-
-
News
News Highlights
- Books
Featured Books
- pcb007 Magazine
Latest Issues
Current IssueSales: From Pitch to PO
From the first cold call to finally receiving that first purchase order, the July PCB007 Magazine breaks down some critical parts of the sales stack. To up your sales game, read on!
The Hole Truth: Via Integrity in an HDI World
From the drilled hole to registration across multiple sequential lamination cycles, to the quality of your copper plating, via reliability in an HDI world is becoming an ever-greater challenge. This month we look at “The Hole Truth,” from creating the “perfect” via to how you can assure via quality and reliability, the first time, every time.
In Pursuit of Perfection: Defect Reduction
For bare PCB board fabrication, defect reduction is a critical aspect of a company's bottom line profitability. In this issue, we examine how imaging, etching, and plating processes can provide information and insight into reducing defects and increasing yields.
- Articles
- Columns
- Links
- Media kit
||| MENU - pcb007 Magazine
Estimated reading time: 8 minutes
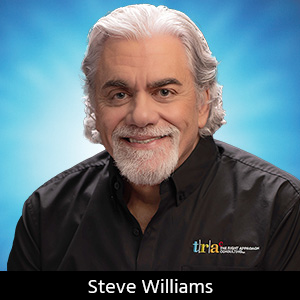
Willy Wonka: The Lean Case Study
Overproduction waste is minimized in a variety of ways at the Wonka Chocolate Factory. First, the Wonka voice of the customer program assures that the factory is only making products that customers want, eliminating finished goods obsolescence. Next, the kanban pull continuous flow manufacturing system minimizes the work-in-process inventory that normally builds up between operations. Finally, the six-sigma process performance level keeps defects to a minimum, and the just-in-time kanban systems eliminate raw material and finished goods inventory at the Wonka factory.
Transportation Waste
Transit time waste was greatly reduced by utilizing a very impressive global logistics system to distribute Willy Wonka candy bars from the factory to retail outlets throughout the world. Order fulfillment is accomplished via a massive, well-oiled freight division that utilizes company-owned ground and air transportation. A cutting-edge “Television Chocolate” technology is also currently under development that will transport a chocolate bar through the TV to customers all over the world, thus eliminating transit time waste.
4 — Life Imitates Art
Or does art imitate life? In the end, Charlie’s dad gets his job back at the toothpaste factory as a robot technician, keeping the machine that replaced him operating. One of the biggest fears people have of Lean is that they will no longer be needed. Charlie’s dad was retrained and redeployed at a new position that was much more personally enriching, which happens every day in the real world. Willy Wonka’s processes were environmentally friendly, with much of the by-products edible and biodegradable. The bottom line is that, yes, Willy Wonka was a Lean visionary and his Chocolate Factory a study in the ultimate goal of Lean: manufacturing perfection!
Although this is obviously a tongue-in-cheek look at a fictional company, the concepts and theory liberally applied by the author’s imagination are technically sound and based in fact. It then follows that, if Lean can be successfully implemented in the fantastical setting of Willy Wonka’s Chocolate Factory, it most certainly will work in your company.
Conclusion: Lean Works
I would be willing to take it a step farther and state that I can guarantee that Lean will work in any industry, in any organization if the following two conditions are met: (1) Senior management must fully buy in to the program, and (2) it is implemented correctly. As with any new program, initiative, or philosophy, management buy-in and commitment is mission critical.
Lean is not free, or even cheap, when you consider the time and human resources that must be expended on a regular basis. It takes money to save money, and an organization can’t realistically expect to significantly improve performance without investing in training, organizational infrastructure and cultural evolution. Sure, it costs money to implement any training program, but the initial training is only the tip of the iceberg. The major expense in a Lean program is the ongoing cost of human resources.
If management is not willing to allocate the appropriate time for their employees to work on Lean projects, the program is sure to fail, and fail spectacularly. The good news is that the hard dollar payback of a solid program can be equally spectacular. Fortune 500 companies have saved billions of dollars through Lean, but even the mom-and-pop small business that make up most America’s jobs can see tremendous benefit through Lean practices.
My closing advice would be to do something now! Waiting for a plan to be perfect will only ensure that it never begins; doing something now is always better than doing something later. I will close with a quote from Karen Lamb, courtesy of my friend Tom Peters: “A year from now you may wish you had started today.” And remember, it’s always about the dollars.
Steve Williams is the president of The Right Approach Consulting LLC. To read past columns, or to contact Williams, click here.
Page 2 of 2More Columns from The Right Approach
The Right Approach: ‘Twas the Night Before Christmas (Harley-style)The Right Approach: I Hear the Train A Comin'
The Right Approach: Culture Change is Key to a QMS
The Right Approach: Leadership 101—Be a Heretic, Not a Sheep
The Right Approach: Leadership 101—The Law of Legacy
The Right Approach: Leadership 101: The Law of Explosive Growth
The Right Approach: Leadership 101—The Law of Timing
The Right Approach: The Law of Sacrifice