(Not) Breaking the Barrier to Foldable OLED Displays
November 16, 2017 | Holst CentreEstimated reading time: 2 minutes
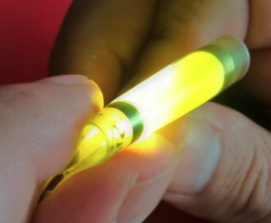
With today's smartphones, tablets and laptops, there always seems to be a compromise: do you choose a bigger display for a better experience or a smaller, more portable device? But what if you could have both: displays the size of newspapers that fold up to fit in your pocket. Researchers from Holst Centre have solved a major challenge in creating such large-area displays for portable devices, demonstrating a new protective barrier for organic electronics that is foldable and allows high-temperature processing of display backplanes on top.
OLEDs are extremely sensitive to humidity, and the flexible substrates needed for foldable displays don't provide enough protection against moisture. So flexible displays need moisture-proof protective barrier layers above and below the sensitive OLED materials. However, the materials used in these barriers are quite brittle, limiting how much resulting displays can be bent and hampering the development of foldable displays.
Holst Centre's new optimized barrier makes foldable displays possible. It comprises an organic layer sandwiched between two layers of silicon nitride (SiN) – a standard barrier layer material. By optimizing the design of this stack, Holst Centre's scientists have been able to control its mechanical properties and create a much more flexible barrier that ensures the neutral stress line during bending is close to the active layers of the display to prevent mechanical and electrical degradation. The organic material also helps prevent moisture penetration through pinholes by ensuring very slow lateral spreading of water between the SiN layers.
Crucially, the particular organic material used is stable up to 400 °C and can be applied by slot-die coating. This allows the SiN layers to be deposited at 350 °C, improving their quality and ability to prevent water penetration. Moreover, it means the barrier can withstand the high temperatures used in display production processes, making it suitable for the bottom protective layers.
"Foldable displays are a hot topic right now, with many people claiming to demonstrate them. But the term is applied quite loosely, and very few – if any – of these demonstrators achieve the bending radii of 2 mm or less needed to be truly foldable. Our optimized multilayer barrier now makes foldable OLED displays possible. Not only does it enable very small bending radii, it is compatible with standard display production processes and provides excellent protection against water and stress for long-lasting displays," said Hylke Akkerman, Program Manager at Holst Centre.
OLED demonstrators using the new barrier have achieved 1000 hours with no blackspots in accelerated lifetime testing, even after ten thousand cycles of folding with a bending radius of 0.5 mm. This represents an operational lifetime of several years. With earlier versions of the barrier already deployed in its own Gen 1 pilot production line, Holst Centre is currently transferring this latest barrier to a production at a partner's facility.
Suggested Items
MVTec Presents Advantages of Machine Vision for Battery Production
05/16/2025 | MVTecMVTec Software GmbH, a leading international manufacturer of machine vision software, will once again demonstrate the added value of machine vision for battery production at this year's Battery Show Europe in Stuttgart.
Interlink Electronics Reports Q1 2025 Result
05/15/2025 | BUSINESS WIREInterlink Electronics, Inc., a global leader in sensor technology and printed electronic solutions, reported results for the first quarter ended March 31, 2025.
Japan’s Sharp to Sell LCD Plant to Taiwanese Parent Company Foxconn
05/14/2025 | I-Connect007Japanese electronics firm Sharp Corp. announced on May 12 that it plans to sell its Kameyama No. 2 liquid crystal display plant to its Taiwanese parent company, Foxconn.
Breaking Down Barriers: The Connectivity of Machines in SMT Production Lines
05/14/2025 | Bill Cardoso, Creative ElectronAs the world increasingly moves toward erecting trade barriers, we find ourselves in a paradox. Across the globe, the rise in tariffs and protectionist policies is creating a more fragmented global economy, with nations seeking to insulate themselves from external economic pressures. However, within the confines of the SMT production line, the trend is moving in precisely the opposite direction—toward greater connectivity, integration, and collaboration. Rather than isolating one machine from another, SMT production lines are increasingly interconnected, with data being shared across various stages of the process to improve quality, efficiency, and defect detection.
Vertical Aerospace, Honeywell Expand Partnership to Bring VX4 eVTOL to Market
05/13/2025 | HoneywellVertical Aerospace and Honeywell announced the signing of a new long-term agreement that expands their existing partnership and reinforces Honeywell’s commitment to the certification and production of Vertical’s electric vertical take-off and landing (eVTOL) aircraft, the VX4.