-
- News
- Books
Featured Books
- pcb007 Magazine
Latest Issues
Current IssueInventing the Future with SEL
Two years after launching its state-of-the-art PCB facility, SEL shares lessons in vision, execution, and innovation, plus insights from industry icons and technology leaders shaping the future of PCB fabrication.
Sales: From Pitch to PO
From the first cold call to finally receiving that first purchase order, the July PCB007 Magazine breaks down some critical parts of the sales stack. To up your sales game, read on!
The Hole Truth: Via Integrity in an HDI World
From the drilled hole to registration across multiple sequential lamination cycles, to the quality of your copper plating, via reliability in an HDI world is becoming an ever-greater challenge. This month we look at “The Hole Truth,” from creating the “perfect” via to how you can assure via quality and reliability, the first time, every time.
- Articles
- Columns
- Links
- Media kit
||| MENU - pcb007 Magazine
Estimated reading time: 5 minutes
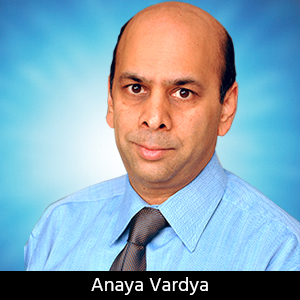
Material Selection: The Key to RF/Microwave Success
Introduction
When discussing the right choice for materials, today’s design engineers are more knowledgeable than during the early years of radio frequency (RF) PCB technology. At that time, only a couple types of low-loss Teflon® materials existed. Today, dozens of controlled dielectric constant (Dk) and low-loss materials are available on the market.
Cost-Benefit Analysis
There is no particular material that will be more effective across the board for every application. There will always be a cost-benefit component to these choices based on performance and functional requirements; total cost must be the guide. Ease of manufacturing, rework, scrap, and reliability must be factored into any material selection decision. As with anything else, saving pennies at the expense of dollars is short-sighted. The initial material cost may be higher than other alternatives, but if the net result is a product that meets design specifications, then it still may be considered the right material (Figure 1).
Figure 1: PCB materials.
Designers of digital logic and RF/microwave products have very different needs, which results in different material requirements. Typically, digital designers are more interested in circuit speed and density. Accordingly, they are primarily interested in thin materials and specific dielectric constants because permittivity is a major concern in the digital world. RF and microwave designers, however, are more interested in frequency-based issues and need materials that help minimize energy loss and provide dielectric uniformity. They also require tight control over material thicknesses and electrical properties; there is special concern with factors such as loss tangent and dielectric constant stability throughout a range of operating conditions.
Two Key Parameters
RF and microwave circuits usually process precision and/or low-level signal transmissions. This means that these circuits require much tighter control of parameters pertaining to signal losses. The two greatest concerns are losses caused by signal reflections due to impedance mismatch, and the loss of signal energy into the dielectric of the material. Material choice (laminate and copper) can have a major impact on all these sources of energy loss. As a result, materials geared to the RF arena tightly control the two key parameters: loss tangent and dielectric constant.
Parameter 1: Loss Tangent
The primary consideration is how much loss a design will tolerate; in other words, how much power in versus how much power out. With an infinite supply of power, loss is unimportant. Adjustments can always be made to compensate for the loss of the materials or conductors. The exception to this is in the heat generated by conductor and return losses; fortunately, this is seldom a reality.
Parameter 2: Dielectric Constant
The primary consideration is the required dielectric material thickness and conductor width to achieve a given impedance value. This turns into a copper loss and power handling issue. The secondary issue is the ability to dissipate the heat that occurs both at the power device(s) and in the conductors. This heat needs to be transmitted somewhere, and the materials need to have a low dielectric constant or thick conductor widths—enough to carry whatever power the circuitry requires.
A careful consideration of these two parameters will provide guidance to the proper material type and thickness required for the PCB being designed. It’s all about signal speed (Figure 2.)
Figure 2: Signal speed is key to performance.
Dimensional Stability
An understanding of dimensional stability—how materials react under operating conditions—is also important when making selections for an RF PCB. There are three types of materials that relate to dimensional stability:
- Homogeneous: Material of uniform composition throughout that cannot be mechanically separated into different materials, such as plastic, glass, and resin.
- Isotropic: Material with properties that are equal in all directions (X, Y, and Z), such as glass microfiber RT/duroid®.
- Anisotropic: Material with properties that might vary depending on direction, such as woven glass fabric in traditional FR-4 and certain glass fabric-reinforced PTFE materials.
Best Practices for Material Selection
There are several best practices that will help a designer choose the right laminate substrate and copper foil for high-frequency RF applications:
- Match dielectric constants: In RF PCB design, a Dk match is highly desired. If a PCB substrate is made of resin and woven material, they may have different Dks. Non-uniform Dks in a substrate may cause problems. Working with the PCB fabricator will assure as close a Dk match as possible in all of the substrates being considered.
- Match coefficient of thermal expansion (CTE): The degree of expansion in response to temperature increase is important on its own, but it can also impact the function of the PCB. Differing CTEs of the laminate substrate layers in a PCB will expand at different rates during fabrication or operation, which can create functional failures and reliability concerns.
- Tight substrate weave: The woven properties of the laminate substrate need to mesh tightly and may directly impact Dk. Working with the PCB fabricator will help avoid choosing a material set that may negatively impact performance.
- FR-4: It must be understood that if FR-4 is used for high-frequency applications; it will not have the same level of precise dielectric constant and thickness control as specially formulated RF material.
- Use a smooth foil: A smooth copper foil will ensure lower resistive losses at extremely high frequencies.
One must also consider skin effect. At high signal frequencies, the current in a PCB copper circuit is concentrated within a small depth near its surface, which is referred to as the skin effect or skin depth. Skin depth is a measure of how and where electrical conduction takes place in a conductor and is a function of frequency (Figure 3).
Figure 3: Skin depth calculation. (Courtesy of Isola)
Conclusion
In today’s environment, there are a number of suppliers that may have similar materials but price points and lead times may vary. If you are open to trying different options, it is a good idea to work closely with your PCB fabricator so they can educate you on these aspects. Another option is to do parallel builds with multiple materials in the early stages of honing a new design to determine the optimum material set.
Anaya Vardya is the CEO and president of American Standard Circuits and John Bushie is the director of technology.
Visit i-007eBooks to download your copies of American Standard Circuits' micro eBooks today:
The Printed Circuit Designer's Guide to...Fundamentals of RF/Microwave PCBs
The Printed Circuit Designer's Guide to...Flex and Rigid-Flex Fundamentals
More Columns from Standard of Excellence
Standard of Excellence: Training Your Team to Excel in Customer ServiceStandard of Excellence: Delivering Excellence—A Daily Goal
Standard of Excellence: The Role of Technology in Enhancing the Customer Experience
Standard of Excellence: Turning Negative Customer Feedback Into Positive Outcomes
Standard of Excellence: Anticipating Customer Needs Early and Often
Standard of Excellence: The Power of Personalization in Customer Care
Standard of Excellence: Building Trust with Customers—The Foundation of Excellent Service
Standard of Excellence: Finding and Developing Future Leaders in Manufacturing