Triangle Labs: Covering the Niche Market of Large Boards
May 18, 2018 | Patty Goldman, I-Connect007Estimated reading time: 11 minutes
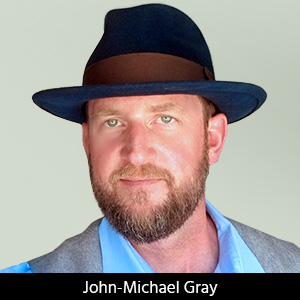
I recently had the opportunity to speak with John-Michael Gray, president of Triangle Labs. We had quite a discussion on their rather unique capability of building large-format PCBs and multilayers—perhaps the largest PCBs in the world. To make very large PCBs, one needs some very large processing equipment—room-sized—as is the case with Triangle Labs.
Patty Goldman: John-Michael, please begin by telling me a little bit about yourself and Triangle Labs.
John-Michael Gray: Absolutely. I got my start with Triangle Labs when I was 22 years old, and I am 39 now, so about 17 years with the company. I started working in the back in the photo department, then moved over to processing, with a small stint in plating, and then back to photo. I really have a good, fundamental understanding of board processioning and fabrication, but not quite a mastery. Then I was found to be better suited to the front end and moved into a sales role. I transitioned in as president over the past two years after my work in the business development arena, which I still lead. I'm still out there in the field meeting with customers and maintaining the sales department. It's been great.
Goldman: Give me some background on Triangle Labs.
Gray: Triangle Labs was formed in 1994, in Redwood City, California. We are historically a Silicon Valley company, but the permitting and regulations in California at the time really didn't encourage hardware manufacturing companies, mainly PCB shops. We looked for a new location and found Carson City, Nevada, where the permitting fees were about 30x smaller than California. We moved here in 2004 and have been here for about 14 years now, which has been wonderful. Here we were able to install a 20,000 square foot facility with full electroplating on-site, which we did not have in Redwood City—we just had engineering and on-site services there.
Goldman: And now you can make the full circuit boards.
Gray: Yes, we can. In fact, according to my research, we make the largest circuit in the world that is a full master panel, at 48” x 96”. I don't know of many people that can do that.
Goldman: That must be a great niche to be in.
Gray: Yes, absolutely.
Goldman: Tell me more about Triangle Labs.
Gray: Currently we have 19 full-time employees. This building was originally 15,000 square feet, but we just added on 5,000 square feet onto the back to expand our large board capabilities, so 19 employees in a 20,000 square foot facility right now.
It looks like we're working in two departments: one is our core microwave work, which we've been doing for many years that supports Raytheon, Boeing, Lockheed Martin, and companies like that; and then there is our large format PCB manufacturing. We've purchased all new equipment for the large format PCBs—new processing equipment, new conveyorized Chemcut lines, and I believe the largest laser direct imager in the world now, which is a Limata UV-O LDI that can handle the 48 x 96 panels. We've really expanded into that big board niche market.
Goldman: That must be a big machine. What are the dimensions?
Gray: It's basically the size of a small room. It's probably 14’ x 8’, and it’s about seven feet tall. It's taller than me, and I'm pretty tall.
Goldman: What else can you tell me about Triangle?
Gray: We're a preferred supplier for Raytheon on all of their AESA radar systems, so we provide quite a few part numbers to Raytheon TAS-Tactical Airborne Systems, for their AESA radars, primarily F-15, F-18, and to a lesser extent the F-16. That's our core work that we really pride ourselves on. We have a perfect delivery record, and a full quality system. We expanded into the large board business in 2010, and we are currently building all 1,800 replacement boards for the ATLAS New Small Wheel upgrade at the (LHC) Large Hadron Collider, in Geneva Switzerland at CERN. That's been an exciting, yet challenging program. They want us to maintain basically a 2-mil deviation from top to bottom on a 48” x 86” board.
Goldman: Is all the equipment is conveyorized?
Gray: Yes, other than the optical CMM that we use to measure the features, everything is conveyorized and requires two people for handling.
Goldman: I would think two people would be necessary, because of course you have to move the panels from one piece of equipment to another at some point.
Gray: Yes, we created many custom racks so the board comes off from one conveyor, it slides onto the rack, it goes vertical, and the operator takes it to the next station. There's very little hand carrying of the boards. They're actually all semi-automated racks that we use to transport the large boards.
Goldman: That's good. And I take it all your equipment was specially designed for you?
Gray: Yes, absolutely. All the equipment was specially designed. We have subject matter experts and a lot of people who work on just the handling of such a big board because handling really is a major concern for something so big. You're not putting this board on a small board rack. It's on a big wheeled rack with casters on it at this point.
Goldman: Are these rigid boards?
Gray: Some of the skins or innerlayers are 4 mils, up to 062”. Yes, they are rigid FR-4 boards. But we can also process PTFE and Polyimide boards to this size as well.
Goldman: But even rigid panels must still bend and flex when they're that long, right?
Gray: Exactly.
Goldman: You've got the laser-direct imaging, but what about drilling? How is that done?
Gray: That's a great question. We custom-ordered two Pluritec MEGA drilling machines that would normally be set up for a minimum of three heads and basically had Pluritec turn those into a single-head and double-head unit that can handle 54” x 120”. We can drill and rout a large panel like that. We repurposed existing equipment to accommodate the large size. We also ordered two Schmoll-Machinen machines that are one meter by one meter, which is about 40” x 40”, give or take. Everything's very large in our facility. Even our smaller equipment is large, compared to the standard 18” x 24” board.Page 1 of 2
Suggested Items
TT Electronics Secures £20 Million in Aerospace and Defence Contracts as European Programmes Accelerate
06/06/2025 | TT ElectronicsTT Electronics has been awarded more than £20 million in new and renewed defence contracts, marking a major step forward in its contribution to Europe’s rapidly evolving defence landscape.
Elma Electronic Bolsters Quality Management Company-wide with Added AS9100:D and ISO9001:2015 Certifications
06/02/2025 | Elma ElectronicElma Electronic now includes AS9100:D and ISO 9001:2015 certifications at its Horsham, Pa. manufacturing facility, earning the company a multiple site accreditation designation.
See TopLine’s Next Gen Braided Solder Column Technology at SPACE TECH EXPO 2025
05/28/2025 | TopLineAerospace and Defense applications in demanding environments have a solution now in TopLine’s Braided Solder Columns, which can withstand the rigors of deep space cold and cryogenic environments.
ICEFlight to Accelerate Maturation of Cryogenic Technologies for Hydrogen-Powered Flight
05/27/2025 | GKN AerospaceGKN Aerospace is one of the project partners in ICEFlight (Innovative Cryogenic Electric Flight), a project aiming to contribute to the development of hydrogen-powered flight.
Vertical Aerospace Makes Aviation History with Piloted eVTOL Flight in Open Airspace
05/27/2025 | BUSINESS WIREVertical Aerospace, a global aerospace and technology company that is pioneering electric aviation, announced it has made European aviation history with the first-ever piloted wingborne flight of a winged electric vertical take-off and landing (eVTOL) aircraft in open airspace.