Why Cleaning Still Matters
June 13, 2018 | Stephen Las Marias, I-Connect007Estimated reading time: 16 minutes
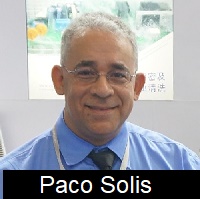
Paco Solis, lead investigator at Foresite Inc., speaks with I-Connect007 about why cleaning is more important now, the common pitfalls and misconceptions in cleaning, and strategies to consider to ensure reliable PCB assemblies.
Stephen Las Marias: Paco, tell us more about Foresite and your role in the company.
Paco Solis: Foresite was started in 1992 in Kokomo, Indiana. Our president, Terry Munson, used to be an engineer at Delphi, originally Delco Systems. He spun off his own company as he saw a need for analysis and education in the PCB and PCBA industries. Primarily, we are a consulting and analysis laboratory. We are a consulting firm that looks into process contamination, failure analysis, and ion chromatography studies.
We do a number of things. We assess customers’ boards, assemblies, and related hardware for cleanliness and reliability, and we also educate our customers as far as how clean their process needs to be for “in-field service” and “long-term reliability”. Part of what we do is test PCBs and PCBAs for cleanliness. Other things we do is rescue cleaning, metallurgical studies, and material analysis studies for failures. We help customers through the process of failure analysis to root cause, remove that failure from the process, and teach them how to recover their product lines. In some ways we teach contamination risk assessment as a consulting firm. Once we have our customers back online, we also perform testing and perform laboratory studies for them to monitor their process and prevent the issue from returning.
Las Marias: As lead investigator, what's your main responsibility?
Solis: It can be anything from walking through a PCB manufacturer and looking for opportunities for improvement to cross-contamination and cleanliness control. It could be helping a customer optimize their wash process for PCBs or PCBAs. Or it could be consulting for what grade of wash water they're using. If I’m going to PCBA assembly house, I'm going to go look at the cleanliness of the PCB and the cleanliness of the discrete devices, I.C.s, and ASICs which go into process. This includes the cleanliness of the stenciling, reflow process (both SMT and wave soldering), and rework processes. We are looking at the many factors of bare-board cleanliness, device cleanliness, solder re-flow and end processes. Because, usually when a PCB fails in the field, its typically is not just one factor. It’s multiple factors. We specialize in understanding semiconductor packaging, PCB and PCB assembly processes. And each time we discover a new failure mechanism, we are adding to our knowledge base. This experience, together with the expertise, is what allows us to help our clients get through their issues even quicker, or prevent those pitfalls altogether, especially if they engage early with us.
Las Marias: What are the biggest challenges that your PCBA customers are facing?
Solis: It comes down to cleanliness education and what is important to pay attention to: inner layer cleanliness of PCBs, electrochemical migration issues, either internal on different inner layers of the PCB, or external layers as well. These materials can be left behind by the PCB manufacturer or introduced at any point in the assembly process. One of the biggest challenges is that the industry has been so pinched that profit margins are very narrow. The customers are demanding Class 2 and Class 3 quality, but they’re not willing to pay for it. These narrowing profit margins are forcing some suppliers to ride the quality levels on the edge of the processes. It is very difficult for a PCB manufacturer to still stay profitable and really get a clean product because their customers are not willing to pay for a clean product. When it’s about profit margin, it’s a very, very, tight rope.
Another issue we're finding is that as a customer orders PCBs, they aren’t communicating enough to their PCB manufacturer what they need. It has become a “build to print” industry. They'll give their contract manufacturer the PCB design and say, “Build to this print.” If the customer that is buying the PCB doesn’t know how to specify what his cleanliness needs are, they don’t know how to relay that information to their suppliers. If they did know, they could specify that on their print, and demand that from the supplier. So, there is an education gap between the end customers, intermediate, and all subsequent tier customers.
What we have learned from the PCB industry is “If I don't tell my PCB contract manufacturer how clean to make it, then it is up to the manufacturer to produce what they normally produce” (their standard preferred in-house process package). If the customer doesn't know how clean he needs his PCB to be, then he has done his supplier a disservice. Each tier in the process needs to communicate their cleanliness needs to the next tier. That is where we come in! We help to bridge the gap of knowledge and education. We help our customers by teaching them how clean their processes need to be so in turn, they can work with their contract manufacturer to develop a PCB that is clean enough for his product. It’s not so straightforward. The PCB industry has many different customers with different cleanliness needs based on their individual products. Here is something I say often to my clients: “There’s a difference between the cheapest thing I can buy, and the best I can afford.” You can apply this to every step to the industry. When you drive costs too close to the quality limits, quality will eventually suffer.
Our customers must work with their contract manufacturers at every tier. For example, discussing sensitive architectures or low standoff architectures in their application. We need more of a technology cooperation between customers and contract manufacturers to understand what cleanliness levels they need in order to produce reliable products for the End Consumer. It’s a break of education and communication right now because it is about profit. Usually our clients become true believers in how important this is after they have been bitten by an avoidable issue which cause all parties a great deal of financial pain. I like to call it “baptized by fire”. After this happens to a client they are more sensitized to future products and will usually work to use the lessons learned.
Las Marias: You said it well. There has to be communication between the designers, assemblers…
Solis: There must be! I was involved with one client where an uneducated decision from a manufacturer to their supplier resulted in an $18 million issue/recall. It was because of a lack of communication of what was needed versus picking a device which was a few cents cheaper. The application and materials in the application required a slightly more expensive device to withstand the end use environment reliably. The issue also could have been avoided if the customer understood their introduction factors and had spec’d lower contaminating materials when they affixed the PCBA into the final assembly.
Las Marias: In our earlier discussion with some solder manufacturers, they say the PCB assembly industry has some sort of misconception when it comes to no-clean. The customers of these contract manufacturers are expecting very sleek looking boards or PCBAs because they thought it’s no-clean. Can you speak to us more about that?
Solis: When the term no-clean came out, it was kind of a misnomer. There is more than one way you can interpret “no-clean.” If you commit to having a no-clean assembly process there are issues which must be understood and concepts you commit to. If you have a no-clean process, you're not cleaning the bare PCB, not cleaning your parts, not cleaning your ASICs, and not cleaning your contributions as well. So, you have to either know the contributors of all your previous tiers or you blindly accept the cleanliness levels of your suppliers. In short, if you decide not to clean your assembly, you have already committed to accepting all previous tier cleanliness issues.
Here is another consideration. The term “no-clean” has been given to the industry as a process without clear expectations and metrics to the final assembly. Much of this comes from flux suppliers who are trying to supply the industry with different solutions for solder reflow needs. The complication is they don’t often have knowledge of how clean the customer’s assembly and end customer’s needs are. The flux suppliers will put their perceived best chemistries forward based on the input from their flux designers and their assembly customers. So, who is supplying the cleanliness needs for the end use product? Sensitive architectures require cleaner processing levels. This may require a flux product with lower levels of activators to attain a reliable end product. This applies for SMT reflow processes the same as it applies to wave and selective solder processes. The knowledge on how to process these fluxes to achieve these higher cleanliness levels also needs to be considered. Again, we have a gap in communication and education. For us at Foresite, no-clean is not a process. No-clean is a decision! It is a decision not to clean my assembly based on empirical data which suggests my product is clean enough to operate reliably in the selected end use environment. So we call no-clean a decision, not a process. It really comes down to an issue of knowledge, on what sensitive architectures and circuits require.
It's not about how cheap I can do this. It's how well I can do it based on my budget. It isn't as simple as “no-clean”. The bigger question is why am I not cleaning? If my application needs are telling me cleanliness is not a first order concern then I can make an educated decision. It means I've decided I'm not going to clean my boards because I know my board supplier is clean. I know my part supplier is clean, and my ASIC supplier is clean, and I know that all my assembly processes are clean enough for my end use requirements. I make this decision on data. Not just a process but one with the proper data.Page 1 of 2
Suggested Items
Heraeus Electronics to Present Pastes for the Next Era of Mobility at SMTA International 2023
09/07/2023 | Heraeus ElectronicsHeraeus Electronics is pleased to announce its participation at SMTA International, a premier event for electronics manufacturing and assembly professionals.
Nihon Superior to Highlight SN100CV P608 Paste at SMTAI
09/06/2023 | Nihon Superior Co. Ltd.Nihon Superior Co. Ltd., an advanced joining material supplier, is pleased to announce that it will exhibit its SN100CV P608 solder paste in Booth #1415 at the SMTA International Exposition, scheduled to take place Oct. 10-11, 2023 at the Minneapolis Convention Center in Minneapolis, MN.
MKS’ Atotech to Participate in SEMICON Taiwan 2023
09/05/2023 | MKS’ AtotechMKS’ Atotech will be participating at the upcoming SEMICON Taiwan, a business matching platform for Taiwan’s semiconductor industry. The event will take place at the TaiNEX Hall 1 and 2 in Taipei, Taiwan, from September 6 – 8.
KYZEN Introduces AQUANOX A4618 with Process Control at SMTA International
09/05/2023 | KYZEN'KYZEN, the global leader in innovative environmentally friendly cleaning chemistries, is excited to announce its participation in the upcoming SMTA International Exposition.
Insulectro Begins Selling EMC & Arlon Laminates Today
09/05/2023 | InsulectroInsulectro, the largest distributor of materials for use in the manufacture of PCBs and printed electronics, ushers in its New Era of Laminates and Prepregs as it begins selling EMC copper clad laminates and Arlon polyimides beginning today.