AT&S Offers Interconnection Tech for Next-Generation 5G Mobile Communications
June 19, 2018 | AT&SEstimated reading time: 2 minutes
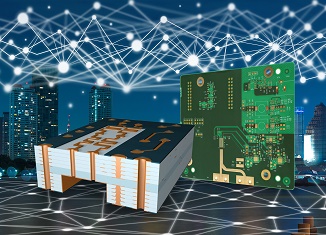
Significantly higher data rates and volumes together with high power densities are resulting in rising requirements for interconnection technologies, too. The new 5G mobile communications generation is undoubtedly an overarching and defining trend here, with applications ranging from infrastructure (base stations) to terminal devices (mobile phones), as well as real-time automation scenarios. AT&S is supporting the current roll-out of the 5G mobile communications generation with high frequency (HF) optimized interconnect solutions and will continue to offer corresponding solutions as the new standard develops.
The launch of the 5G mobile communications generation has far-reaching consequences on the product and system level in terms of miniaturization, functional integration, electromagnetic compatibility (EMC), signal integrity, modularity, safety, security, etc. AT&S therefore analyzed customer requirements and implications for the PCB, substrate and packaging, then initiated and implemented appropriate developments. Innovative solution concepts respond to the challenges of 5G, e.g. using new materials, combining different technologies for hybrid PCB structures, and embedding passive and active circuit components. AT&S invested not only in processes and materials, but also in essential HF measurement equipment to investigate transmission losses, phase shifts and signal delays at up to 100 GHz, for example.
The roll-out of the new 5G mobile communications generation, with frequency bands up to 6 GHz, is already underway. The next step will be to implement 5G millimeter waves with frequencies of 28 GHz or even higher. In principle, for an interconnection technology manufacturer like AT&S, this means reducing signal losses and interference, e.g. by optimizing the dielectric layer in respect of the material (dielectric constant) or thickness, the material transitions (interfaces), or also the copper roughness.
With copper, the major challenge is that while smoother copper offers advantages for HF applications, somewhat greater roughness improves the adhesion of the PCB traces on the basic material. For this reason, AT&S conducted an extensive study of commercially available copper foils for HF applications. The geometry (profile) of the tracks also affects signal delays at higher frequencies and has to be optimized. In addition, AT&S investigated the effects between different metals (copper, gold, nickel) on the skin effect in the GHz range and is developing new surface materials accordingly to get optimized results.
For 5G applications, a hybrid PCB structure combining high-speed layers (HF-optimized) and standard layers represents a performance and cost-optimized solution. AT&S has created a 12-layer hybrid board (HF and FR4 in 2.5D technology) for wireless systems with fully integrated HF antenna. The layers are connected by micro-vias (filled and stacked). Another exemplary HF-optimized solution is a 6-layer board that combines HF layers having a very low dielectric constant with embedded components (application-specific integrated circuits (ASICs) under the antenna structure). The connection between ASICs and antenna is formed by laser-vias.
About AT&S Austria Technologie & Systemtechnik Aktiengesellschaft - First choice for advanced applications
AT&S is the European market leader and one of the globally leading manufacturers of high-end printed circuit boards and IC substrates. AT&S industrialises leading-edge technologies for its core business segments Mobile Devices, Automotive, Industrial and Medical. As an international growth enterprise, AT&S has a global presence with production sites in Austria (Leoben, Fehring) and plants in India (Nanjangud), China (Shanghai, Chongqing) and Korea (Ansan near Seoul). The company employed an average of around 10'000 people in the financial year 2017/18. For further information click here.
Suggested Items
RF PCB Design Tips and Tricks
05/08/2025 | Cherie Litson, EPTAC MIT CID/CID+There are many great books, videos, and information online about designing PCBs for RF circuits. A few of my favorite RF sources are Hans Rosenberg, Stephen Chavez, and Rick Hartley, but there are many more. These PCB design engineers have a very good perspective on what it takes to take an RF design from schematic concept to PCB layout.
Trouble in Your Tank: Causes of Plating Voids, Pre-electroless Copper
05/09/2025 | Michael Carano -- Column: Trouble in Your TankIn the business of printed circuit fabrication, yield-reducing and costly defects can easily catch even the most seasoned engineers and production personnel off guard. In this month’s column, I’ll investigate copper plating voids with their genesis in the pre-plating process steps.
Elephantech: For a Greener Tomorrow
04/16/2025 | Marcy LaRont, PCB007 MagazineNobuhiko Okamoto is the global sales and marketing manager for Elephantech Inc., a Japanese startup with a vision to make electronics more sustainable. The company is developing a metal inkjet technology that can print directly on the substrate and then give it a copper thickness by plating. In this interview, he discusses this novel technology's environmental advantages, as well as its potential benefits for the PCB manufacturing and semiconductor packaging segments.
Trouble in Your Tank: Organic Addition Agents in Electrolytic Copper Plating
04/15/2025 | Michael Carano -- Column: Trouble in Your TankThere are numerous factors at play in the science of electroplating or, as most often called, electrolytic plating. One critical element is the use of organic addition agents and their role in copper plating. The function and use of these chemical compounds will be explored in more detail.
IDTechEx Highlights Recyclable Materials for PCBs
04/10/2025 | IDTechExConventional printed circuit board (PCB) manufacturing is wasteful, harmful to the environment and energy intensive. This can be mitigated by the implementation of new recyclable materials and technologies, which have the potential to revolutionize electronics manufacturing.