-
- News
- Books
Featured Books
- pcb007 Magazine
Latest Issues
Current IssueInventing the Future with SEL
Two years after launching its state-of-the-art PCB facility, SEL shares lessons in vision, execution, and innovation, plus insights from industry icons and technology leaders shaping the future of PCB fabrication.
Sales: From Pitch to PO
From the first cold call to finally receiving that first purchase order, the July PCB007 Magazine breaks down some critical parts of the sales stack. To up your sales game, read on!
The Hole Truth: Via Integrity in an HDI World
From the drilled hole to registration across multiple sequential lamination cycles, to the quality of your copper plating, via reliability in an HDI world is becoming an ever-greater challenge. This month we look at “The Hole Truth,” from creating the “perfect” via to how you can assure via quality and reliability, the first time, every time.
- Articles
- Columns
- Links
- Media kit
||| MENU - pcb007 Magazine
Estimated reading time: 8 minutes
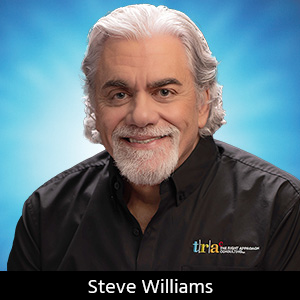
Willy Wonka: The Lean Case Study
Introduction
No matter where my travels take me, I hear a wide and limitless supply of excuses for why Lean will not work in “my” organization. One of my favorite ways of illustrating that Lean will indeed work anywhere is to take a Lean look at a very unlikely organization, Willy Wonka’s Chocolate Factory.
Why Willy Wonka
The inspiration for this case study came from one of my Lean Principles graduate students, who told me that while she was studying diligently one evening, her son was watching the video Charlie and the Chocolate Factory. She said, “Professor” (I love it when they call me professor!), “as I sat there listening to the underlying ideas behind the Chocolate Factory, I got distracted in my reading and realized I was watching a show that is formulated on the idea of creating a Lean factory.” As we discussed this in great detail, she presented a very compelling argument to support her position. So, that following weekend I purchased the DVD, and sat down with a bowl of popcorn, a cold Budweiser and my notepad and turned a critical Lean eye to Roald Dahl’s classic tale. What follows are the results of that session, which led to the development of a Lean case study that I now use both academically and professionally.
WILLY WONKA CASE STUDY
1 — The Need for Lean
Competition
The Willy Wonka Chocolate Factory was infiltrated by industrial spies trying to steal Wonka’s secret recipes and manufacturing technology. This espionage resulted in a proliferation of copycat low-cost products flooding the market, and while inferior to the Wonka quality, were quite successful as consumers made their buying decisions based on price. The Willy Wonka Chocolate Factory was devastated and could not compete with these low-cost candy bars, which resulted in the closure of the factory and loss of thousands of jobs, including Charlie Batch’s Grampa Joe. Grampa Joe was a lifelong employee of the Wonka factory and approaching retirement when the factory closed down. In a related story line, Charlie’s father was also recently downsized at the local toothpaste factory after being replaced by a robot to reduce costs. Consumer pricing pressure had certainly caused the Batch family to fall on hard times.
Side Note: This part of the story was based on personal experiences from Dahl’s childhood. The two largest British candy firms, Cadbury and Rowntree, sent so many moles to work in competitors’ factories that their spying became legendary.
2 — Reducing Costs
Outsourcing
After closing the factory, Willy Wonka traveled the world looking for a low-cost country (LCC) in which to re-establish his business that would allow him to become competitive again. He was beginning to lose hope, but then Willy reached LoompaLand, where he discovered an entire population of highly skilled and dedicated workers, the Oompa Loompas, who were destined for extinction by the monsters of their native land. So, instead of bringing the factory to the low-cost country, Willy brought the low-cost country to the factory (reshoring)!
3 — Eliminating the Seven Deadly Wastes
Defect Waste
Jidoka built-in-quality was evidenced throughout the process, with my favorite example being the team of squirrels performing quality-at-the-source verification in the nutshelling department. Years of continuous process improvement has resulted in the development of a chocolate waterfall that provides an automated, low-cost chocolate mixing system which produces Wonka’s world-class “light and frothy” chocolate. Robust statistical process control and capability study programs have allowed continuous process improvement that has resulted in the factory’s ability to achieve and maintain the current six sigma level of performance.
Motion Waste
All the manufacturing processes were designed to be highly automated, with each having an advanced technology control center requiring minimal manpower to operate. Through the 6S methodology, all materials and tools are stored at the source to eliminate internal travel time waste. Every task within each control center has also been ergonomically designed for the Oompa Loompas so that every control, gauge, and monitor is within easy reach.
Waiting Waste
Given the vast size of the operation (the largest in the world), moving people and product around the factory is quite the task. Queue time (waiting waste) was virtually eliminated with the Wonka-invented flying elevator, which quickly transports employees and WIP throughout the factory. Lean practices are evident throughout the operation, and the art of chocolate making has developed into a continuous flow manufacturing process. A hovering spaceship sucks up thousands of gallons per hour of WIP from the chocolate river and transports it throughout the factory for real-time subsequent processing.
Overprocessing Waste
The factory was designed to produce only products featuring qualities that customers not only want, but are willing to pay for. Understanding customer needs and preferences was accomplished by performing a critical to quality analysis of Wonka’s products based on voice of the customer feedback. The fantastical manufacturing technology employed by Wonka was all developed in-house in the Inventing Room, the organization’s R&D lab. Driven by data mined from his voice of the customer program, Wonka was also concerned with eliminating waste for his customers as well.
The invention of the Three Course Dinner stick of gum was intended to reduce waste in the home, as food, cooking time, and kitchens for that matter, are all eliminated by a single stick of gum!
Inventory Waste
Inventory has been minimized through the organization’s just-in-time program, which has been implemented both internally and externally.
All manufacturing processes utilize a kanban pull system that minimizes work-inprocess inventory by only manufacturing what is needed, when it is needed. This system has also been implemented with Wonka’s raw material suppliers, who have eliminated raw material inventory through electronic data interchange transactions and supplier-managed inventory programs. Kanbans have also been set up with Wonka’s retail customers so that product replenishment is driven by consumption, not forecast.
Page 1 of 2
More Columns from The Right Approach
The Right Approach: ‘Twas the Night Before Christmas (Harley-style)The Right Approach: I Hear the Train A Comin'
The Right Approach: Culture Change is Key to a QMS
The Right Approach: Leadership 101—Be a Heretic, Not a Sheep
The Right Approach: Leadership 101—The Law of Legacy
The Right Approach: Leadership 101: The Law of Explosive Growth
The Right Approach: Leadership 101—The Law of Timing
The Right Approach: The Law of Sacrifice