-
- News
- Books
Featured Books
- smt007 Magazine
Latest Issues
Current IssueWhat's Your Sweet Spot?
Are you in a niche that’s growing or shrinking? Is it time to reassess and refocus? We spotlight companies thriving by redefining or reinforcing their niche. What are their insights?
Moving Forward With Confidence
In this issue, we focus on sales and quoting, workforce training, new IPC leadership in the U.S. and Canada, the effects of tariffs, CFX standards, and much more—all designed to provide perspective as you move through the cloud bank of today's shifting economic market.
Intelligent Test and Inspection
Are you ready to explore the cutting-edge advancements shaping the electronics manufacturing industry? The May 2025 issue of SMT007 Magazine is packed with insights, innovations, and expert perspectives that you won’t want to miss.
- Articles
- Columns
- Links
- Media kit
||| MENU - smt007 Magazine
Ryder Industries Empowering All in the Digital Age
July 2, 2018 | Ryder Industries Ltd.Estimated reading time: 3 minutes
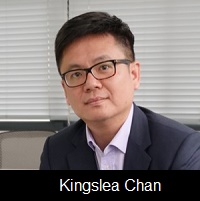
Ryder Industries launches their electronic digital interchange (EDI) platform. Their aim is to solve manufacturing challenges and serve their customers quicker in today’s digitally enabled world.
On the 23rd of May 2018, Ryder Industries officially switched on their new EDI platform to support their long-term partner BOA. Created in collaboration with BOA, Ryder Industries is excited about the possibilities that this improved system will bring to their business.
In a recent interview, Kingslea Chan described BOA as a “strategic customer of Ryder Industries.” BOA and Ryder Industries have a 15-year partnership, and as such, Ryder Industries invests in talent, technology, and processes to support their growing and evolving relationship needs.
The BOA product isn’t traditional EMS business, as guess what, it has no electronic heartbeat. Chan continues; “It’s mainly plastic, nothing electronic, so it’s unique from our traditional customer profile. The scale of the BOA build also takes us out of our traditional low volume / high mix model, as BOA is medium-to-high volume manufacturing with several product configurations. We manufacture in the range of 100,000 units per month, with over ten variations. This type of manufacturing demands responsive supply chain systems and solutions.
We call ourselves an EMS, but really in the case of BOA, we are a manufacturing service provider (MSP). Through time, electronics has become just one component part of our business mix along the entire production lifecycle value chain of; plastic injection moulding, spray painting, Pantone colour mixing, UV coating etc.
Taking the next step into the world of EDI with BOA enables us to serve their needs effectively and efficiently, and it is the next natural stage in the evolution of our continued relationship.
For BOA, EDI will create a reactive supply chain, and for Ryder Industries, we will reduce waste along the same supply chain structure. As a result, yield will improve, and we will operate in real-time with accurate operational data. In turn, this speeds up the entire manufacturing and supply chain process for BOA, whose market is growing at a rapid pace.
We need complete visibility into when outsourced materials will arrive, as well as when the parts we develop in-house, as part of our VI roadmap, will be available to commence the BOA build. Through our new EDI system, both Ryder Industries and our friends at BOA can view the same educational dashboards, achieving not only transparency but supply chain control.
Flexibility is key in the BOA build. The nature of the product requires the ability to scale production volumes up and down as per forecast fluctuations. The system can be accessed by both Ryder Industries and BOA, where a schedule can be loaded and monitored allowing us to scale the manufacturing environment to suit actual requirements, again reducing waste and improving yield.
Unfortunately, one common area of waste within EMS is human error. EDI, of course, decreases this significantly, automating manual functions such as invoicing. Transactions between BOA and Ryder Industries will now transfer electronically, rather than physically, simplifying the process, whilst providing an electronic fingerprint for identification and proof of purchase/receipt.
Developing our EDI system in collaboration with one of our key customers has allowed us to focus on their specific and somewhat unique requirements.
We now have a customised online tool that will enable us to serve their needs better, whilst removing supply chain fragility and potential blockchain issues.
It is an exciting time at Ryder Industries as we continue to expand our potential into new and emerging markets, innovation and technology, whilst increasing our quality, attractiveness and customer satisfaction,” Chan concludes.
About Ryder Industries
Ryder Industries has deep experience in China manufacturing, with some 40 years of operational history, originally as an original equipment manufacturer (OEM) and subsequently as an electronics manufacturing service provider (EMS).
As a Swiss-owned company, we are obsessed with quality, process, and efficiency, and we always deliver what we promise.
We deal with small and large brands, delivering everything from innovation, to volume, from board assembly to complex mechatronics and much more, and our private ownership means we make decisions based on our customers and the industry’s needs. We think long-term.
Ryder Industries offers product introduction, small and medium volumes and, when needed, a gateway to product design, vertical integration, and component sourcing. Our production transitions are seamless because all of our equipment, software, and systems are integrated, offering complete traceability and transparency back to batch.
Our supply chains are kept simple, enabling our customers the flexibility to scale the services to their speed-to-market, time-in-market, and time-in-profit needs.
For further information click here.
Suggested Items
Zollner Completes Full Acquisition of Bluechips Microhouse
07/01/2025 | Zollner Elektronik AGZollner Elektronik AG has successfully finalized its com- plete takeover of Bluechips Microhouse Co., Ltd., in Thailand. In the future the company will operate as part of the Zollner Group of companies under the leadership of Thomas Kiefl – strategically networked, technologically focused and internationally oriented.
Inission Acquires the Lithuanian Company Selteka
07/01/2025 | InissionInission AB has signed an agreement to acquire 100% of UAB Selteka. Selteka is a well-respected EMS (electronics manufacturing services) company with operations located in Kaunas, Lithuania.
Kitron Strengthens Order Backlog with EUR 11 Million Contract for Defense Communication
07/01/2025 | KitronKitron has received an order valued at EUR 11 million to produce advanced military communication products destined for the European market.
TRI Unveils New Multi-Camera AOI, TR7500 SIII Ultra
07/01/2025 | TRITest Research, Inc. (TRI), the leading test and inspection systems provider for the electronics manufacturing industry, proudly introduces the new TR7500 SIII Ultra.
IMI Wins Gold Award for Best Managed Technology Company at FinanceAsia’s 29th Asia’s Best Companies Awards
07/01/2025 | IMIIntegrated Micro-Electronics Inc. (IMI) has been awarded the prestigious Gold Award for Best Managed Technology Company at the 29th edition of the Asia’s Best Companies Awards, hosted by FinanceAsia.