-
-
News
News Highlights
- Books
Featured Books
- pcb007 Magazine
Latest Issues
Current IssueThe Hole Truth: Via Integrity in an HDI World
From the drilled hole to registration across multiple sequential lamination cycles, to the quality of your copper plating, via reliability in an HDI world is becoming an ever-greater challenge. This month we look at “The Hole Truth,” from creating the “perfect” via to how you can assure via quality and reliability, the first time, every time.
In Pursuit of Perfection: Defect Reduction
For bare PCB board fabrication, defect reduction is a critical aspect of a company's bottom line profitability. In this issue, we examine how imaging, etching, and plating processes can provide information and insight into reducing defects and increasing yields.
Voices of the Industry
We take the pulse of the PCB industry by sharing insights from leading fabricators and suppliers in this month's issue. We've gathered their thoughts on the new U.S. administration, spending, the war in Ukraine, and their most pressing needs. It’s an eye-opening and enlightening look behind the curtain.
- Articles
- Columns
- Links
- Media kit
||| MENU - pcb007 Magazine
It’s Time to Retire ROSE Testing
June 27, 2018 | Joe Russeau, Precision Analytical Laboratory, and Mark Northrup, IEC ElectronicsEstimated reading time: 3 minutes
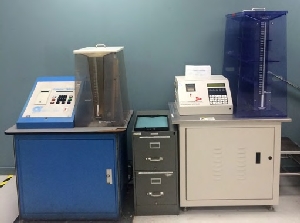
For decades now, the electronics industry has had a growing need to understand the impacts of chemical residues on PCB and PCBA reliability. Residues left from flux and other process chemistries can potentially lead to premature failure of assemblies once in the field. Understanding where such residues originate and their impact on product function is paramount to mitigating product failures due to cleanliness issues. One tool that has been used for decades to evaluate printed board and assembly cleanliness has been the resistivity of solvent extract (ROSE) test.
The ROSE test was developed in the early 1970s by the Naval Avionics Warfare Center in Indianapolis, Indiana. The early test used a squeeze bottle containing a solvent comprised of 75% 2-propanol and 25% deionized water (75/25). The surface of an assembly was rinsed with the 75/25 mixture and any material (e.g., flux) easily soluble in the mixture was dissolved and captured in a beaker. The resistivity of the captured solution was measured, and the result was expressed in terms of sodium chloride equivalents (NaCl eq.). Later versions of the test were automated and a 10.06 microgram (μg) of NaCl eq./in2 (1.56 μg of NaCl eq./cm2) limit was eventually ascribed to the test. That limit became enshrined in various military specifications, such as MIL-P-28809 and WS-6536 and eventually became the industry pass/fail standard. The limit persists today and is used across a wide base of material sets, from bare boards to assemblies to components.
Over the last two to three years, there has been considerable discussion within various IPC committees about the role of the ROSE test in today’s assembly environment. The transition from predominantly water wash processes to “no clean” has meant the advent of very different flux compositions. The question has been posed—on numerous occasions, we might add—as to whether the ROSE test is still a viable option for evaluating PCB and PCBA cleanliness. There have essentially been two camps of thought on the subject: those who want to continue using the test and re-invent it as a process control tool and those that think the test has run its useful course.
To update the test, IPC’s J-STD-001 committee commissioned a subgroup of users and subject matter experts to determine if there was a best-practices use that would bolster its continued application. Two conclusions were reached by that subgroup. First, the ROSE test should no longer be referred to as a cleanliness test, but as a process control tool. This was a reasonable conclusion since ROSE was never meant for cleanliness as industry had defined it. Second, users of the test must provide objective evidence, aside from just ROSE alone, to show that their manufacturing process is in control. More information about what the subgroup defined as “objective” evidence can be found in IPC-WP-019.
The statement made in the title to this article is where we want to focus most of our discussion. We are in the camp that believes the ROSE test provides little value for evaluating today’s assembly products and here’s why. The first significant concern with the validity of the ROSE test is the solvent. Back when the test was developed the predominant flux being used was heavily comprised of rosin (>30%). The 75/25 mixture was a very effective solvent for breaking down that flux and bringing it into solution. This is an important factor to consider because to accurately measure the amount of residual flux on a PCBA, you must first have a solvent that can dissolve it into solution. This is one of the major problems with the ROSE test today.
Why is the solvent an important consideration? Typically, four questions that are asked when performing cleanliness testing of assemblies. The questions are as follows:
1. What types of residues are on the surface of the assembly?
2. What are the concentrations of those residues?
3. Do those residues/concentrations pose any risk to product performance/function?
4. Where are the residues originating?
To have any hope of answering these questions, we need to consider a testing platform with two very specific attributes: selectivity and sensitivity. With the advances in board design, product miniaturization, process improvement and the myriad of chemicals used in assembly production today, a bulk-solvent measurement is not adequate for determining if there are any hidden residue traps.
To read the full version of this article, which appeared in the in the May 2018 issue of SMT007 Magazine, click here.
Suggested Items
The Global Electronics Association Releases IPC-8911: First-Ever Conductive Yarn Standard for E-Textile Application
07/02/2025 | Global Electronics AssociationThe Global Electronics Association announces the release of IPC-8911, Requirements for Conductive Yarns for E-Textiles Applications. This first-of-its-kind global standard establishes a clear framework for classifying, designating, and qualifying conductive yarns—helping to address longstanding challenges in supply chain communication, product testing, and material selection within the growing e-textiles industry.
IPC-CFX, 2.0: How to Use the QPL Effectively
07/02/2025 | Chris Jorgensen, Global Electronics AssociationIn part one of this series, we discussed the new features in CFX Version 2.0 and their implications for improved inter-machine communication. But what about bringing this new functionality to the shop floor? The IPC-CFX-2591 QPL is a powerful technical resource for manufacturers seeking CFX-enabled equipment. The Qualified Product List (QPL) helps streamline equipment selection by listing models verified for CFX compliance through a robust third-party virtual qualification process.
Advancing Aerospace Excellence: Emerald’s Medford Team Earns Space Addendum Certification
06/30/2025 | Emerald TechnologiesWe’re thrilled to announce a major achievement from our Medford, Oregon facility. Andy Abrigo has officially earned her credentials as a Certified IPC Trainer (CIT) under the IPC J-STD-001 Space Addendum, the leading industry standard for space and military-grade electronics manufacturing.
Magnalytix and Foresite to Host Technical Webinar on SIR Testing and Functional Reliability
06/26/2025 | MAGNALYTIXMagnalytix, in collaboration with Foresite Inc., is pleased to announce an upcoming one-hour Webinar Workshop titled “Comparing SIR IPC B-52 to Umpire 41 Functional & SIR Test Method.” This session will be held on July 24, 2025, and is open to professionals in electronics manufacturing, reliability engineering, and process development seeking insights into new testing standards for climatic reliability.
IPC Rebrands as Global Electronics Association: Interview With Dr. John W. Mitchell
06/22/2025 | Marcy LaRont, I-Connect007Today, following a major announcement, IPC is embracing the rapid advancement of technology with a bold decision to change its name to the Global Electronics Association. This name more accurately reflects the full breadth of its work and the modern realities of electronics manufacturing. In this exclusive interview, Global Electronics Association President and CEO Dr. John W. Mitchell shares the story behind the rebrand: Why now, what it means for the industry, and how it aligns with the organization’s mission.