-
- News
- Books
Featured Books
- smt007 Magazine
Latest Issues
Current IssueWhat's Your Sweet Spot?
Are you in a niche that’s growing or shrinking? Is it time to reassess and refocus? We spotlight companies thriving by redefining or reinforcing their niche. What are their insights?
Moving Forward With Confidence
In this issue, we focus on sales and quoting, workforce training, new IPC leadership in the U.S. and Canada, the effects of tariffs, CFX standards, and much more—all designed to provide perspective as you move through the cloud bank of today's shifting economic market.
Intelligent Test and Inspection
Are you ready to explore the cutting-edge advancements shaping the electronics manufacturing industry? The May 2025 issue of SMT007 Magazine is packed with insights, innovations, and expert perspectives that you won’t want to miss.
- Articles
- Columns
- Links
- Media kit
||| MENU - smt007 Magazine
7 Simple Ways to Motivate Your Electronics Manufacturing Staff
January 18, 2018 | Neil Sharp, JJS ManufacturingEstimated reading time: 5 minutes
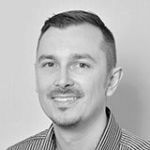
Your manufacturing staff are the backbone of your electronics manufacturing organization. They are the ones showing up day in, day out to build products for your customers. So, keeping them motivated and engaged should be a priority, right?
But too often during peak production periods, surmounting pressure can lead to staff feeling overworked, demoralized, and underappreciated.
Do you have systems in place to identify when employees are struggling, and to find suitable solutions to problems? Are you keeping staff updated on progress at these challenging times, and rewarding their hard work? Are you giving them a voice to raise ideas for improvements?
If you're serious about improving the engagement of your electronics manufacturing staff, read on for seven ways to boost staff morale and maintain calm during peak production times.
Set Standardized Processes
Start with the basics—make sure you have standardized processes in place. As with any task, it’s much easier to find motivation if you know exactly what you’re doing. And clear, standardized processes create momentum.
Communicate Effectively
Communicate openly with staff on company goals and progress. Share KPIs and keep everyone up to date with the results. Being left out of the loop is one of the most common causes of staff dissatisfaction. Your employees need to feel motivated to achieve company goals. But if they don’t know what those goals are…?
During peak periods when everything gets a lot busier, make sure staff are kept abreast of any new information and given a heads up on upcoming workloads. The more prepared they are, the less of a hurdle it will feel.
Make It Meaningful
Good pay, a fair work-life balance, and the job itself are all drivers of job satisfaction. But there’s another reason that motivates people to show up at work every day; knowing they are doing something meaningful.
Do your staff understand how the tasks they are responsible for fit into the bigger picture? Do they know what happens when an order comes in, and what happens after products leave the building? Do they ever hear the feedback you receive from customers?
Electronics manufacturing companies need to be open and transparent with all staff about their vision and purpose. If staff don’t understand what the business is trying to achieve, how can they truly buy into the process?
Provide a Positive Working Environment
The working environment can have a big impact on staff morale and productivity. I’m not suggesting you paint the walls of the manufacturing shop floor in bright yellow to cheer everyone up. But having a clean, tidy and safe working environment makes it easier for employees to do their job, and helps them feel energized.
The 5S methodology is one initiative manufacturers use to organize the workspace. The first three of the five steps involve removing tools not in use and clearing obstacles that slow down workflow, arranging items so they are ready to use, and regular cleaning and maintenance of equipment so small issues can be addressed before they become big problems.
Make sure staff have good quality tools and machinery to work with too. It would be understandably frustrating if someone was struggling with a task they knew could be a lot easier and more enjoyable if they had a better tool to use.
As much as your workforce may love their jobs, there will inevitably be things that frustrate or slow them down on a daily basis. Something as simple as moving an item they use regularly to a more convenient place, or upgrading a piece of machinery, could have a significant impact on how easy (and enjoyable) it is for them to do their job.
Listen!
Make sure staff have opportunities for their voice to be heard. And when they do share their views, listen to them.
Okay, so you don't want to face an onslaught of moans about everyday niggles. Rather, provide platforms for people to voice ideas for improvements. Create a culture where employees feel comfortable putting their hand up to say, "I've got an idea for how we can improve this process."
Provide accessible ways for staff to flag issues and share their ideas. Create a feedback wall on the factory floor where ideas will be visible to all. Hold regular process improvements where staff have the opportunity to share and discuss ideas. Or incorporate time into your current weekly meetings to discuss issues and ideas. Having an open culture will get everything out in the open.
Develop a systemized way for managers to collect feedback, review, and implement changes. The key message is: make it easy for people to provide feedback, and easy to manage so it doesn't become an administrative burden.
Allow Your Employees to Grow
When people are given the chance to learn new skills and expertise, it encourages them to take more pride in their work. And those who take pride in their work—they are your best workers. Provide opportunities for on-the-job training and knowledge sharing sessions.
Celebrate Success
A simple acknowledgement of thanks when employees have put in an extra effort to meet targets can have a big impact on morale. Whether you’re recognizing the efforts of a particular individual, or of a whole team, saying 'well done' never fails. And in peak periods when people need that extra boost to get things over the line, it's even more vital to celebrate their hard work. Your employees will remember it too, and energize them for the next busy period.
There are other ways to recognize the hard work of your employees more formally too, such as with bonuses, vouchers, or additional training. But research from the book The Carrot Principle shows frequent praise has a better impact on motivation than monetary rewards.
These are just some of the common sense ways you can increase motivation and engagement among your electronics manufacturing staff. But why not speak to your employees first? See what they think. They may have other ideas for how to increase motivation.
Suggested Items
Standard of Excellence: Delivering Excellence—A Daily Goal
06/25/2025 | Anaya Vardya -- Column: Standard of ExcellenceDelivering excellence consistently across all touchpoints is essential for organizations aiming to build trust, foster customer loyalty, and maintain their brand reputation. This requires a strategic approach encompassing uniform messaging, standardized service protocols, employee training, performance monitoring, and seamless integration across platforms.
Punching Out: Characteristics of Successful Leaders in North American PCB and EMS Sectors
06/11/2025 | Tom Kastner -- Column: Punching Out!I have worked in M&A in the PCB and EMS sectors for over 20 years and have met dozens of owners in these sectors. It has not been an easy environment to survive and thrive in, yet some companies have done well. Here are some characteristics of our most successful leaders in the industry (names withheld to protect the innocent).
The French Oil Mill Machinery Company Celebrates 125 Years of Innovation and Manufacturing Leadership
05/28/2025 | The French Oil Mill Machinery CompanyThe French Oil Mill Machinery Company marked its 125th anniversary this week, celebrating a rare legacy of continuous family ownership and manufacturing innovation.
K & F Electronics Invests in Workforce Training with IPC-A-610
05/15/2025 | K & F ElectronicsIn a strategic move to prioritize employee development and uphold quality standards, K & F Electronics, a third-generation, family-owned printed circuit board (PCB) manufacturer based in Fraser, Michigan, used a recent period of reduced production to certify its employees in IPC-A-610, the industry standard for the acceptability of electronic assemblies.
Microsoft to Lay Off 6,000 Workers Across All Departments
05/14/2025 | I-Connect007Microsoft announced on May 13 that it is cutting 3% of its workforce, which will affect 6,000 people across all levels, teams, and geographies. This, despite the fact that the company’s shares rose about 9% at the end of April, with better-than-expected results, with $25.8 billion in quarterly net income.