-
- News
- Books
Featured Books
- pcb007 Magazine
Latest Issues
Current IssueThe Hole Truth: Via Integrity in an HDI World
From the drilled hole to registration across multiple sequential lamination cycles, to the quality of your copper plating, via reliability in an HDI world is becoming an ever-greater challenge. This month we look at “The Hole Truth,” from creating the “perfect” via to how you can assure via quality and reliability, the first time, every time.
In Pursuit of Perfection: Defect Reduction
For bare PCB board fabrication, defect reduction is a critical aspect of a company's bottom line profitability. In this issue, we examine how imaging, etching, and plating processes can provide information and insight into reducing defects and increasing yields.
Voices of the Industry
We take the pulse of the PCB industry by sharing insights from leading fabricators and suppliers in this month's issue. We've gathered their thoughts on the new U.S. administration, spending, the war in Ukraine, and their most pressing needs. It’s an eye-opening and enlightening look behind the curtain.
- Articles
- Columns
- Links
- Media kit
||| MENU - pcb007 Magazine
PCB Design, Fabrication and Use from the Mil-Aero End-User Perspective
August 28, 2018 | Pete Starkey, I-Connect007Estimated reading time: 13 minutes
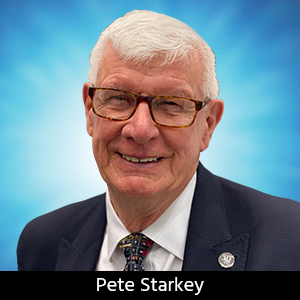
How do leading military and aerospace electronics end-users define their high-reliability printed circuit board requirements? How do they specify their materials? What factors determine their design rules? How do they deal with impedance control? What are their preferred solderable finishes? How do they qualify a new design? And when PCBs are delivered, what are their incoming inspection and quality standards, and how are the boards tested? How are PCBs handled and what precautions are taken to control moisture absorption?
The answers to these and many more questions were provided by a webinar organised by the European chapter of SMTA, moderated by Bob Willis and presented by two industry experts with whom I had the privilege of working for many years on the SMART Group technical committee and latterly as members of the SMTA Europe technical committee: Charles Cawthorne, industrial electronics technologist with MBDA Systems, and Ian Fox, electronics materials and process specialist with Rolls Royce. Their input exemplified the standards and practices adopted by a manufacturer of missile systems and a manufacturer of aero-engine controls and characterised the typical requirements of the hi-rel mil-aero sector.
The first part of the webinar was delivered by Charles Cawthorne, who reviewed the basic fabrication steps for a sequential-build 10-layer PCB as an introduction to a discussion of laminates, prepregs, copper foils and flex-rigid materials, and various aspects of design including via protection and controlled impedance.
The defining specification for base materials for rigid and multilayer printed circuit boards was IPC-4101, with its associated slash sheets defining resin and reinforcement systems, testing parameters and properties. Cawthorne quoted examples of FR-4 materials that demonstrated different glass transition temperatures (Tg), the baseline being IPC-4101/21 with a 110°C minimum Tg. In fact, MBDA specified IPC-4101/126, with a 170°C minimum Tg. But was it sufficient simply to define a Tg? Cawthorne stressed the importance of considering Z-axis coefficient of thermal expansion (CTE), especially above Tg, and explained that MBDA required a Z-axis TCE of less than 60ppm/°C below Tg and less than 300ppm/°C above Tg. Additionally, MBDA required a decomposition temperature (Td) no less than 325°C and a time to delamination at 260°C (T260) of no less than 30 minutes.
For operating temperature above about 130°C, polyimide materials were preferred, example grades being IPC-4101/40, with Tg of 200°C minimum, and IPC-4101/41 with Tg of 250°C minimum, but these materials were significantly more expensive than FR-4.
The defining standard for copper foils was IPC-4562. Cawthorne explained the meaning of the full specification sheet designation, taking as example a typical foil used by MBDA for outer layers: IPC-4562A/3 CuE3HSXS3, where /3 was the IPC-4562 Spec Sheet Number, Cu denoted copper, E indicated electrodeposited, 3 signified high temperature elongation, H indicated half-ounce thickness, S stood for single-sided bond enhancement, XS indicating that this was standard profile, and the final 3 referred to highest quality.
For the additional materials required for flex-rigid multilayer constructions, no flow prepreg was defined by IPC-4101/40, 41 or 42, flex cores by IPC-4204, and coverlays and bond-plies by IPC-4203. MBDA typically used polyimide-based adhesiveless flex cores in accordance with IPC-4204/11.
Cawthorne moved on to a discussion of surface mount design rules, beginning with component footprints for which the defining standard was IPC-7351. This considered three density levels, where Level A represented the largest footprint and Level C the smallest. MBDA used a software-based footprint calculator to optimise design for manufacture, and generally chose to work at Density Level B to give the best compromise between ease of manufacture and minimum footprint area.
The defining standards for PCB layout were the generic IPC-2221 and the sectional standards IPC-2222, IPC-2223 and IPC-2226. There had been lengthy discussion on the relative merits of solder-mask-defined or non-solder-mask-defined BGA pads, and MBDA considered the latter a more reliable option. Concerning offset vias, their preference was to ensure that solder resist was present between BGA pad and via to prevent wicking of solder away from the joint.
The defining standard for PTH footprints was IPC-7251, which covered three density levels, Level A being for the largest hole diameter and Level C the smallest. Historically, MBDA had used Level B or Level C for tin-lead but experience had shown that the PTH diameter needed to be increased for lead-free and Level A had now been adopted for both tin-lead and lead-free soldering. Standard maximum aspect ratio for plated-through holes was 6:1 for rigid boards and 5:1 for flex-rigid. For buried vias, minimum aspect ratios were 7:1 for rigid boards and 6:1 for flex-rigid, with minimum diameter 0.25 mm depending on current handling requirements.
Page 1 of 3
Suggested Items
KYZEN to Highlight Understencil and PCB Cleaners at SMTA Querétaro Expo and Tech Forum
07/09/2025 | KYZEN'KYZEN, the global leader in innovative environmentally responsible cleaning chemistries, will exhibit at the SMTA Querétaro Expo & Tech Forum, scheduled to take place Thursday, July 24, at Centro de Congresos y Teatro Metropolitano de Querétaro.
Driving Innovation: Direct Imaging vs. Conventional Exposure
07/01/2025 | Simon Khesin -- Column: Driving InnovationMy first camera used Kodak film. I even experimented with developing photos in the bathroom, though I usually dropped the film off at a Kodak center and received the prints two weeks later, only to discover that some images were out of focus or poorly framed. Today, every smartphone contains a high-quality camera capable of producing stunning images instantly.
Hands-On Demos Now Available for Apollo Seiko’s EF and AF Selective Soldering Lines
06/30/2025 | Apollo SeikoApollo Seiko, a leading innovator in soldering technology, is excited to spotlight its expanded lineup of EF and AF Series Selective Soldering Systems, now available for live demonstrations in its newly dedicated demo room.
Indium Corporation Expert to Present on Automotive and Industrial Solder Bonding Solutions at Global Electronics Association Workshop
06/26/2025 | IndiumIndium Corporation Principal Engineer, Advanced Materials, Andy Mackie, Ph.D., MSc, will deliver a technical presentation on innovative solder bonding solutions for automotive and industrial applications at the Global Electronics A
Fresh PCB Concepts: Assembly Challenges with Micro Components and Standard Solder Mask Practices
06/26/2025 | Team NCAB -- Column: Fresh PCB ConceptsMicro components have redefined what is possible in PCB design. With package sizes like 01005 and 0201 becoming more common in high-density layouts, designers are now expected to pack more performance into smaller spaces than ever before. While these advancements support miniaturization and functionality, they introduce new assembly challenges, particularly with traditional solder mask and legend application processes.