Experts Discussion: The Flex Technologists Speak
June 5, 2018 | I-Connect007 Editorial TeamEstimated reading time: 4 minutes
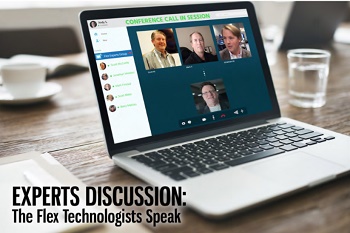
For our first issue of the Flex007 Magazine, we invited a group of flexible circuit experts to discuss their work in this rapidly growing segment. Participants included Jonathan Weldon of DuPont, Mark Finstad of Flexible Circuit Technologies, and Scott McCurdy and Scott Miller of Freedom CAD. In a free-wheeling discussion with Andy Shaughnessy and Barry Matties, these technologists share their thoughts on the challenges and opportunities in flexible circuits, as well as what constitutes the cutting edge of flex right now.
Andy Shaughnessy: Why don’t we just start with some introductions? Jonathan, would you tell us about yourself?
Jonathan Weldon: I’ve been with DuPont for about two and a half years. I’m an RF application engineer so I focus primarily on Pyralux™ flexible copper-clad laminates and the Kapton films that go with those. They’re used in everything from consumer electronics through industrial applications. I’m an EE undergrad, EE grad, and all focused in electromagnetics. I was in the Air Force for about eight years doing electro-optics, radar work, and all sorts of jammer work developing jam patterns and a few other things for the systems. And then I worked at Sandia National Labs before coming to DuPont. I’m typically an analog guy. I came from the defense side. I still try to stay close to the defense side, but have been sort of mixing into the consumer electronics world since being in this industry.
Shaughnessy: Scott McCurdy, how about your background?
Scott McCurdy: I’m with Freedom CAD. I’ve been in the PCB design world for the last dozen years. In a past life, I owned a printed circuit board manufacturing company for 32 years. Also, I’ve been the president for the last 15 years of the Orange County IPC Designers Council, the largest chapter in the country. I just started my 50th year in the printed circuit world. I started when I was four. (Laughs)
Scott Miller: I’m the chief operating officer at Freedom CAD Services. We perform contract printed circuit board design and layout services and provide prototype assemblies. I started my career with DuPont back in 1978 and it was a division of DuPont called Berg Electronics, which was a connector manufacturer. I’ve been with Freedom CAD for about 15 years and I always enjoy keeping up on what’s going on between the materials and the design world.
Shaughnessy: All right. Give us a little background, Mark.
Mark Finstad: I’m the senior application engineer at Flexible Circuit Technologies. I’ve been there for about eight years. Prior to that, I was with Minco for 27 years. During that time, I was heavy into the military and avionics. Now, at Flexible Circuit Technologies, I design flex for commercial and non-implantable medical and other applications like that. I’ve been doing this for 35+ years. I co-chair the IPC 2223 committee and I’m on the 6013 committee, and the Flex Materials committees. I’ve been on those committees for decades now, so I guess I’m a lifer at this point.
Shaughnessy: Jonathan, what’s important to you and your flex customers?
Weldon: It’s been kind of tough starting into the 5G world. I throw it out there just to get the words out because I know it’s sort of a hot topic right now everywhere. For me, I still view it as high-speed/high-frequency materials, right? But, 5G has become the trend in all of those discussions. One thing that seems to be true is that I’m not seeing anybody break any of that down into what I’ll call components. They’ll talk about base stations, they’ll talk about nodes, and they’ll talk about handsets. But none of that trickles down to requirements, constructions, antenna types, material choices, and fabrication challenges, or any of those sorts of subsets that are the real meat of 5G. I don’t know if other people are finding good sources for that, but everywhere I’ve looked it’s still been a little thin or a little ambiguous. It’s still very high level. So, that would be one of the first things I would add to the first flush. This would be useful for me looking at a magazine, getting into those sorts of details about that whole market and what that’s going to look like.
Shaughnessy: How about flex materials? That’s one of the things we always hear. The designers are always saying that they need to know more about materials.
Weldon: There are two sides to every story, right? I work on one side, looking at new materials and how we can get our current materials in. I hear a lot of talk about LCP still. I hear a lot of talk about other sorts of exotics that are out there. But I don’t really have any fieldcovered reviews. If I look at an iPhone or something like that, maybe it has 10 to 20 flex circuits in there and those flex circuits all have different requirements. Different flex requirements, different materials requirements. Nowhere is that really broken down. Obviously, that’s proprietary to that specific fabricator, but where does LCP need to go there? Maybe that may be the kind of feed line and antenna. Where you can go with the polyimide? Where can you go with a lower performing polyimide? Where can you swap out ED copper for RA copper? That is some of the specific details that I might be looking at.
To read the full version of this article which originally appeared in the April 2018 issue of FLEX007, click here.
Suggested Items
RF PCB Design Tips and Tricks
05/08/2025 | Cherie Litson, EPTAC MIT CID/CID+There are many great books, videos, and information online about designing PCBs for RF circuits. A few of my favorite RF sources are Hans Rosenberg, Stephen Chavez, and Rick Hartley, but there are many more. These PCB design engineers have a very good perspective on what it takes to take an RF design from schematic concept to PCB layout.
Trouble in Your Tank: Causes of Plating Voids, Pre-electroless Copper
05/09/2025 | Michael Carano -- Column: Trouble in Your TankIn the business of printed circuit fabrication, yield-reducing and costly defects can easily catch even the most seasoned engineers and production personnel off guard. In this month’s column, I’ll investigate copper plating voids with their genesis in the pre-plating process steps.
Elephantech: For a Greener Tomorrow
04/16/2025 | Marcy LaRont, PCB007 MagazineNobuhiko Okamoto is the global sales and marketing manager for Elephantech Inc., a Japanese startup with a vision to make electronics more sustainable. The company is developing a metal inkjet technology that can print directly on the substrate and then give it a copper thickness by plating. In this interview, he discusses this novel technology's environmental advantages, as well as its potential benefits for the PCB manufacturing and semiconductor packaging segments.
Trouble in Your Tank: Organic Addition Agents in Electrolytic Copper Plating
04/15/2025 | Michael Carano -- Column: Trouble in Your TankThere are numerous factors at play in the science of electroplating or, as most often called, electrolytic plating. One critical element is the use of organic addition agents and their role in copper plating. The function and use of these chemical compounds will be explored in more detail.
IDTechEx Highlights Recyclable Materials for PCBs
04/10/2025 | IDTechExConventional printed circuit board (PCB) manufacturing is wasteful, harmful to the environment and energy intensive. This can be mitigated by the implementation of new recyclable materials and technologies, which have the potential to revolutionize electronics manufacturing.