-
- News
- Books
Featured Books
- smt007 Magazine
Latest Issues
Current IssueWhat's Your Sweet Spot?
Are you in a niche that’s growing or shrinking? Is it time to reassess and refocus? We spotlight companies thriving by redefining or reinforcing their niche. What are their insights?
Moving Forward With Confidence
In this issue, we focus on sales and quoting, workforce training, new IPC leadership in the U.S. and Canada, the effects of tariffs, CFX standards, and much more—all designed to provide perspective as you move through the cloud bank of today's shifting economic market.
Intelligent Test and Inspection
Are you ready to explore the cutting-edge advancements shaping the electronics manufacturing industry? The May 2025 issue of SMT007 Magazine is packed with insights, innovations, and expert perspectives that you won’t want to miss.
- Articles
- Columns
- Links
- Media kit
||| MENU - smt007 Magazine
Configure to Order: Different by Design
January 9, 2018 | Michael Ford, Aegis Software Corp.Estimated reading time: 11 minutes
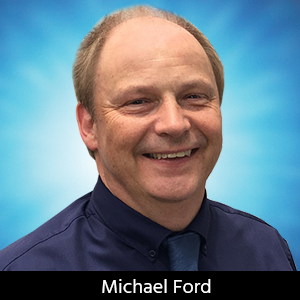
Perhaps in the future, sentient robots looking back at humans today will consider that we were a somewhat random bunch of people as no two of us are the same. Human actions and choices cannot be predicted reliably, worse even than the weather. As with any team however, our ability to rationalize in many different ways in parallel is, in fact, our strength, creating a kind of biological “fuzzy logic.” Robots will have to cope with mankind’s wishes for differentiation, no matter how illogical that may be. Rather than repetitive automation, the Industry 4.0 computerization concept has been created to find efficiency in automated randomness. The crux of such a process is the ability to be prepared for, and to be able to manage, the increasing mix of products and their variants effectively, just as smoothly as if factories were producing in high volume. When considering Industry 4.0 therefore, being able to digitally configure to order (CTO), rather than having to be responsible for hundreds or thousands of individual bill of materials (BOMs), in a simple and effective way is an essential, critical business need.
Automation has been a key element since the start of the third industrial revolution, where electrical systems and controllers have been running machinery designed to replace human manual dexterity. Until quite recently, automation has been rather dumb. Simple automation was dominant where machines simply followed a set of sequential instructions, or, in the case of assembly robots, copied a series of movements. More evolved automation can apply alterations and corrections based on, for example, the processing of visual checks on SMT machines, which correct the position and orientation of materials picked up or positioned for placement. The challenge for the creation of the vast majority of automated processes was made very much easier by the notion of mass production, where once set up, the automation would simply repeat what it was doing in a very efficient way, with very high equipment utilization. Unfortunately, the heyday of repetitive high-volume manufacturing for most of us has passed.
It seems ironic that automation has played the initial part in the downfall of mass-production itself. Adopting automation meant that the quantity of products made could be increased drastically over manual production lines. This meant that the market for such products expanded. Requirements in expanded markets meant that there needed to be different versions made, for example with different electricity or communication standards, including of course human language. The concept of variants was born. Once established, marketing teams got involved, using variants to find ways of targeting against competitor’s products, making lower cost versions, higher featured versions. Any company could then target increasingly well-defined niches of customer need with exactly the right cost-effective product.
After marketing, came fashion. Technology has become fashionable, creating the need, for example, in personal devices such as cellphones, to be available in many different sizes, colors and styles. Perhaps as an extreme example, but genuine nonetheless, a specific original design of mobile phone is now manufactured with thousands of individual variants, depending on feature level, resource level, wireless options, software options, language, service provider, colors, etc. Keeping track of which phone is which during manufacturing is an absolute nightmare. Most of the variants look the same throughout most of the processes, but have different assembly combinations, including subtle differences in electronic component placement positioning. The worst aspect of this is yet to come.
Figure 1: Knowing what is currently executing and the status of each process in the factory provides critical information for Industry 4.0 computerized management systems.
Since there are so many variants, the cost of storage of semi-complete and completed products has increased in line with the number of variants being produced. In most cases, the business demand has been to avoid stock of products as far as possible. The number of days of stock throughout the distribution chain has typically shrunk from being many months, to a few days at most. For manufacturing operations that are remote from their markets, such as China, the reduction can only be achieved by air-freight rather than sea-freight, increasing distribution costs and environmental impact. Companies that manufacture close to their markets, typically those remaining in the West, are pushed to be almost “make to order” so as to keep needless investment of stock to an absolute minimum. In-factory warehousing is included. The opportunity for manufacturing to smooth the effect of high product mix on the lines by creating stockpiles in the warehouse is rapidly running out. The reality now must be faced. Manufacturing must be capable of producing multiple configurations with complete control and without any loss of productivity. Those companies that can achieve this are surely the companies that will succeed, having reduced the extortionate operational overhead of mixed and low-volume production to an absolute minimum. This is the condition that Industry 4.0 achieves through the use of computerization.
When considering implementation of Industry 4.0 solutions, following the hype in the market, attention typically is focused on the need for communication between machines on the shop-floor. Knowing what is currently executing and the status of each process in the factory, as well as all the related resources and support operations, provides critical information for Industry 4.0 computerized management systems. This includes work-order creation and assignment, as well as the control and planning of related resources and support operations. What is often neglected however until much later in the process, is the management and control of the engineering definitions of products and related variants that are to be made in this ultra-flexible factory. Engineering control is quite a challenge considering the many tens, hundreds or indeed thousands of products and variants that can potentially be live in production in a single factory at any time. The management of the precise engineering data, which includes visual aids and documentation, to be supplied to all processes exactly when needed can quickly become an extreme drain on engineering resource. Add to this the need for conformance, where every set of engineering data, whether comprising a set of machine instructions, or an ISO controlled operation standard for a manual process, needs to be issued and confirmed into place prior to specific execution of a work-order.
Apart from the number of different products and their variants, managing the many sets of BOMs on an individual variant basis is made more difficult where the differences between each variant can be quite small, but critical. Many of the differences will be at the end of the production process, for example the casing, manual, or packaging which is different. Of course, making a mistake here carries the same level of importance as anywhere else, as no-one wants to get a product with the wrong manual or power adaptor, or worse, with the wrong version of software. Small differences earlier in the manufacturing process, such as those in SMT production may make no discernable visual difference, but can affect many of the tests and processes that come later, as measurements and inspections may show up different results. Any level of confusion about what is supposed to be there and what is not, is simply not an option in manufacturing. The management of individual variant BOMs therefore requires a very thorough team of engineers.
Page 1 of 2
Suggested Items
EU Defence Electronics Ecosystem Highlighted in Brussels
07/01/2025 | I-Connect007 Editorial TeamIn this interview, Alison James, senior director of Global Electronics Association—Europe (formerly IPC), discusses the European Defence & Security Summit in Brussels, June 9–13, as well as the first IPC–ASD Europe Defense Electronics Summit, June 16, which brought together 70 leaders from across the electronics manufacturing supply chain. ASD is the Aerospace, Security and Defence Industries Association of Europe, and co-hosted both the larger and smaller events.
Europlacer Expands U.S. Reach with New Eastern Region Representative
06/30/2025 | EuroplacerEuroplacer, a global leader in flexible SMT assembly solutions for High-Mix manufacturers, is pleased to announce the appointment of Photo Chemical Systems as its new representative for the Eastern United States.
PCBA Market to Reach $147.5 Billion by 2035, Growing at a CAGR of 4.7% from 2025
06/27/2025 | PRNewswireThe Printed Circuit Board Assembly market is projected to reach $147.5 billion by 2035, up from an estimated $90.91 billion in 2025, growing at a steady CAGR of 4.7% during the forecast period.
Indium Corporation Expert to Present on Automotive and Industrial Solder Bonding Solutions at Global Electronics Association Workshop
06/26/2025 | IndiumIndium Corporation Principal Engineer, Advanced Materials, Andy Mackie, Ph.D., MSc, will deliver a technical presentation on innovative solder bonding solutions for automotive and industrial applications at the Global Electronics A
Fresh PCB Concepts: Assembly Challenges with Micro Components and Standard Solder Mask Practices
06/26/2025 | Team NCAB -- Column: Fresh PCB ConceptsMicro components have redefined what is possible in PCB design. With package sizes like 01005 and 0201 becoming more common in high-density layouts, designers are now expected to pack more performance into smaller spaces than ever before. While these advancements support miniaturization and functionality, they introduce new assembly challenges, particularly with traditional solder mask and legend application processes.