-
- News
- Books
Featured Books
- pcb007 Magazine
Latest Issues
Current IssueInventing the Future with SEL
Two years after launching its state-of-the-art PCB facility, SEL shares lessons in vision, execution, and innovation, plus insights from industry icons and technology leaders shaping the future of PCB fabrication.
Sales: From Pitch to PO
From the first cold call to finally receiving that first purchase order, the July PCB007 Magazine breaks down some critical parts of the sales stack. To up your sales game, read on!
The Hole Truth: Via Integrity in an HDI World
From the drilled hole to registration across multiple sequential lamination cycles, to the quality of your copper plating, via reliability in an HDI world is becoming an ever-greater challenge. This month we look at “The Hole Truth,” from creating the “perfect” via to how you can assure via quality and reliability, the first time, every time.
- Articles
- Columns
- Links
- Media kit
||| MENU - pcb007 Magazine
Estimated reading time: 2 minutes
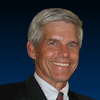
Polyimide vs. Silicone for Flexible Heaters
Flexible heaters are sub-divided into two primary technology platforms: etched-foil and wire-based technology. Wire-based (wire strands woven together or single strand wire) is the more common technology, with multiple customers offering a wide range of products. Etched foil heaters represent a newer technology (developed in the last 40 years…if that can be considered new!) and are used in more advanced thermal management applications with thickness limitations and multiplanar heated surfaces.
Flexible etched foil heaters are commonly grouped into categories based on their dielectric type. Three primary types of dielectrics are most common and each have advantages and disadvantages. Heater dielectric categories for this discussion include: Standard Polyimide, Silicone Rubber and High Temperature Polyimide.
Standard Polyimide
Polyimide is the primary material type chosen when high thermal control is desired with the thinnest construction possible. The amber-colored polyimide is often referred to as Kapton® a trade name of DuPont. Traditional polyimide heaters are constructed with two layers of polyimide film encapsulating an etched metal pattern of a resistive foil layer. The top and bottom polyimide film layers are bonded together using high performance thermoset acrylic adhesive.
Both flame-retardant (FR) grades and non-FR grades of adhesive are available. The polyimide film is rugged and can handle temperatures exceeding 300°C. The weak link in these constructions is the adhesive system which can become problematic at temperatures >150°C. Polyimide is also excellent for applications requiring low out-gassing.
Silicone Rubber
Silicone rubber (SR) is often utilized for general heater applications and is favored for its overall mechanical properties. Silicone rubber can be used for outdoor or wet environments and the overall thickness provides better protection from mechanical damage. Silicone rubber is frequently reinforced with a fiberglass grid which provides excellent dimensional stability. Silicone rubber heaters have a higher thermal rating at >230°C. However, SR heaters are less flexible and are not well-suited for component assembly.
Silicone rubber heaters are also much heavier, placing some limits on their ability to be bonded using typical pressure-sensitive adhesives. An attractive bonding option is to mount the silicone rubber heaters directly onto a heat sink using a vulcanizing process. This attachment method uses uncured silicone rubber as the bonding material. Silicone rubber heaters are rugged solutions for industrial and general use applications, but should be avoided when out-gassing is critical.
High Temperature Polyimide
Specialty applications are demanding higher and higher temperature performance from thin and flexible heaters. Downhole oil drilling is frequently mentioned as a particularly extreme high-temperature environment so flexible circuit materials developed for some of these specialty applications have been adopted in high temperature heaters. Advanced polyimide heater constructions have been recently developed and tested to perform well in applications up to 300°C (572°F). Elimination of the adhesive layer within the heater construction is a prerequisite to achieve these performance requirements. Combining these specialty adhesiveless materials with newly developed manufacturing processes can create products with exceptionally high temperature heater performance.
The chart below provides a comparison among three flexible heater materials. It should be noted these are standard parameters and should be considered safe as guidelines. Exceeding these operating ranges is often possible but consultation with an applications engineer, along with some prototype testing, is recommended.
*Continuous Operating Temperatures.
**Application specific and must be validated by customer.
*** Bond data per 3M specification and test protocol. Actual data will vary depending on application.
Related Reading:
- All Flex Heater Circuit Design Guide
- 300C High Temperature Flexible Heaters
- Understanding Etched Foil Heaters
Dave Becker is vice president of sales and marketing at All Flex Flexible Circuits LLC.
More Columns from All About Flex
All About Flex: Terms and ConditionsAll About Flex: ISO 9001 Basics
All About Flex: FAQs on UL Listings for Flexible Circuits
All About Flex: Avoiding Trace Fracturing in a Flexible Circuit
All About Flex: Copper Thickness Requirements for Flex Circuits
All About Flex: Copper Grain Direction
All About Flex: Options for Purchasing Flexible Heaters
All About Flex: More on UAVs and Flexible Circuits