-
- News
- Books
Featured Books
- smt007 Magazine
Latest Issues
Current IssueWhat's Your Sweet Spot?
Are you in a niche that’s growing or shrinking? Is it time to reassess and refocus? We spotlight companies thriving by redefining or reinforcing their niche. What are their insights?
Moving Forward With Confidence
In this issue, we focus on sales and quoting, workforce training, new IPC leadership in the U.S. and Canada, the effects of tariffs, CFX standards, and much more—all designed to provide perspective as you move through the cloud bank of today's shifting economic market.
Intelligent Test and Inspection
Are you ready to explore the cutting-edge advancements shaping the electronics manufacturing industry? The May 2025 issue of SMT007 Magazine is packed with insights, innovations, and expert perspectives that you won’t want to miss.
- Articles
- Columns
- Links
- Media kit
||| MENU - smt007 Magazine
Dealing with Vias-in-Pad
November 8, 2017 | Stephen Las Marias, I-Connect007Estimated reading time: 4 minutes
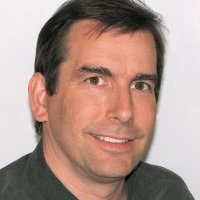
Screaming Circuits, a division of EMS firm Milwaukee Electronics, specializes in short-run, one-off, and prototype PCB assembly. For instance, if you need two or three prototypes and you need them in just a couple of days—that's what the company does. Or if you need 500 or 5,000 production boards, for example, if you had a Kickstarter and you sold 500 and you don’t know if you’ll sell any more—most manufacturing companies don’t want that business, but that’s where Screaming Circuits comes in.
It's all about small volumes, unforecastable, uncertain volumes, according to Duane Benson, chief technology officer and marketing manager of Screaming Circuits. "That gives us a very large set of experience because we see so many different jobs; we see virtually any kind of component tree applications that you might possibly imagine."
In another interview, Mike Creeden, vice president of layout services at sister company San Diego PCB Design LLC, said via-in-pad, even if it's a plated through-hole via, is a form of HDI.
With that in mind, I interviewed Benson about the challenges when dealing with microvias and vias-in-pads from an assembly standpoint, and how in-circuit test (ICT) issues, such as access to test points, can be addressed. Generally, Benson said there's not that much issue for the assemblers when it comes to microvias or HDI. However, he notes that no matter how small the vias are, especially in via-in-pad, they have to be plugged and filled at the fabricator side, must be plated over, and has to have a very planar surface.
"That's the biggest challenge with the high-density vias—making sure that they’re properly plugged and plated at the board house, and then that they leave a planar surface. If it's nice and flat like that, for assembly purposes, it doesn't matter—we don't really know that it's there really. Some people like to leave the microvias partially open—there would be a via open going from one layer to the next. With the tiny micro BGA, if you do that, you are going to end up with an air bubble inside the BGA ball, which might crack under stress, and it might not totally connect," said Benson. "Basically, the only thing for a super fine pitch BGAs and those types of vias, the only proper way to avoid assembly problems is to have them filled and plated at the board house, and leaving a flat, planar surface. That's really the only option. Between the pads, you have to make sure that there is a complete and total solder mask dam between the pad and the via."
If vias are open, there's this possibility of solder flowing into them during the reflow process. "You can end up with outgassing—flux that didn’t fully activate. It's just bad news," said Benson. "Really, with microvias, especially when it comes to BGA pads, you got to have them plugged and filled at the board house. You got to have a nice, flat, planar metal surface; there's really no other option for assembly with those tiny little parts. We would normally catch that before it goes to the board house. So, then we would go back to the designer, one of our manufacturing engineers would call them up, and let them know how to avoid that. If the via is in the pad, the two ways to avoid that are: (a) move it outside of the pad; or (b) connect with the board house and let them fill it and plate it over. We would give that advice to the designer."
Another issue with via-in-pads is the limited access for ICT. Screaming Circuits, however, typically doesn’t do these tests because it is just dealing with prototypes. "What our volume production facility, Milwaukee Electronics, a more-traditional EMS, typically would do is our engineers would go back to the designer. If the test program is needed, we will have to say, 'We can't test without a test point here.' Quite often, you will end up with a hybrid of either bed of nails or flying probe, and a functional test. You can detect a lot of problems with a functional test, even if the pads are underneath the BGAs or hidden. But not everything. You will end up with some test points added in and potentially use of software-based testing system," said Benson.
"In the prototype world, we make do with what we got. But when we are going to build hundreds or thousands, or tens of thousands of things, we will have to have our manufacturing engineers connected with the design engineers before those volume productions. Sometimes, what's going to happen is we’ll get a prototype, we’ll build it, and they will modify the design, then build it again, and then say, 'We're ready to go to volume production.' Then, we'll go through an additional NPI process. If we found that it can’t be tested, or it can’t be reliably built because of some of those issues, whether they are HDI related or not, we would give them guidance on where or how to modify the designs so that they will be reliable and testable."
Suggested Items
Magnalytix and Foresite to Host Technical Webinar on SIR Testing and Functional Reliability
06/26/2025 | MAGNALYTIXMagnalytix, in collaboration with Foresite Inc., is pleased to announce an upcoming one-hour Webinar Workshop titled “Comparing SIR IPC B-52 to Umpire 41 Functional & SIR Test Method.” This session will be held on July 24, 2025, and is open to professionals in electronics manufacturing, reliability engineering, and process development seeking insights into new testing standards for climatic reliability.
Defense Speak Interpreted: Is DARPA Still Around After CHIPS?
06/24/2025 | Dennis Fritz -- Column: Defense Speak InterpretedWhen I first published my Defense Speaks Interpreted column in January 2019 on the Defense Advanced Research Projects Agency (DARPA ERI), the agency advocated for an expanded Defense emphasis on closing the growing technology gap in microelectronics. The emphasis was on “resurgence.”
I-Connect007 Editor’s Choice: Five Must-Reads for the Week
06/13/2025 | Marcy LaRont, I-Connect007Today is Friday the 13th, and in much of Western folklore, this is a day when bad luck is lurking. But while Friday the 13th may top Western superstition charts, the global calendar is sprinkled with its own unlucky legends. In Spain and Greece, the bad juju lands on Tuesday the 13th—a day linked to Mars, the god of war, and naturally, chaos. In Italy, it’s Friday the 17th that is feared, thanks to the Roman numeral XVII, which can be rearranged to spell VIXI—Latin for “I have lived” (a poetic way of saying you’re dead).
TTCI Celebrates Melanie Rutkauskas’ 10-Year Anniversary and Her Leadership of New Training Division
06/12/2025 | TTCIThe Test Connection Inc. (TTCI), a leading provider of electronic test and manufacturing solutions, is proud to celebrate Melanie Rutkauskas on her 10-year anniversary with the company.
Bridging the Knowledge Gap in Test: A Conversation with Bert Horner
06/11/2025 | Barry Matties, I-Connect007Bert Horner is a seasoned industry veteran and co-creator of The Test Connection, Inc. (TTCI), a test and inspection company spanning over 45 years. In this candid conversation, Bert reflects on the challenges our industry faces with the retirement of career professionals and the subsequent loss of critical tribal knowledge. As he unveils The Training Connection’s innovative training initiatives, Bert emphasizes the importance of evolving educational programs that align with industry needs, particularly in design for test (DFT), and sheds light on strategies being implemented to foster the next generation of engineers.