane. In fact, the main problem with ground impedance is the discontinuities that occur in the signal path, and it has a major impact on characteristic impedance control.
Copper thickness is not an important factor. At high bit rates, the skin effect dominates so the signal is pushed to the copper surface, which means that additional copper thickness is irrelevant.
These days, with more and more HDI designs operating well up in the GHz frequencies, characteristic impedance control becomes more important, but also more challenging to maintain, since distances between layers are shrunk. HDI and microvias require less distance between layers, and the fact that more layers will be squeezed within a given PCB thickness.
To read the full version of this article which appeared in the October 2017 issue of The PCB Magazine, click here.
Suggested Items
Copper Price Surge Raises Alarms for Electronics
07/15/2025 | Global Electronics Association Advocacy and Government Relations TeamThe copper market is experiencing major turbulence in the wake of U.S. President Donald Trump’s announcement of a 50% tariff on imported copper effective Aug. 1. Recent news reports, including from the New York Times, sent U.S. copper futures soaring to record highs, climbing nearly 13% in a single day as manufacturers braced for supply shocks and surging costs.
I-Connect007 Editor’s Choice: Five Must-Reads for the Week
07/11/2025 | Andy Shaughnessy, Design007 MagazineThis week, we have quite a variety of news items and articles for you. News continues to stream out of Washington, D.C., with tariffs rearing their controversial head again. Because these tariffs are targeted at overseas copper manufacturers, this news has a direct effect on our industry.I-Connect007 Editor’s Choice: Five Must-Reads for the Week
Digital Twin Concept in Copper Electroplating Process Performance
07/11/2025 | Aga Franczak, Robrecht Belis, Elsyca N.V.PCB manufacturing involves transforming a design into a physical board while meeting specific requirements. Understanding these design specifications is crucial, as they directly impact the PCB's fabrication process, performance, and yield rate. One key design specification is copper thieving—the addition of “dummy” pads across the surface that are plated along with the features designed on the outer layers. The purpose of the process is to provide a uniform distribution of copper across the outer layers to make the plating current density and plating in the holes more uniform.
Trump Copper Tariffs Spark Concern
07/10/2025 | I-Connect007 Editorial TeamPresident Donald Trump stated on July 8 that he plans to impose a 50% tariff on copper imports, sparking concern in a global industry whose output is critical to electric vehicles, military hardware, semiconductors, and a wide range of consumer goods. According to Yahoo Finance, copper futures climbed over 2% following tariff confirmation.
Happy’s Tech Talk #40: Factors in PTH Reliability—Hole Voids
07/09/2025 | Happy Holden -- Column: Happy’s Tech TalkWhen we consider via reliability, the major contributing factors are typically processing deviations. These can be subtle and not always visible. One particularly insightful column was by Mike Carano, “Causes of Plating Voids, Pre-electroless Copper,” where he outlined some of the possible causes of hole defects for both plated through-hole (PTH) and blind vias.