-
- News
- Books
Featured Books
- pcb007 Magazine
Latest Issues
Current IssueInventing the Future with SEL
Two years after launching its state-of-the-art PCB facility, SEL shares lessons in vision, execution, and innovation, plus insights from industry icons and technology leaders shaping the future of PCB fabrication.
Sales: From Pitch to PO
From the first cold call to finally receiving that first purchase order, the July PCB007 Magazine breaks down some critical parts of the sales stack. To up your sales game, read on!
The Hole Truth: Via Integrity in an HDI World
From the drilled hole to registration across multiple sequential lamination cycles, to the quality of your copper plating, via reliability in an HDI world is becoming an ever-greater challenge. This month we look at “The Hole Truth,” from creating the “perfect” via to how you can assure via quality and reliability, the first time, every time.
- Articles
- Columns
- Links
- Media kit
||| MENU - pcb007 Magazine
Estimated reading time: 3 minutes
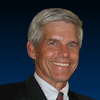
All About Flex: Avoiding Trace Fracturing in a Flexible Circuit
Flexible circuits are used in applications requiring millions of flex cycles. But this does not suggest they never experience failures due to flex life. In fact, occurrences of performance issues as the result of fractured traces have been experienced in a variety of applications. Solutions are often the result of design, construction, and feature location modifications. But a much better solution is to avoid the problem in the first place!
A flexible circuit’s ability to be bent, twisted, folded and continuously flexed is a significant advantage offered as a designer considers this interconnect method in a new product. The design options are myriad with “origami” packaging being an accurate description of how the product is often used. But it is true that improper designs and/or specifications have resulted in “bad experience” anecdotes about trace fracturing problems.
The following are some pitfalls to avoid and minimize the chance a design will experience premature failure.
High Stress Points
There are several ways a designer might inadvertently lay out traces and create a higher level of mechanical stress during bending. Designs with traces on opposite sides of the dielectric laying directly over each other will create an “I-beam effect” (Figure 1).
Figure 1
With traces mapped directly over each other, added stress occurs on the traces located on the outside of a bend radius. The traces on the outside of a bend radius are in tension mode while the layers on the inside are in compression. Traces in tension tend to develop micro-fractures if they are flexed repeatedly. During failure analysis these can be particularly difficult to diagnose as the open circuit often occurs intermittently.
Another mechanical stress point occurs at the end of a stiffener, which will tend to focus stress at the stiffener termination line. A simple design feature solution is often to overlap the coverlay termination on the opposite side (Figure 2).
Figure 2
Solder joints/vias too close to bend points
While copper foil is fairly ductile, the alloy resulting on a solder joint becomes brittle. These regions are particularly susceptible to trace fractures as the region defined by the junction of coverfilm and solder pad cannot take significant bending. Figure 3 shows a safe distance between the bend location and a solder joint or plated through-hole.
Figure 3
Unbalanced Dielectric Thickness
This problem is avoided by locating the copper traces in the “neutral axis” of the circuit (i.e., by having equivalent material thicknesses above and below copper in regions to be repeatedly flexed). Polyimide film has been proven as a robust material for dynamic flex applications and is used almost exclusively in these applications. Although screen-printed or photoimaged solder mask are sometimes used as dielectrics, it is rare to find these alternative materials used in applications requiring high flex life. They tend to be brittle and are likely to craze or crack when folded or repeatedly bent.
In some applications it is necessary to use photoimaged soldermask for its high-resolution capability for component openings. But if these parts are also to be dynamically flexed, polyimide is again used in the flexing region of the circuit, creating a circuit with dual insulation materials and processing.
Copper Selection
There are two basic types of copper foil: electrodeposited (ED) and rolled annealed (RA). They have significantly different grain structures and bending properties. Using ED copper for high flex applications can result in infant mortality. RA copper offers significantly better flex life. Also important is the copper grain direction on RA copper as flex life is much higher when the fold or bend line is perpendicular to the grain. Keeping the circuit composite thin perpetuates flex life. A copper thickness of one ounce and thinner is a good design practice.
Copper selection errors can also occur with two+ layer circuits when creating plated through-holes. Avoiding the addition of electroplated copper in a flex region is possible by masking during copper plating. This restricts the addition of electroplated copper to the copper pads and the vias. This fabrication method avoids the addition of electroplated copper in a flex zone and keeps copper thicknesses to a minimum. This is a pretty common process known as “pads only plating” or “button plating.” Both features can be key to a robust design and are often called out specifically as requirements on a customer’s drawing.
There are many industry guidelines a designer can reference to avoid these and other issues when designing/laying out a flexible circuit. I always encourage customers to specifically mention dynamic flexing and flex location requirements on their product documentation. This helps the supplier make recommendations regarding circuit layout and construction options.
Dave Becker is vice president of sales and marketing at All Flex Flexible Circuits LLC.
More Columns from All About Flex
All About Flex: Terms and ConditionsAll About Flex: ISO 9001 Basics
All About Flex: FAQs on UL Listings for Flexible Circuits
Polyimide vs. Silicone for Flexible Heaters
All About Flex: Copper Thickness Requirements for Flex Circuits
All About Flex: Copper Grain Direction
All About Flex: Options for Purchasing Flexible Heaters
All About Flex: More on UAVs and Flexible Circuits