-
- News
- Books
Featured Books
- smt007 Magazine
Latest Issues
Current IssueWhat's Your Sweet Spot?
Are you in a niche that’s growing or shrinking? Is it time to reassess and refocus? We spotlight companies thriving by redefining or reinforcing their niche. What are their insights?
Moving Forward With Confidence
In this issue, we focus on sales and quoting, workforce training, new IPC leadership in the U.S. and Canada, the effects of tariffs, CFX standards, and much more—all designed to provide perspective as you move through the cloud bank of today's shifting economic market.
Intelligent Test and Inspection
Are you ready to explore the cutting-edge advancements shaping the electronics manufacturing industry? The May 2025 issue of SMT007 Magazine is packed with insights, innovations, and expert perspectives that you won’t want to miss.
- Articles
- Columns
- Links
- Media kit
||| MENU - smt007 Magazine
Creating a Healthy Work Environment
January 19, 2018 | Stephen Las Marias, I-Connect007Estimated reading time: 5 minutes
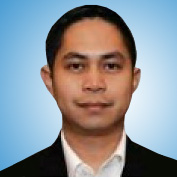
German-based ULT AG has been engineering and manufacturing top-notch fume extraction and air filtration devices for industrial applications since 1994. What started out as a one-man-band now employs more than 120 people. The company is focused on removing airborne dry dust and fumes from manufacturing processes, by dedicated, local devices. The goal is to contribute to a healthy work environment and to prevent parts and machinery from contamination.
Wolfgang Koehler is the CEO of the North America branch of ULT. In an interview with SMT007 Magazine, he discusses how their business has been over the past year, their challenges and opportunities, and how they are helping their customers. Another topic of discussion is investing in new equipment—the key parameters to consider, and what’s driving customers to buy their systems.
Stephen Las Marias: How has your business been last year, and what have been the major drivers for growth?
Wolfgang Koehler: We have done great over the past year. For our German HQ, 2017 has been another year of constant growth and development, showing that the course we plugged in is all about right. As the actual economy is strong in Germany and in many other parts of the world, we have been, among others, participating in the growing demand for sophisticated air filtration from laser manufacturing processes. In January 2017, we started our U.S. entity in Milwaukee, Wisconsin, following our global customer base to the Americas. This strategic move offers a huge potential for further growth.
Las Marias: From your perspective, what sort of challenges are your customers facing?
Koehler: Our customers are facing multiple challenges from global competition to swiftly changing demands of their customers. This is not limited to a few, but involving all kinds of industries, from electronics, automotive and aerospace, to defense, energy, medical, and many others. It is the daily challenge to keep up with the market and stay a little bit ahead of your competitors.
Figure 1: ULT offers a versatile extraction and filtration system for the efficient removal of soldering fume.
Las Marias: How are you helping your customers with their problems?
Koehler: It is all about creating awareness of appropriately dealing with hazardous, sometimes highly cancer-causing particulates. We are supporting our customers to protect their labor, their parts, and their manufacturing equipment from harm and contamination.
Las Marias: What forces do you see driving the industry as a whole?
Koehler: We see that new technologies are rapidly developing, especially in laser-based processes. Those, along with metal 3D printing, will be driving the industry for the next decade.
Las Marias: What challenges and opportunities do you see for your company in the upcoming years?
Koehler: We do see a huge potential especially in laser applications. For example, 3D printing from metal powder is a rapidly growing industry, with materials and processes that require proper air filtration and professional disposal. We have learned from experience that almost any metal powders used in laser 3D printing are bearing a certain risk to health and manufacturing processes. We are offering off-the-shelf and customized solutions for dealing with highly reactive nanoscale particulates from metal 3D printing processes. This makes us unique in the market. We are very well prepared to support any customer in any industry when air filtration from metal 3D printing is required. The major challenge for us is to create awareness and convince decision makers to invest in proper, local and dedicated air filtration.
Another opportunity for further growth is air purification in electronics manufacturing. Whether it is about soldering fume or laser fume removal, extraction and filtration of dust, odors, vapors or gases, there are various airborne pollutants that may have hazardous impacts on employees, manufacturing systems and products. Here we see enormous potential and opportunities to install our air handling solutions. It is any company’s target to protect their values in form of humans, machinery and product quality, which we are able to support by our fume extraction technology.
Las Marias: You’ve been in the industry for decades. What are some of the biggest changes you’ve seen?
Koehler: We have seen a thing or two throughout the last decades, that much is true. We have seen laser having a huge impact on manufacturing long before anyone else was thinking about laser fume extraction. For us, it is essential to foresee future trends in manufacturing and what kind of airborne particulates might be occurring in processes to come. That is why we are spending a fair amount of money every year on R&D and projects with well-known research institutes. It is all about understanding manufacturing processes to come up with air filtration solutions that perform at top level.
Figure 2: Fume extraction setup for hand soldering processes.
Las Marias: From your perspective, what are the top reasons when investing in new equipment?
Koehler: Higher output, less scrap, lower costs per piece, more stable processes, and keeping up with new technologies. There are multiple reasons for investing in new equipment.
Las Marias: In your line of business, what market drivers would move customers to buying your equipment?
Koehler: Frankly, we would need to have a stricter law enforcement when it comes to personal exposure limits (PEL) and environmental protection. We are looking at materials and processes resulting in sometimes extremely hazardous particulates. Those might harm labor as well as being highly combustible when, for example, exposed to oxygen. Not to mention the negative long-term effect when being ventilated outside without proper filtration.
Las Marias: What advice can you give customers who are looking to acquire extraction/filtration solutions?
Koehler: Give us a call.
Las Marias: Is there anything else you’d like to add?
Koehler: We are very experienced in what we are doing. We are a one-stop-shop for local fume extraction and air filtration needs. Automation companies, system integrators, OEMs and end users in any industry worldwide have been relying on our engineering and quality.
Las Marias: How do you see the electronics manufacturing industry developing this year?
Koehler: From our perspective, we are looking at a growing market share as we are extending our global customer base. The close collaboration with well-known OEMs in the industry and ongoing R&D projects are contributing to our outstanding position in this market.
Las Marias: Thank you very much.
Suggested Items
Hands-On Demos Now Available for Apollo Seiko’s EF and AF Selective Soldering Lines
06/30/2025 | Apollo SeikoApollo Seiko, a leading innovator in soldering technology, is excited to spotlight its expanded lineup of EF and AF Series Selective Soldering Systems, now available for live demonstrations in its newly dedicated demo room.
SolderKing’s Successful Approach to Modern Soldering Needs
06/18/2025 | Nolan Johnson, I-Connect007Chris Ward, co-founder of the family-owned SolderKing, discusses his company's rapid growth and recent recognition with the King’s Award for Enterprise. Chris shares how SolderKing has achieved these award-winning levels of service in such a short timeframe. Their secret? Being flexible in a changing market, technical prowess, and strong customer support.
E-tronix Announces Upcoming Webinar with ELMOTEC: Optimizing Soldering Quality and Efficiency with Robotic Automation
05/30/2025 | E-tronixE-tronix, a Stromberg Company, is excited to host an informative webinar presented by Raphael Luchs, CEO of ELMOTEC, titled "Optimize Soldering Quality and Efficiency with Robotic Automation," taking place on Wednesday, June 4, 2025 at 12:00 PM CDT.
SMTA Releases Final Batch of Training Resources Donated by Bob Willis
05/29/2025 | SMTAThe Surface Mount Technology Association (SMTA) announces the release of several more webinars, poster sets, and photo libraries to conclude a generous donation from renowned industry expert Bob Willis.
Altus Supports Phoenix Systems in Advancing THT Assembly with Robotic Soldering
05/27/2025 | Altus GroupAltus Group, a leading distributor of capital equipment in the UK and Ireland, has successfully supported Phoenix Systems UK Ltd in its investment in robotic soldering technology to further enhance its through-hole technology (THT) assembly processes.