-
- News
- Books
Featured Books
- smt007 Magazine
Latest Issues
Current IssueWhat's Your Sweet Spot?
Are you in a niche that’s growing or shrinking? Is it time to reassess and refocus? We spotlight companies thriving by redefining or reinforcing their niche. What are their insights?
Moving Forward With Confidence
In this issue, we focus on sales and quoting, workforce training, new IPC leadership in the U.S. and Canada, the effects of tariffs, CFX standards, and much more—all designed to provide perspective as you move through the cloud bank of today's shifting economic market.
Intelligent Test and Inspection
Are you ready to explore the cutting-edge advancements shaping the electronics manufacturing industry? The May 2025 issue of SMT007 Magazine is packed with insights, innovations, and expert perspectives that you won’t want to miss.
- Articles
- Columns
- Links
- Media kit
||| MENU - smt007 Magazine
The Importance of Product Testing for Quality, Reliability and Durability
January 17, 2018 | Patty Rasmussen, East West ManufacturingEstimated reading time: 3 minutes
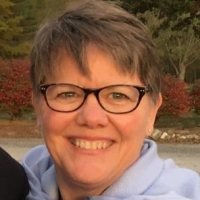
Product development takes time, creativity, resources, and more time. One really vital piece of the development process is product testing for quality, reliability and durability. You need to find out whether your product will do what it's supposed to do—that's quality. You also need to learn whether it will do what it's supposed to do over and over again, even when conditions aren't ideal—that's reliability and durability.
Product Testing
Some products, like Class III medical devices, require something called "Premarket approval" (PMA), the process of scientific and regulatory review administered by the Food and Drug Administration (FDA) to evaluate safety and effectiveness. Class III devices are those that support or sustain human life, are of substantial importance in preventing impairment of human health, or which present a potential, unreasonable risk of illness or injury.
But what about products that don't require FDA tests or approvals? Where do you go and what do you do when you're looking for solid, third-party validation to back up the claims you're making about your product?
Step one: Google. Seriously. Get online and start researching. Talk to people in your industry. Find out which product testing labs other folks are using.
Product testing is something that may be done either in-house (you or your manufacturer do the tests) or it's outsourced to an independent product testing agency. As much as you might think you want to be in control of the product testing, trust us: there are good reasons to outsource testing—chiefly cost. Maintaining a testing lab is expensive. It requires dedicated space, equipment (which must be maintained and repaired), upgrades, labor, training and certifications.
Types of testing include quality assurance, product reliability and lifecycle testing.
Testing is usually done during the development and manufacturing phases of product development. The outcome criteria are based on realistic expectations of customer use. Questions you need to ask include:
- How will this part or product be used?
- What sorts of pressures does it need to withstand - thermal, weight, etc.?
- How long should this product last?
The components that make up the product are selected based on the answers to the customer use profile. Perhaps the electronics or the raw material needs to be a certain grade or quality. Those items will be taken into account. Let's say you're making a medical device, for example. Components in medical devices must meet a higher standard than those going into a non-medical consumer electronics product.
During the manufacturing process, it's part of the quality process to test a product's functionality off the line. The quantity of items tested is determined in advance. It's also wise to test your product at the system level as the components are only as good as the sum of all the parts working together. Determine what the end results should look like and design the test(s) to rigorously examine how well the product/part performs.
Unlike quality testing, the purpose of which is to find defects early in the product development process, the main reason for reliability testing is to measure performance and endurance over the long haul—preferably in similar operational environments. When looking at the reliability of a group of products over a lifetime, you might hear experts describe something called the "bathtub curve."
The bathtub curve shows the decreasing failure rate during the early "infant mortality" days of the product, leading to the normal (a.k.a. useful) life of a product population and, finally, the onset of the end of life wear-out.
Stress testing from the earliest product development phase is meant to find design weaknesses and specific assembly and material problems. Highly Accelerated Life Testing (HALT) and Highly Accelerated Stress Test (HAST) introduce the types of real life problems a product may encounter during its lifecycle, without waiting the life of the product. For example, if corrosion could occur during the life of the product, the test would introduce corrosive material (salt water, for example) to the part/product to see if or how much the performance is affected.
Reliability testing is done for three specific reasons:
- To examine a product's endurance under certain conditions.
- To identify the failure rates of the product.
- If possible, to determine preventative measures that can increase the product's reliability and lifespan.
Typically, reliability testing will examine five areas:
- Vibration
- Temperature and humidity
- Time duration
- Number of test cycles
- Duration
To know more about building your own product reliability testing process, read the article titled What Is Reliability Testing by Jit Gupta of test, inspection, and certification company NTS.
This article originally appeared on the East West Manufacturing blog, which can be found here.
Suggested Items
Magnalytix and Foresite to Host Technical Webinar on SIR Testing and Functional Reliability
06/26/2025 | MAGNALYTIXMagnalytix, in collaboration with Foresite Inc., is pleased to announce an upcoming one-hour Webinar Workshop titled “Comparing SIR IPC B-52 to Umpire 41 Functional & SIR Test Method.” This session will be held on July 24, 2025, and is open to professionals in electronics manufacturing, reliability engineering, and process development seeking insights into new testing standards for climatic reliability.
Bridging the Knowledge Gap in Test: A Conversation with Bert Horner
06/11/2025 | Barry Matties, I-Connect007Bert Horner is a seasoned industry veteran and co-creator of The Test Connection, Inc. (TTCI), a test and inspection company spanning over 45 years. In this candid conversation, Bert reflects on the challenges our industry faces with the retirement of career professionals and the subsequent loss of critical tribal knowledge. As he unveils The Training Connection’s innovative training initiatives, Bert emphasizes the importance of evolving educational programs that align with industry needs, particularly in design for test (DFT), and sheds light on strategies being implemented to foster the next generation of engineers.
IPC Hall of Fame Spotlight Series: Highlighting Bob Neves
06/11/2025 | Dan Feinberg, I-Connect007Many IPC members who have contributed significantly to IPC and our industry have been awarded the IPC Raymond E. Pritchard Hall of Fame (HOF) Award. This Hall of Fame spotlight features industry veteran Bob Neves, who joined IPC in 1986 and was inducted into the IPC Hall of Fame in 2007.
GEN3 Set to Host HATS²™ Technical Day at A.W. Technical Centre with Bob Neves
06/09/2025 | Gen3GEN3, a global leader in reliability testing and measurement solutions for the electronics industry, is excited to announce a dedicated HATS²™ Technical Day to be held at the A.W. Technical Centre in Farnborough, GEN3’s HQ. The event will showcase the HATS²™ (Highly Accelerated Thermal Shock) system with demos and presentations by Bob Neves, Chairman of RAS Inc. and creator of the HATS²™.
Rohde & Schwarz Satellite Industry Day 2025: Connecting the World with New Space and 5G NTN Technologies
05/27/2025 | Rohde & SchwarzAfter four successful online events with over 1000 participants, Rohde & Schwarz is hosting its fifth Satellite Industry Day on June 3, 2025, on-site at its Munich campus. Rohde & Schwarz test and measurement experts and partners from the industry will present topics from 5G Non-Terresterial Network (NTN) and satellite testing to monitoring and regulatory issues. During breaks participants can experience cutting-edge test and measurement solutions.