-
- News
- Books
Featured Books
- pcb007 Magazine
Latest Issues
Current IssueThe Hole Truth: Via Integrity in an HDI World
From the drilled hole to registration across multiple sequential lamination cycles, to the quality of your copper plating, via reliability in an HDI world is becoming an ever-greater challenge. This month we look at “The Hole Truth,” from creating the “perfect” via to how you can assure via quality and reliability, the first time, every time.
In Pursuit of Perfection: Defect Reduction
For bare PCB board fabrication, defect reduction is a critical aspect of a company's bottom line profitability. In this issue, we examine how imaging, etching, and plating processes can provide information and insight into reducing defects and increasing yields.
Voices of the Industry
We take the pulse of the PCB industry by sharing insights from leading fabricators and suppliers in this month's issue. We've gathered their thoughts on the new U.S. administration, spending, the war in Ukraine, and their most pressing needs. It’s an eye-opening and enlightening look behind the curtain.
- Articles
- Columns
- Links
- Media kit
||| MENU - pcb007 Magazine
Groundbreaking Developments at liloTree
November 9, 2017 | Patty Goldman, I-Connect007Estimated reading time: 9 minutes
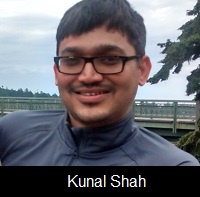
I was introduced to liloTree and Chief Scientist Kunal Shah by Joe Fjelstad. It seems this small company (with Intel as part of its pedigree) has developed a novel ENIG process that just may shake up the regular chemistry suppliers. This new process is described as cost-effective and ecofriendly while completely eliminating black pad and brittle solder joints.
Patty Goldman: Kunal, let’s start with a little about yourself and your company.
Kunal Shah: Thanks for this opportunity. I have a PhD in material science and engineering from the University of Florida. I was hired by Intel as a senior research scientist, working in R&D developing materials and chemistries and things of that sort. I was a key person as we developed polymer interlayer dielectric and passivation material. Since 2008, all IC products from Intel have had integrated polymer passivation material. Then I had a brief tenure at Pacific Northwest National Lab working on a Department of Homeland Security project for identifying semiconductor materials for radiation detection. From there, I moved to Seattle and we started liloTree. At liloTree, we do two things. One is product improvement. We work with some aviation-aerospace companies because we are in Seattle.
When their products fail, they come to us and we do scientific analysis and evaluation all the way to the materials level to identify the root cause of their failure. Then we just don’t tell them, “Hey, this is why it failed.” We go beyond that, “Here’s what you need to do so these problems don’t happen again.” The product improvement solutions and that recommendation led us towards our other focus on ENIG. We had many aviation aerospace companies keep coming back to us, with the failures and the root causes, more or less black pad-related failure due to the electroless nickel/immersion gold process. We’d tell them, “It’s a black pad-related issue that you are facing,” and because these companies’ applications are critical they could not afford to have repeating failures. Then we had medical electronics also come to us with similar problems and we realized there was no solution out there.
It then became apparent from our side that there is a need in the market because even if we are giving them solutions, it’s not a complete solution. It’s not understood well by the manufacturers, first. It is very technical and scientific, and they’ve not addressed that issue, which is a root cause of black pads. We decided there was an opportunity to develop a product ourselves. First, we wanted to fundamentally understand why black pads were happening, then develop a technology to mitigate them, so that they never happen with our product. We named it ENIG-Premium and developed it from the ground up.
Almost all ENIG on the market uses cyanide-based gold chemistry, which can be considered environmentally hazardous as well as potentially hazardous to facility personnel. We developed a cyanide-free chemistry for the gold solution as part of our value proposition, which is good for both PCB and component manufacturers.
As we did market research, we realized there was another major issue associated with ENIG:the brittle solder joint. We learned this from talking to the real customers, the OEMs. When solder is being reflowed onto ENIG, especially when the solder is lead-free, that intermetallic or solder joint is very, very brittle.
Our paper to be presented at IPC APEX EXPO 2018 will have all the details of why ENIG and lead-free solder has more brittle failures than its counterpart, leaded solder. We know that the entire industry is going towards lead-free technology. That is a major concern for products, for applications or for OEMs who are using ENIG surface finish with lead-free.
When we were developing ENIG-Premium, our first goal was to of course make it black-pad-proof or completely corrosion-resistant. Our second goal was to design our chemistry, especially the cyanide-free gold chemistry, to be ecofriendly. Third, and most important, was to design the ENIG-Premium in such a way that when it forms an intermetallic, with either lead-based technology or lead-free technology, it is so robust that failures do not happen at the intermetallic itself.
We wrote a technical proposal to the National Science Foundation, Small Business Innovation Research Grant (SBIR). We were awarded a phase-one grant for a novel ENIG. We etched out some of the finer details and fully developed that product during that phase
Then we did a whole lot of market research and talked to as many as 50−70 different PCB manufacturers and component manufacturers who are the actual end-customers of the ENIG. They applied it to their PCB or components as ENIG surface finish. We talked to them to understand what concerns they were facing, what challenges they were facing. We built up that knowledge base as we developed this product.
We were awarded phase two because we successfully demonstrated that product very effectively and very successfully as well as all the market research and responses that we received.
It’s the financial support that is great. Along with that, we believe that it added so much credibility to the type of work that we are doing and the type of product that we have developed because just their review process was six months, with two committees. One was commercial viability, and another on technical viability and technical proof of concepts and how technically strong and robust the technology is.
Now we are all ready for ENIG-Premium to fast scale commercialization. We are appearing at IPC APEX EXPO early next year and doing all the business development and everything just to get the word out and market this product and get to all the PCB manufacturers locally in United States as well as outside of the United States.
Goldman: Have you worked with any PCB facilities or manufacturers yet?
Shah: Several PCB manufacturers are in different stages of testing. One of the largest flex PCB manufacturers in the world has gone through three rounds of testing of ENIG-Premium and they are happy. They are just making sure of the logistics and then plan to install it in their multiple factories in China as well as in the U.S. Then there are several smaller-scale companies who have adopted ENIG-Premium in a variety of levels. They are realizing the benefits and they are slowly and steadily adopting it to all their facilities and operating lines.
Goldman: So, this is in production, correct?
Shah: Yes, absolutely. We’ve done a lot of scientific testing in-house. Just to give you an idea, when we tested ENIG-Premium versus a conventional ENIG, we have 10 times more corrosion resistance compared to the conventional ENIG. That is a benefit. There is no way black pads can happen. One of the reasons is because we do interfacial engineering between nickel and gold surfaces. Once the electroless nickel phosphorous layer is applied, we do interfacial engineering onto that surface before the gold is applied. When the solder is applied, that phosphorous-rich area does not wet well with the solder joint. You have spots of areas where it’s not wetting well, and then other areas where it’s wetting well. You have pockets or voids, which are microscopically small. It is basically the phosphorous-rich area that shows up black, hence the name, black pad.
If you have complete non-wetting, that is a complete failure right there. Sometimes it is a partial wetting and partial non-wetting, which is even more dangerous because when it goes into the application, you will start seeing failures because some mechanical stress or vibration is applied and you’ll have a complete failure. What we have done is completely passivated the nickel layer left behind. It becomes extremely corrosion resistant when the gold layer is applied. That’s why you won’t find a phosphorous-rich area and you’ll have a very strong gold layer on top, attached to the nickel layer underneath.
Also, one of the things we have done for the same principle was applied when the intermetallics were formed, because in conventional ENIG, you have a phosphorous-rich area that makes a phase called Ni3p. In general, it is nickel 9, p10, which is a 90:10 ratio if we go by regular 90% nickel and 10% phosphorous. Electroless nickel deposits are typically around 90% nickel and 10% phosphorous, with some variation in phosphorous content depending on the supplier.
Because the nickel has been exchanged in the immersion gold process along with high diffusion of nickel into solder during the reflow process, the localized region (at the intermetallics towards Ni-P side) forms a phase called Ni3P. That phase is very soft and has sub-micron-size voids in it which makes it prone to brittle failures. Wherever the stress is applied, the failure invariably happens in that phase because of the minute voids that are present. That’s why conventional ENIG solder joints usually see brittle failures.
Our technology has resulted in two things. First, because of our interfacial engineering, you don’t see phosphorous rich areas. In a conventional ENIG, when the soldering is done at 260°C, too much nickel diffuses into the solder joint. Your intermetallic area is significantly thicker on the order of several microns. But we can limit or reduce that phosphorous rich area significantly.
Secondly, because of the interfacial engineering, during the soldering/reflow process the nickel does not diffuse too much into the solder. The intermetallic is very thin and compact, as small as few microns, so you will have the negligible Ni3p phase, so it is very robust.
We had a NASA-approved third-party lab in California do testing on our intermetallics and solder joints. We had a solder prepared using conventional ENIG and a solder prepared using ENIG-Premium on the printed circuit board and sent those samples to the lab in California. They were able to do industry-based standards, including JEDEC, which is somewhat affiliated with IPC. They did JEDEC standard-based ball shear test and ball pull test on solder joints.
Goldman: I know a new standard has just come out, a new spec limiting the amount of gold that goes on. Then there was a whole issue about how you measure that gold thickness because a lot of the equipment can’t measure it accurately.
Shah: We are very much aware of that. And one of the benefits of the interfacial engineering is we can control the gold thickness. We’re able to consistently produce our ENIG plating with exactly 50 nanometers of gold. With conventional ENIG, most PCB manufacturers cannot easily control the thickness of gold and they end up putting 100 to maybe 150 nanometers of gold. Too much gold can lead to potential gold embrittlement. In this discussion of technical benefits, our ENIG-Premium is very cost equivalent to conventional ENIG.
Goldman: Well, that’s quite the product then. Have you worked out a network of technical service for your customers? How do you expect to service this?
Shah: That is a great question. As I mentioned, liloTree has two business models. One is the product improvement solution where our expertise lies in identifying the failures and providing the solution. I think that is our main core competency. When it goes out to anywhere in United States or outside, we have a technical lab with all the scientific instruments like scanning electron microscopes, elemental analysis using EDS, thickness measurement using XRF, and molecular analysis using FTIR. We have assigned a team of scientists who continuously support those kinds of activities. We can use it as soon as any customer has any problem or faces any issues.
Goldman: Well, that’s very good. I guess we’ll learn more at the IPC conference in San Diego.
Shah: Absolutely.
Suggested Items
Knocking Down the Bone Pile: Addressing End-of-life Component Solderability Issues, Part 4
07/15/2025 | Nash Bell -- Column: Knocking Down the Bone PileIn 1983, the Department of Defense identified that over 40% of military electronic system failures in the field were electrical, with approximately 50% attributed to poor solder connections. Investigations revealed that plated finishes, typically nickel or tin, were porous and non-intermetallic.
SHENMAO Strengthens Semiconductor Capabilities with Acquisition of PMTC
07/10/2025 | SHENMAOSHENMAO America, Inc. has announced the acquisition of Profound Material Technology Co., Ltd. (PMTC), a premier Taiwan-based manufacturer of high-performance solder balls for semiconductor packaging.
KYZEN to Highlight Understencil and PCB Cleaners at SMTA Querétaro Expo and Tech Forum
07/09/2025 | KYZEN'KYZEN, the global leader in innovative environmentally responsible cleaning chemistries, will exhibit at the SMTA Querétaro Expo & Tech Forum, scheduled to take place Thursday, July 24, at Centro de Congresos y Teatro Metropolitano de Querétaro.
Driving Innovation: Direct Imaging vs. Conventional Exposure
07/01/2025 | Simon Khesin -- Column: Driving InnovationMy first camera used Kodak film. I even experimented with developing photos in the bathroom, though I usually dropped the film off at a Kodak center and received the prints two weeks later, only to discover that some images were out of focus or poorly framed. Today, every smartphone contains a high-quality camera capable of producing stunning images instantly.
Hands-On Demos Now Available for Apollo Seiko’s EF and AF Selective Soldering Lines
06/30/2025 | Apollo SeikoApollo Seiko, a leading innovator in soldering technology, is excited to spotlight its expanded lineup of EF and AF Series Selective Soldering Systems, now available for live demonstrations in its newly dedicated demo room.