IMPACT Washington D.C., 2018 with Juki Automation’s Bill Astle
August 1, 2018 | Patty Goldman, I-Connect007Estimated reading time: 8 minutes
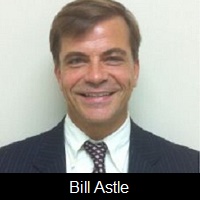
I caught up with Juki Automation’s Bill Astle during a luncheon on the last day of IMPACT Washington D.C., 2018. As a first-time attendee, Bill came away feeling like he made the right connections with key members of Congress, and he looks forward to returning to the event in the future.
Patty Goldman: Bill, please begin by telling our readers a bit about your background, as well as the history of Juki Automation Systems Inc., or JAS.
Bill Astle: I've been in the electronics industry for longer than I want to admit—30+ years now, starting out as a hands-on engineer from the beginning. I brought in surface mount equipment for Hamilton Standard, now Hamilton Sundstrand, right out of college and was thrown into this high-technology electronics assembly building circuit boards for Pratt and Whitney's jet engines. I was born in South Carolina, but I was raised in New England and went to University of Massachusetts, where I received my undergraduate degree in Mechanical Engineering. Fresh out of college, at just 21, I joined Hamilton Standard in Windsor Locks, Connecticut, where I met. Bob Black who had sold them an early vintage machine called an HBA (Hybrid Assembly), one of the first SMT mounters that offered the automated placement capability, and real time in-flight electrical testing of the chip SMDs required by most of the customers of high reliability aerospace PCBAs.
In the very beginning, I visited MPM Speedline, or MPM in those days, when they were just a few years old and literally in a garage. I brought in one of their screen printers to Hamilton and learned it very well. I also learned all about vapor phase reflow technology. That reflow technology transitioned out of the industry, but it's coming back. My relationship with Juki Automation Systems also started very early in my career, in fact before Juki acquired Zevatech. I bought pick-and-place machines from Zevatech in 1985, and quickly learned to program all of the SMDs of the day. Back then a 1206 SMD was state-of-the art. Bob Black was the president at that time, and he is now a senior advisor for Juki. He promoted me to take his place as the president and CEO of Juki Automation Systems Inc. After working in the Aerospace SMT segment with Hamilton, I moved into the computing industry by joining Digital Equipment Corporation (DEC). At both Hamilton and DEC, I was fortunate enough to be sent out in the field to attend several SMT industry trade shows, as well as many SMT technology learning seminars. I was then given the checkbook to go out and buy the next generation of SMT assembly equipment, everything from printers to in-circuit testers (ICTs). Over the years I've progressed through positions involved with fundamental SMT process engineering, product management, sales management, general management, and now I am the acting President & CEO of JAS.
As for Juki, it is a world leader in two industries. Our premier industry is industrial and home sewing machines. We're a billion-dollar international company, and our electronics assembly division, which I'm part of, is about one third of our revenue. We're a public company, very innovative, and we pride ourselves on excellent customer support and competitive products. Our core fundamental product is a pick-and-place machine. I would say there are three Japanese companies that comprise about 60% of the market, and then there's ASM, probably another 15-20%, with Fuji, Panasonic, and Juki being the top three. Also, Yamaha is in that mix to round out the top five pick-and-place manufacturers.
Goldman: Juki is a Japanese company, but are you CEO of the Americas?
Astle: We're a subsidiary of the headquarters and our own entity, if you will. We are Juki Automation Systems Inc., and there's also Juki Corporation, of which we are a part. Our headquarters is located in Tokyo, and the pick-and-place mounters are manufactured under strict quality standards in several factories located across Japan. For complete Smart SMT line solutions we have partnered with world class partners. We provide screen printers from GKG marketing those in the Americas; they're the world leader in printers these days and they are headquartered out of Dongguan, China. We have also brought in a complete line of forced-convection reflow ovens from JT Universal, also in the Shenzhen China area, selective and stamp soldering machines from Inertec in Germany, and the best intelligent storage management (ISM) solutions which automatically stores and pulls kits of SMDs. We also provide complete material handling solutions, such as magazine handlers, buffer conveyors, and inspection conveyors, etc., as part of solutions.
Goldman: Juki offers a complete solution, shall we say?
Astle: Magazine to magazine, that's right. We have complete SMT line offerings and to augment the SMT lines, we also offer selective and stamp soldering for the odd-form, and standard through-hole components. Our odd form insertion machine is called the JM20. It will place all sorts of PTH connectors, headers, coils, transformers, E-Caps, etc. Most any part that can't be placed by the SMT machines can be placed or inserted using the JM20. Then we have our intelligent storage management systems. The ISMs automates the storage, retrieval and MSD control of the parts used on today’s PCBAs.
Normally, you would send an operator off to the warehouse and say, "Here’s the bill of materials for some 200 different part numbers. I need this quantity of each one of those. We'll see you in three or four hours. Come back with a kit.” Well, those times have changed. We now automate the kit pull within a system very similar to a Redbox—just like videos. We can literally send a bill of materials either from a clients’ ERP system, or from the pick-and-place mounters, of most any brand, directly to our ISM towers. The ISMs will then automatically pull and stack up to (54) 8mm reels at one time. The operator can put in the kit pull command to the ISM, and 12-15 minutes later, come back to a stacked pick list of up to 54 reels at once. Multiple stack pulls are used when BOMs exceed 54 unique part numbers, and these days we are seeing of upwards of 300 unique part numbers. Can you imagine how long it takes to pull a kit of that magnitude by hand? The ISM also tracks inventory and can connect to X-ray counters, ERP software or intelligent mounters to update parts counts in real time. In order to maximize SMT line utilization, its mission critical to have the correct parts, in the correct quantities, at the correct place, just in time for change over. You would be very surprised how many times lines go down for lack of parts, missing parts, and delays due the slow manual process of kit pulls.
Goldman: That's a huge savings in time, and I would guess labor savings, also.
Astle: Absolutely, it is, and it’s a floor savings. Humans make errors, unfortunately. Part numbers are beginning to be 30 characters long, so it's easy to make a mistake.
Goldman: Is this your first time at IMPACT?
Astle: Yes, it is.
Goldman: What are your impressions?
Astle: I'm very happy with the organization of the event, with the meetings that have been set up, with the U.S. Senate and Congress; the topics are very important to the U.S. The circuit board industry, as you know, has experienced a lot of offshoring. We've kept NPIs and the higher technologies here, but there's a real lack of capacity for building the circuit boards themselves, and this is the topic we've been bringing up to the delegates.
Goldman: If you aren't here and you aren't talking to them, how can you get the word out?
Astle: That's right. It's surprising how some of the delegates don't know a lot about our industry. They know what a circuit board is certainly, but they don't know the difference between semiconductor, second level packaging and SMT. I was able to explain a little bit of that, one-on-one, with Congressman David Price of North Carolina, and in fact, he now wants to come over and visit Juki.
Goldman: That's good to hear.
Astle: He was very engaging. In fact, I was telling John Mitchell, president of IPC, that we were invited to have a hearing. If we're serious about our issues he said, "No problem, I can get you in front of the delegates, and we'll have a hearing and they'll listen to your concerns and that's really the way to take it to the whole team." So, that was very encouraging. I had a one-on-one with the congressman. There was no one else there except a couple of his aides.
Goldman: How perfect is that?
Astle: I really put on my articulation shoes. I worked on the Joint Advanced Fighter Engine program when I was first at Hamilton Standard; on the military side. So, to see some of the infiltration of the adversary’s chips in our defensive board sets, and the basic inability to produce enough PCBAs in a crisis is alarming.
Goldman: And it’s good to get that alarm across to the right people.
Astle: I will work to make more delegate connections, and I will follow through with the NC Senator for sure.
Goldman: Excellent. Are you going to come to another IMPACT?
Astle: Oh, absolutely. I'll be better prepared and now I know where I'm going on Capitol Hill as this was my first time attending IMPACT.
Goldman: In the meantime, you'll have had a visit to your facility which is invaluable—showing is so much better than telling.
Astle: Absolutely.
Goldman: Anything else you'd like to talk about here?
Astle: I'm very excited to lead the organization to new heights. I think Juki is a wonderful company. We’re really a family and the distributorships and partnerships around the world are growing substantially. I'd like to thank my former boss, the honorable Mr. Bob Black, who gave me this opportunity to lead, and grow the organization. Juki is very innovative, and we will come with even better products and services in the near future in our drive to be the number one vendor of choice in all SMT.
Goldman: Super. Thank you very much.
Astle: I appreciate it. Thank you. It's been a pleasure.
Suggested Items
TT Electronics Secures £20 Million in Aerospace and Defence Contracts as European Programmes Accelerate
06/06/2025 | TT ElectronicsTT Electronics has been awarded more than £20 million in new and renewed defence contracts, marking a major step forward in its contribution to Europe’s rapidly evolving defence landscape.
Elma Electronic Bolsters Quality Management Company-wide with Added AS9100:D and ISO9001:2015 Certifications
06/02/2025 | Elma ElectronicElma Electronic now includes AS9100:D and ISO 9001:2015 certifications at its Horsham, Pa. manufacturing facility, earning the company a multiple site accreditation designation.
See TopLine’s Next Gen Braided Solder Column Technology at SPACE TECH EXPO 2025
05/28/2025 | TopLineAerospace and Defense applications in demanding environments have a solution now in TopLine’s Braided Solder Columns, which can withstand the rigors of deep space cold and cryogenic environments.
ICEFlight to Accelerate Maturation of Cryogenic Technologies for Hydrogen-Powered Flight
05/27/2025 | GKN AerospaceGKN Aerospace is one of the project partners in ICEFlight (Innovative Cryogenic Electric Flight), a project aiming to contribute to the development of hydrogen-powered flight.
Vertical Aerospace Makes Aviation History with Piloted eVTOL Flight in Open Airspace
05/27/2025 | BUSINESS WIREVertical Aerospace, a global aerospace and technology company that is pioneering electric aviation, announced it has made European aviation history with the first-ever piloted wingborne flight of a winged electric vertical take-off and landing (eVTOL) aircraft in open airspace.