-
-
News
News Highlights
- Books
Featured Books
- smt007 Magazine
Latest Issues
Current IssueWhat's Your Sweet Spot?
Are you in a niche that’s growing or shrinking? Is it time to reassess and refocus? We spotlight companies thriving by redefining or reinforcing their niche. What are their insights?
Moving Forward With Confidence
In this issue, we focus on sales and quoting, workforce training, new IPC leadership in the U.S. and Canada, the effects of tariffs, CFX standards, and much more—all designed to provide perspective as you move through the cloud bank of today's shifting economic market.
Intelligent Test and Inspection
Are you ready to explore the cutting-edge advancements shaping the electronics manufacturing industry? The May 2025 issue of SMT007 Magazine is packed with insights, innovations, and expert perspectives that you won’t want to miss.
- Articles
- Columns
- Links
- Media kit
||| MENU - smt007 Magazine
The Impact of Industry Regulations on Your Supply Chain
August 23, 2018 | Neil Sharp, JJS ManufacturingEstimated reading time: 3 minutes
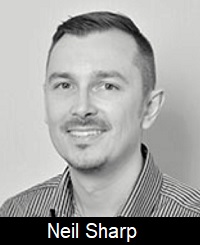
A responsible electronics manufacturing services (EMS) provider will always make it a priority to keep customers abreast of any industry regulation that could have an impact on the manufacture of their product.
Changes and updates to existing legislation is an ongoing process, and the introduction of new rules is inevitable.
So, it’s vital that your assembly partner is committed to staying up to date and to keeping you informed of how these changes may impact your manufacturing supply chain.
Within Europe, the production of electronic equipment is governed by several key European Union (EU) directives, which are designed to regulate the use of chemical substances and the handling of waste products:
- The Restriction of Hazardous Substance Directive (RoHS)
- The Registration, Evaluation, Authorization and Restriction of Chemicals (REACH)
- The Waste Electrical and Electronic Equipment (WEEE) Directive
Recent developments within the Conflict Minerals Legislation, which will come into force in 2021, are also likely to impact how manufacturers source, and import, certain minerals and metals.
The RoHS Directive
The RoHS Directive covers the manufacture, import and distribution of most electrical and electronic equipment (EEE) and is primarily aimed at regulating levels of hazardous substances such as mercury, lead, cadmium and hexavalent chromium and flame retardants.
Any component or sub-assembly that falls within the scope of the Directive is required to have a Declaration of Conformity, must be accompanied by a supporting technical file that demonstrates compliance, must be appropriately marked (including type, batch, serial number and manufacturer details) and must display the European Conformity (CE) label.
If a product is suspected to be non-compliant then the onus is on your assembly partner to notify the Market Surveillance Authorities (MSAs) and to inform the supply chain. They're also required to maintain a register of any identified non-conformities, which must be kept for 10 years.
REACH
REACH is a European Union regulation which came into force in 2007. Its role is to provide a high level of protection for individuals and the environment from the use of chemicals, to educate manufacturers and importers of chemicals in understanding how to manage risks and to allow the free movement of chemicals within the EU market.
By 1 June 2018, any substance that has been pre-registered will need to be registered if its manufacture or import will be in quantities of 1 ton per annum or more.
For assembly providers, this means probing their supply chain to ensure that all substances that are key to their business meet the REACH requirements.
WEEE Regulations
Any manufacturer of electrical and electronic equipment responsible for placing products onto the market must abide by the Waste Electrical and Electronic Equipment (WEEE) Regulations, which came into force in 2003.
The regulations aim to increase the treatment and recovery of waste products and to reduce the amount of waste that goes to landfill by setting collection, recycling and recovery targets.
Any company that produces WEEE is required to join an approved producer compliance scheme (PCS), which then acts as a link between producers and environment agencies. Producers are responsible for labeling all products accordingly to allow for correct disposal—and for meeting the cost of the collection and processing of their waste materials.
Conflict Minerals Legislation
Since 2010, American companies have been required to audit their supply chains to ensure that they are not using any conflict minerals—particularly tantalum, gold, tin and tungsten—which originate from the eastern provinces of the Democratic Republic of Congo (DRC) and surrounding areas.
The Organization for Economic Cooperation and Development (OECD) has written extensively on the subject.
In May 2017, the European Union passed a new regulation (which will come into effect in January 2021), which will stop the export of conflict minerals and metals into the EU and that will require EU companies to demonstrate that they import metals and minerals from responsible sources only.
How Your EMS Partner Can Help
A responsible assembly partner, and its procurement team, understands the importance of keeping track of regulations and of having processes in place to take appropriate action when it’s needed.
Before production gets underway, it will scrutinize your bill of materials (BOM), to ensure that all of the parts are compliant with the latest regulations. And it will offer guidance (and viable alternatives) if it believes that any item may need to be modified or replaced.
Finally, if a regulatory change is about to come into effect, your EMS provider will take all necessary measures to keep you informed so that production continues unimpeded and to-plan.
Suggested Items
Solving the UK Manufacturing Productivity Puzzle
11/30/2018 | Russell Poppe, JJS ManufacturingSince the financial crisis of 2008, manufacturing has seen an undeniable slump. Latest industry statistics paint a pretty compelling picture—where once the UK manufacturing sector was hot on the heels of its international counterparts, it now lags behind with average annual growth of less than 1% a year since the advent of the financial crisis. This article looks at five issues that could help to inform our decisions and boost performance within the sector.
How Effective is Your Induction Process?
11/23/2018 | Neil Sharp, JJS ManufacturingThis article looks at eight ways manufacturers can ensure their induction process passes the 'so what' test. And more importantly, addresses all of the questions and concerns a new starter might have during their first couple of days.
Managing Cyber-Threats Within Electronics Manufacturing
11/16/2018 | Neil Sharp, JJS ManufacturingThe rise of the 4th Industrial Revolution (4IR) has brought with it digital interconnectivity that offers unprecedented opportunities for original equipment manufacturers (OEMs). But with that openness there also comes risk—the threat of the loss of data, the theft of capital or intellectual property, and the disruption of access to systems or operational technology—all of which can impede businesses and impact on trade.
4 Questions OEMs Typically Ask When Outsourcing
11/08/2018 | Neil Sharp, JJS ManufacturingThe decision to transfer your electronics manufacturing to an EMS company is a complex process, with the potential to impact your business, your staff, your customers and your suppliers in a multitude of ways. This article highlights four questions OEMs typically ask prospective contract manufacturing partners when they first start engaging with them—and our take on the answers.
Pros and Cons of Dual Sourcing
11/01/2018 | Neil Sharp, JJS ManufacturingNow, more than ever, there's a need for responsive and flexible supply chains. For OEMs, one solution to mitigate the risk of supply chain disruption is to maintain relationships with more than one supplier through dual sourcing—the practice of purchasing a chosen raw material, product, or service from two (or sometimes multiple) sources. Here are it's pros and cons.