Modeling an SMT Line to Improve Throughput
June 6, 2018 | Gregory Vance, Rockwell Automation Inc., and Todd Vick, Universal Instruments Corp.Estimated reading time: 5 minutes
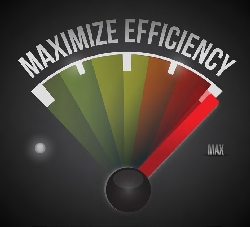
One of the major challenges for an electronics assembly manufacturing engineer is determining how an SMT machine will impact throughput. Typically, an SMT equipment supplier will ask for a few (5-10) products to simulate the throughput capability of their machine. Unfortunately, if the engineer works in a high-mix, low-volume environment, he may need to know the impact of a new machine on 1,000 or more products. Currently, there are no simulation tools to effectively model this. This is confirmed in the 2015 IPC International Technology Roadmap for Electronics Interconnections, which states, "In order to better deal with the demands for increased interconnection density and respond to market demands for better return on capital investment in assembly equipment, there is a need within the manufacturing industry for continued improvement in tools and software for modeling and simulation. Needs in this area include better methods of load balancing and improved machine utilization. The tools for determining the balance on assembly lines will need to be flexible to handle the mix of assembly types that manufacturers now face."
Rockwell Automation partnered with Universal Instruments to develop a tool to model a large quantity of products and the impact of varying SMT line configurations. The information used for the modeling includes placements per panel and components placed per hour. With these tools, an electronics assembly plant can be analyzed to identify improvement opportunities and perform "what if" analysis to model impact of machine changes.
Goals for the SMT Line Model
1. Determine the right machine for the product mix.
2. Determine if products are running as fast as they should.
3. Determine if electronics assembly products are built on the optimal line configuration. This is crucial in plants with multiple line configurations.
Development of the SMT Machine Model
1. Discovery that machine cycle times were poor
After sample product simulations were run by Universal Instruments, it was discovered that observed cycle times were two to three times longer than simulated cycle times. This led to a focused effort to understand why. A kaizen event was held to map out the process and observe product builds. Several items that impacted the product cycle time were uncovered. These items were:
1. Component library placement speed slowed down.
2. Imbalance between placement beams/heads due to not having enough nozzles to pick and place the required component packages for the products.
3. Bypassed nozzles and spindles.
4. Large quantity of placements from a single component input.
5. Panel transfer rate into and out of the machine slowed down.
6. Poor optimization and component split between machines on an SMT line.
7. Operator variation in responding to the process.
The most significant item impacting cycle time was not having the necessary quantity of nozzles available for the mix of component packages for the products that the machine/line was building. To maximize flexibility to move products between lines, machines of the same type were equipped with a standard nozzle configuration. The nozzle configurations were changed only when a new component package was needed. To address this problem, a regular nozzle review was implemented to ensure the machines have sufficient nozzles available to optimize the machine programs.
Products were reviewed for the above issues. As items were addressed, the observed cycle times were reduced to align with the simulated cycle times.
2. Realization that cycle time does not represent SMT machine utilization
Cycle time represents how a product is running compared to a benchmark but does not reflect utilization of a machine based upon its throughput capability. For pick and place machines, throughput can be measured in components placed per hour (CPH).
Table 1. Sample of range of placements per panel to run IPC and manufacturer tests.
Manufacturers provide CPH specifications for SMT machines in two ways. The first method is what is often called "Maximum CPH", which represents the maximum speed the manufacturer was able to achieve and the second is based on "IPC 9850", which has CPH categorized by package type. The “placements per panel” required to run these tests are shown in Table 1.
The "IPC 9850" performance tests are useful to compare equipment models and manufacturers to each other, but they do not necessarily represent the products manufacturers are building. This complexity can be understood by comparing Table 1 to the sample product complexity of global product mix in Table 2.
Page 1 of 2
Suggested Items
TRI to Exhibit at SMTA Queretaro Expo 2025
07/16/2025 | TRITest Research, Inc. (TRI), the leading provider of test and inspection systems for the electronics manufacturing industry, is pleased to announce plans to exhibit at the SMTA Querétaro Expo 2025, scheduled to take place on July 24, 2025, at the Querétaro Centro de Congresos y Teatro Metropolitano.
Global PCB Connections: Let the Spec Fit the Board, Not Just the Brand
07/17/2025 | Jerome Larez -- Column: Global PCB ConnectionsIf you’ve ever seen an excellent PCB quote delayed, or worse, go cold because of a single line on the fab print, you’re not alone. Often, that line reads something like, “Use 370HR only,” or “IT-180A required.” These and other brand-name materials are proven performers, but unless your design needs that specific resin system (say, for RF performance, thermal reliability, or stringent CAF resistance), you may inadvertently be holding your job hostage.
IPC Hall of Fame Spotlight Series: Highlighting Lionel Fullwood
07/15/2025 | Dan Feinberg, I-Connect007Many IPC members who have contributed significantly to IPC and our industry have been awarded the IPC Raymond E. Pritchard Hall of Fame (HOF) Award. Though many early HOF members have passed away and are unknown to today’s IPC membership, their contributions still resonate. This special series on IPC Hall of Fame members provides a reminder of who was honored and why. As a bonus, for those who are still around, we get to find out what these talented individuals are up to today.
TRI Unveils New Platform for Diverse Board Sizes
07/14/2025 | TRITest Research, Inc. (TRI), the leading test and inspection systems provider for the electronics manufacturing industry, proudly introduces a new size configuration for SPI and AOI Models.
Seeing a Future in Mexico
07/09/2025 | Michelle Te, I-Connect007The Global Electronics Association (formerly known as IPC) has been instrumental in fostering a partnership with Guanajuato, a state north of Mexico City with 12 industrial clusters and close to 150 companies involved in electronics. This past spring, Alejandro Hernández, the undersecretary for investment promotion in Guanajuato, attended IPC APEX EXPO 2025 at the invitation of IPC Mexico Director Lorena Villanueva, where he met with several companies to discuss the opportunities available in Mexico. He is inviting electronics-related companies seeking long-term investment in a centrally located area with access to highways, railways, and ports.